Pyrolysis is a thermochemical decomposition process that breaks down organic materials at elevated temperatures in the absence of oxygen. The process is categorized into different types based on heating rates, residence times, and temperature ranges, each yielding distinct products such as biochar, bio-oil, and syngas. The primary types of pyrolysis units are slow pyrolysis, fast pyrolysis, and flash pyrolysis, with additional classifications like intermittent and continuous pyrolysis plants. Each type has unique characteristics, applications, and operational parameters, making them suitable for specific industrial or environmental needs.
Key Points Explained:
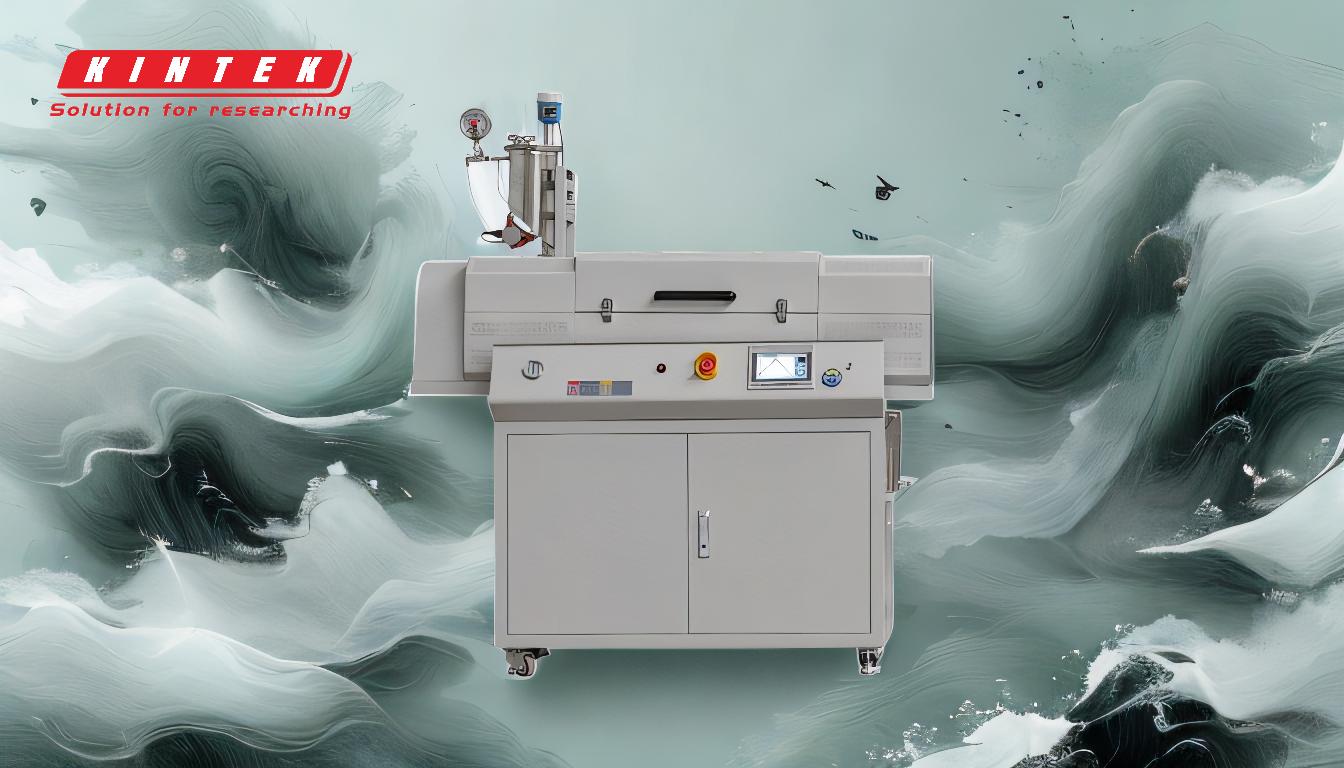
-
Types of Pyrolysis Based on Process Characteristics
-
Slow Pyrolysis:
- Process: Operates at low heating rates (0.1–1°C/s) and long residence times (minutes to hours).
- Temperature: Typically between 300–700°C.
- Products: Primarily biochar, with smaller amounts of bio-oil and syngas.
