Catalysts play a crucial role in pyrolysis by promoting specific chemical reactions that enhance the yield and quality of desired products such as biofuels, chemicals, and hydrocarbons. The type of catalyst used depends on the feedstock, desired end products, and process conditions. Common catalysts include biochar-based catalysts, zeolites, clay minerals like kaolin, titanium compounds, and metal nitrides. These catalysts selectively crack or condense hydrocarbons, improve reaction efficiency, and tailor the output to meet specific needs. Additionally, inherent inorganic materials in biomass, such as alkali and alkali-earth metals, can exhibit catalytic activity, although catalysts are generally not used in torrefaction or slow pyrolysis.
Key Points Explained:
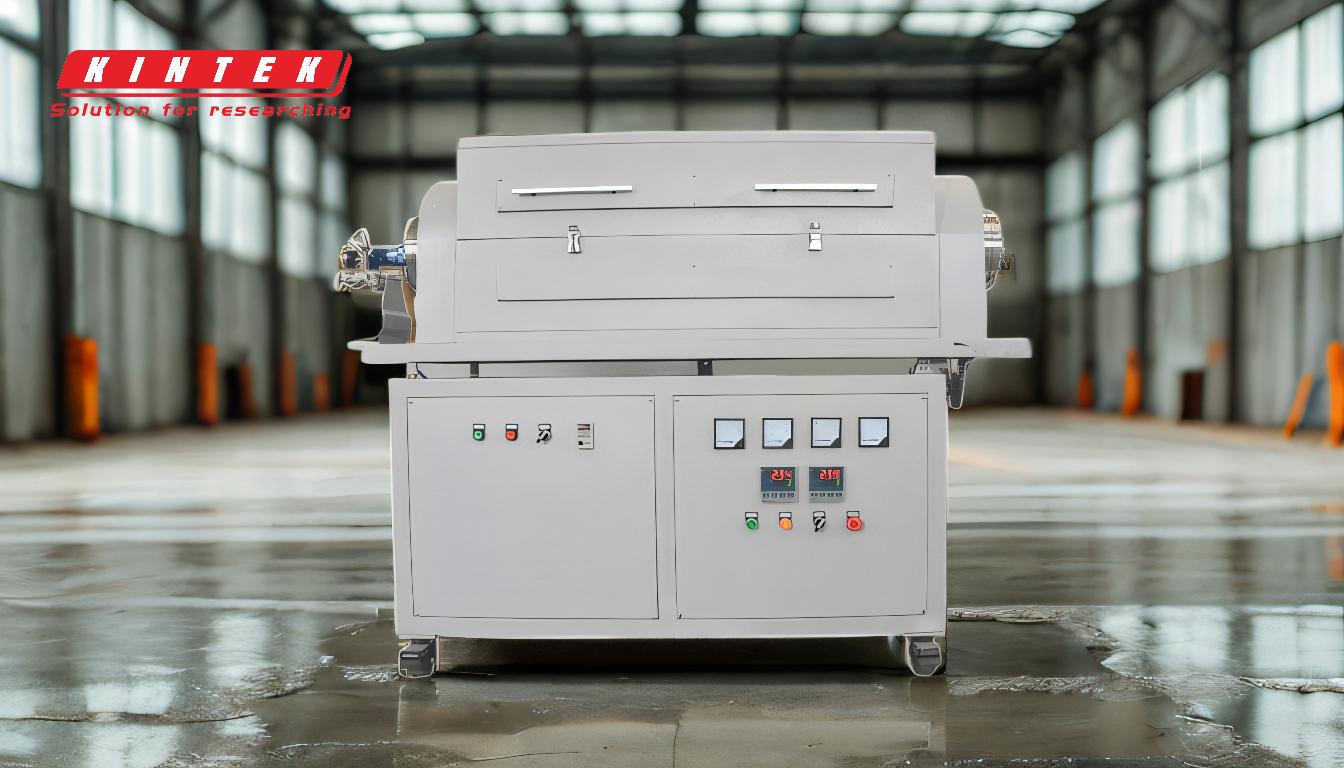
-
Biochar-Based Catalysts:
- Biochar-based catalysts are widely used in pyrolysis to promote desirable chemical reactions. They improve the yield of valuable biofuels and chemicals by enhancing the breakdown of complex organic compounds into simpler, more useful molecules.
