Tool coating methods are essential for enhancing the performance, durability, and efficiency of tools, particularly in industrial and manufacturing applications. Among the most widely used techniques are Physical Vapor Deposition (PVD) processes, which include evaporating, sputtering, and reactive ion plating. These methods are further refined through advanced technologies such as arc evaporation, magnetron sputtering, plasma-enhanced magnetron sputtering, CAM (coating assisted by microwaves), and modified arc evaporation. Each method offers unique advantages and is selected based on the specific requirements of the tool and its intended application.
Key Points Explained:
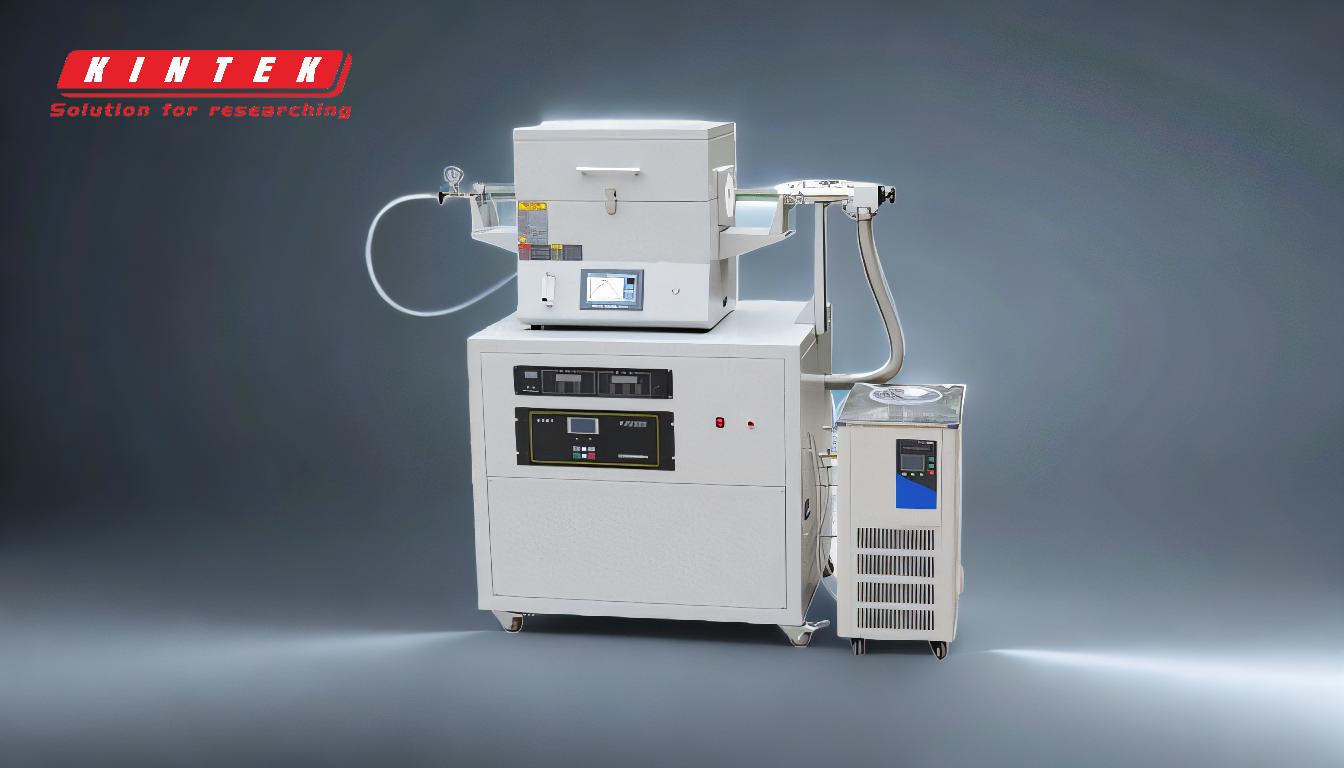
-
Physical Vapor Deposition (PVD) Processes:
- Evaporating: This method involves heating the coating material until it vaporizes, allowing it to condense on the tool's surface. It is widely used for creating thin, uniform coatings with excellent adhesion.
- Sputtering: In this process, high-energy ions bombard the target material, causing atoms to be ejected and deposited onto the tool. It is known for producing dense and high-quality coatings.
- Reactive Ion Plating: This technique combines evaporation with a reactive gas to form a compound coating on the tool. It is particularly effective for creating hard, wear-resistant coatings.
-
Advanced PVD Coating Methods:
- Arc Evaporation: This method uses an electric arc to vaporize the coating material, resulting in high ionization rates and dense coatings. It is ideal for applications requiring high adhesion and durability.
- Magnetron Sputtering: By using a magnetic field to enhance the sputtering process, this method achieves higher deposition rates and better control over coating properties.
- Plasma-Enhanced Magnetron Sputtering: This variation incorporates plasma to further improve coating density and uniformity, making it suitable for precision tools.
- CAM (Coating Assisted by Microwaves): This innovative approach uses microwave energy to enhance the coating process, offering improved efficiency and control over coating characteristics.
- Modified Arc Evaporation: This method refines traditional arc evaporation by optimizing parameters such as arc current and gas pressure, resulting in superior coating quality.
-
Selection Criteria for Coating Methods:
- Tool Material and Geometry: The choice of coating method depends on the tool's material and shape. For example, complex geometries may benefit from methods like magnetron sputtering, which provides excellent coverage.
- Application Requirements: Different applications demand specific coating properties, such as hardness, wear resistance, or thermal stability. Reactive ion plating, for instance, is ideal for high-wear environments.
- Cost and Efficiency: Advanced methods like CAM and modified arc evaporation may offer cost savings and faster processing times, making them attractive for high-volume production.
-
Benefits of PVD Coatings:
- Enhanced Tool Life: PVD coatings significantly extend the lifespan of tools by reducing wear and corrosion.
- Improved Performance: Coatings can enhance tool performance by reducing friction, improving thermal stability, and increasing hardness.
- Versatility: PVD methods can be applied to a wide range of materials, including metals, ceramics, and composites.
In conclusion, the choice of tool coating method depends on factors such as the tool's material, geometry, and intended application. PVD processes, including evaporating, sputtering, and reactive ion plating, along with their advanced variations, offer a versatile and effective solution for enhancing tool performance and durability. By understanding the unique advantages of each method, manufacturers can select the most appropriate coating technique to meet their specific needs.
Summary Table:
Coating Method | Key Features | Best Applications |
---|---|---|
Evaporating | Thin, uniform coatings with excellent adhesion | General-purpose tools requiring consistent coating thickness |
Sputtering | Dense, high-quality coatings | Tools requiring high durability and precision |
Reactive Ion Plating | Hard, wear-resistant coatings | High-wear environments and tools exposed to harsh conditions |
Arc Evaporation | High ionization rates, dense coatings | Applications requiring high adhesion and durability |
Magnetron Sputtering | Higher deposition rates, better control over coating properties | Complex geometries and precision tools |
Plasma-Enhanced Magnetron Sputtering | Improved coating density and uniformity | Precision tools with stringent performance requirements |
CAM (Coating Assisted by Microwaves) | Enhanced efficiency and control over coating characteristics | High-volume production with cost and time savings |
Modified Arc Evaporation | Superior coating quality through optimized parameters | Tools requiring the highest level of performance and durability |
Ready to enhance your tools with the right coating method? Contact our experts today to find the perfect solution!