Biomass conversion technologies are broadly categorized into thermochemical and biochemical methods, each with distinct processes and applications. Thermochemical methods include combustion, gasification, and pyrolysis, which involve the application of heat to convert biomass into energy or fuel. Biochemical methods, such as anaerobic digestion and fermentation, utilize microorganisms to break down biomass into biofuels like ethanol and renewable natural gas. These technologies play a crucial role in sustainable energy production, offering alternatives to fossil fuels and reducing greenhouse gas emissions.
Key Points Explained:
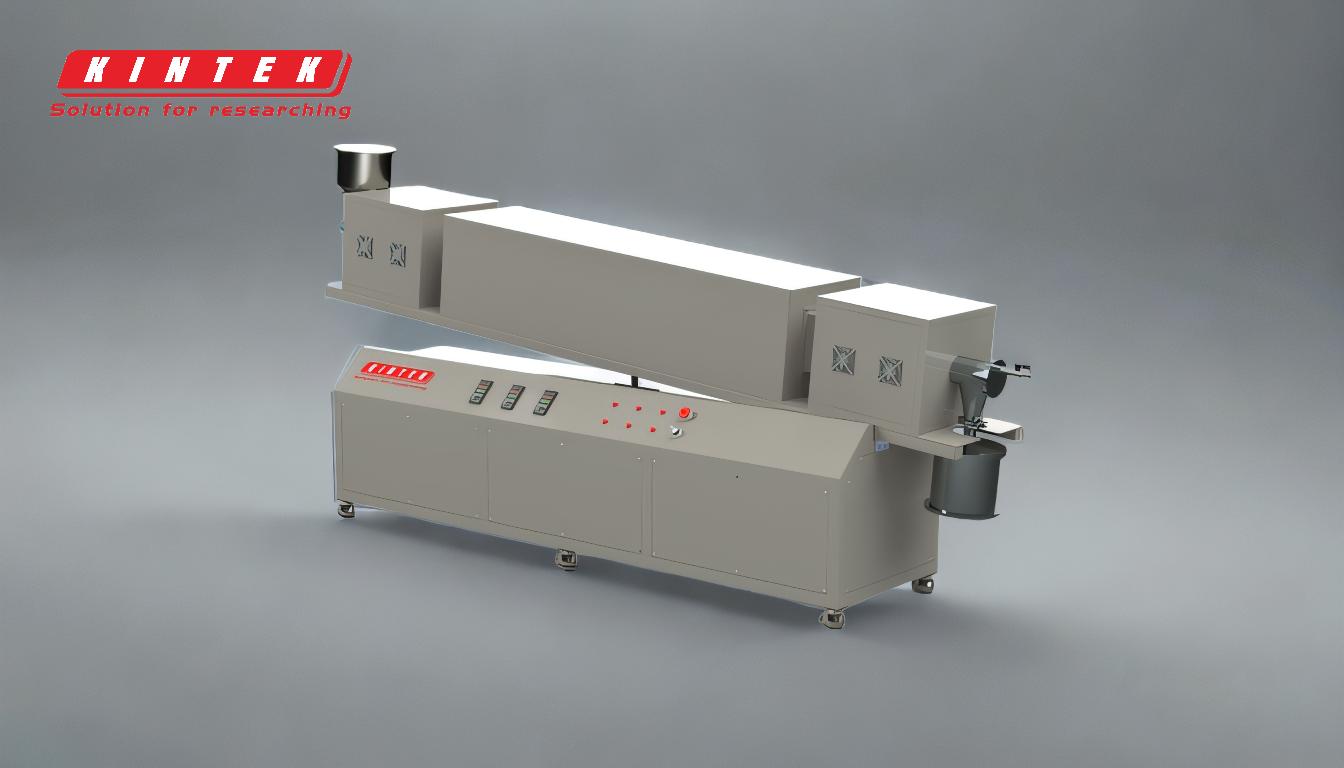
-
Thermochemical Conversion Methods:
- Combustion: This is the most common method where biomass is burned directly to produce heat, which can then be used to generate electricity or provide heating. It is a straightforward process but requires efficient handling of emissions.
- Gasification: Biomass is converted into a gas mixture known as syngas (mainly hydrogen and carbon monoxide) by heating it with a controlled amount of oxygen and/or steam. This syngas can be used to generate electricity or as a precursor for producing chemicals and fuels.
- Pyrolysis: In this process, biomass is heated in the absence of oxygen to produce bio-oil, syngas, and biochar. Bio-oil can be refined into fuels, while biochar is used as a soil amendment.
-
Biochemical Conversion Methods:
- Anaerobic Digestion: This process involves breaking down organic material in the absence of oxygen to produce biogas, which is primarily composed of methane and carbon dioxide. The biogas can be used for heating, electricity generation, or as a renewable natural gas.
- Fermentation: Biomass, particularly sugars and starches, is converted into ethanol through the action of microorganisms. Ethanol is widely used as a biofuel, especially in the transportation sector.
-
Applications and Benefits:
- Energy Production: Both thermochemical and biochemical methods contribute to the production of renewable energy, reducing reliance on fossil fuels.
- Waste Management: These technologies provide a way to convert agricultural, industrial, and municipal waste into valuable energy products, thereby aiding in waste reduction and management.
- Environmental Impact: By converting biomass into energy, these technologies help in reducing greenhouse gas emissions and promoting a circular economy.
-
Challenges and Considerations:
- Efficiency and Scalability: While these technologies are promising, challenges remain in terms of efficiency, scalability, and economic viability.
- Feedstock Availability: The sustainability of biomass conversion technologies depends on the consistent availability of feedstock, which can be influenced by agricultural practices and land use.
- Technological Advancements: Ongoing research and development are crucial for improving the efficiency and reducing the costs of these conversion technologies.
In summary, biomass conversion technologies offer a versatile and sustainable approach to energy production, leveraging both thermochemical and biochemical processes to transform organic materials into valuable energy products. These technologies not only contribute to energy security but also play a significant role in environmental conservation and waste management.
Summary Table:
Category | Methods | Process | Applications |
---|---|---|---|
Thermochemical Methods | Combustion | Direct burning of biomass to produce heat for electricity or heating. | Energy production, heating. |
Gasification | Converts biomass into syngas (hydrogen + carbon monoxide) using heat. | Electricity generation, chemical production. | |
Pyrolysis | Heats biomass without oxygen to produce bio-oil, syngas, and biochar. | Biofuel production, soil amendment. | |
Biochemical Methods | Anaerobic Digestion | Breaks down organic material without oxygen to produce biogas. | Heating, electricity generation, renewable natural gas. |
Fermentation | Converts sugars and starches into ethanol using microorganisms. | Biofuel production, especially for transportation. | |
Benefits | Energy Production | Reduces reliance on fossil fuels. | Renewable energy generation. |
Waste Management | Converts waste into valuable energy products. | Agricultural, industrial, and municipal waste reduction. | |
Environmental Impact | Reduces greenhouse gas emissions and promotes a circular economy. | Sustainable energy solutions. | |
Challenges | Efficiency and Scalability | Requires advancements for better efficiency and scalability. | Ongoing research and development. |
Feedstock Availability | Depends on consistent feedstock supply. | Influenced by agricultural practices and land use. |
Ready to explore biomass conversion technologies for your energy needs? Contact us today to learn more!