- These catalysts are particularly effective in biomass pyrolysis, where they help convert lignocellulosic materials into bio-oil, syngas, and char.
-
Zeolites:
- Zeolites are porous materials composed of aluminum and silicon oxides. They are highly effective in pyrolysis due to their ability to selectively crack heavy hydrocarbons and condense light hydrocarbons.
- Zeolites are commonly used to produce C1, C2, and C3 hydrocarbons from biomass. Their selectivity and efficiency make them ideal for tailoring the output of pyrolysis processes to specific end products.
-
Clay Minerals (e.g., Kaolin):
- Clay minerals like kaolin are another class of catalysts used in pyrolysis. They are particularly useful for cracking heavy hydrocarbons and promoting the formation of lighter, more valuable compounds.
- These catalysts are often chosen for their cost-effectiveness and availability, making them suitable for large-scale pyrolysis applications.
-
Titanium Compounds and Metal Nitrides:
- Heterogeneous catalysts such as titanium compounds (e.g., TiN) and metal nitrides (e.g., GaN) are used in biomass fast pyrolysis for the production of furfural compounds.
- These catalysts are specifically designed to promote the formation of furfural, a valuable chemical used in various industrial applications.
-
Inherent Inorganic Materials in Biomass:
- In some pyrolysis processes, particularly torrefaction and slow pyrolysis, catalysts are not explicitly added. However, the inorganic materials inherently present in biomass, such as alkali and alkali-earth metals, can exhibit catalytic activity.
- These natural catalysts help facilitate the breakdown of biomass into useful products without the need for additional chemical additives.
-
Catalyst Selection Criteria:
- The choice of catalyst in pyrolysis depends on several factors, including the type of feedstock, desired end products, and process conditions.
- Catalysts must be selected based on their ability to promote specific reactions, improve yield, and enhance the quality of the final products.
-
Role of Catalysts in Plastic Pyrolysis:
- Catalysts are also used in the pyrolysis of plastics to convert them into oil. These catalysts promote the breakdown of long-chain polymers into shorter-chain hydrocarbons, which can then be refined into fuels or other valuable chemicals.
- The use of catalysts in plastic pyrolysis helps improve the efficiency and sustainability of the process by maximizing the yield of usable products.
By understanding the different types of catalysts and their specific roles in pyrolysis, stakeholders can optimize the process to achieve desired outcomes, whether for biofuel production, chemical synthesis, or waste recycling.
Summary Table:
Catalyst Type | Key Benefits | Applications |
---|---|---|
Biochar-Based Catalysts | Enhance breakdown of organic compounds, improve biofuel and chemical yield | Biomass pyrolysis, lignocellulosic material conversion |
Zeolites | Selective cracking of heavy hydrocarbons, produce C1, C2, and C3 hydrocarbons | Tailoring pyrolysis output for specific end products |
Clay Minerals (e.g., Kaolin) | Cost-effective cracking of heavy hydrocarbons, promotes lighter compounds | Large-scale pyrolysis applications |
Titanium Compounds/Metal Nitrides | Promote furfural production in fast pyrolysis | Industrial chemical synthesis |
Inherent Inorganic Materials | Natural catalytic activity, no additional additives required | Torrefaction, slow pyrolysis |
Plastic Pyrolysis Catalysts | Convert plastics into oil, maximize yield of usable products | Waste recycling, fuel production |
Optimize your pyrolysis process with the right catalysts—contact our experts today for tailored solutions!