- Applications: Used in carbonization processes, soil amendment, and charcoal production.
- Advantages: High biochar yield, simple operation, and low energy requirements.
-
Fast Pyrolysis:
- Process: High heating rates (10–200°C/s) and short residence times (less than 2 seconds).
- Temperature: Operates between 400–600°C.
- Products: Maximizes bio-oil (up to 60%), with biochar (20%) and syngas (20%) as byproducts.
- Applications: Biofuel production, renewable energy, and chemical feedstock.
- Advantages: High bio-oil yield, efficient energy recovery, and scalability.
-
Flash Pyrolysis:
- Process: Extremely rapid heating rates (up to 1000°C/s) and very short residence times (milliseconds).
- Temperature: Operates at temperatures above 700°C.
- Products: Primarily syngas and bio-oil with minimal biochar.
- Applications: Advanced biofuel production and high-value chemical synthesis.
- Advantages: High gas yield, rapid processing, and suitability for high-throughput systems.
-
-
Types of Pyrolysis Plants
-
Intermittent Pyrolysis Plants:
- Operate in batches, processing a fixed amount of feedstock at a time.
- Suitable for small-scale operations or niche applications.
- Examples include small-scale biochar production units.
-
Continuous Pyrolysis Plants:
- Operate continuously, feeding and processing feedstock without interruption.
- Ideal for large-scale industrial applications, such as waste-to-energy plants.
- Examples include municipal solid waste (MSW) processing facilities.
-
-
Specialized Pyrolysis Processes
- Carbonization: A form of slow pyrolysis focused on producing high-quality charcoal.
- Methane Pyrolysis: Decomposes methane into hydrogen and solid carbon, offering a clean energy solution.
- Hydrous Pyrolysis: Involves water in the process, often used in oil shale processing.
- Dry Distillation: A pyrolysis process used in the production of tar, wood vinegar, and other chemicals.
- Thermal Depolymerization: Breaks down complex organic materials into simpler compounds, often used in waste recycling.
- Flash Vacuum Pyrolysis: A high-speed process used in chemical synthesis and specialty material production.
-
Key Factors Influencing Pyrolysis Type Selection
- Feedstock Type: Determines the optimal pyrolysis process (e.g., wood, plastics, or agricultural waste).
- Desired Products: Biochar, bio-oil, or syngas production goals influence the choice of pyrolysis type.
- Scale of Operation: Small-scale operations may prefer intermittent plants, while large-scale industries opt for continuous systems.
- Energy Efficiency: Fast and flash pyrolysis are more energy-efficient but require advanced technology.
- Environmental Impact: Slow pyrolysis is often favored for carbon sequestration, while fast pyrolysis is ideal for renewable energy.
-
Applications of Pyrolysis Products
- Biochar: Used as a soil amendment, carbon sequestration agent, and in water filtration.
- Bio-oil: A renewable fuel source and feedstock for chemicals.
- Syngas: Used for electricity generation, heating, and as a chemical feedstock.
-
Advantages and Challenges of Pyrolysis
-
Advantages:
- Converts waste materials into valuable products.
- Reduces landfill dependency and greenhouse gas emissions.
- Provides renewable energy and chemical alternatives.
-
Challenges:
- High initial capital investment for advanced systems.
- Requires precise control of temperature and residence time.
- Feedstock variability can affect product quality.
-
Advantages:
By understanding the different types of pyrolysis units and their applications, purchasers can make informed decisions based on their specific needs, whether for energy production, waste management, or chemical synthesis. Each type offers unique benefits and challenges, making it essential to evaluate operational requirements and desired outcomes before selecting a pyrolysis system.
Summary Table:
Type | Heating Rate | Residence Time | Temperature | Primary Products | Applications |
---|---|---|---|---|---|
Slow Pyrolysis | 0.1–1°C/s | Minutes to hours | 300–700°C | Biochar | Soil amendment, charcoal production |
Fast Pyrolysis | 10–200°C/s | < 2 seconds | 400–600°C | Bio-oil (60%) | Biofuel, renewable energy |
Flash Pyrolysis | Up to 1000°C/s | Milliseconds | > 700°C | Syngas, bio-oil | Advanced biofuels, chemical synthesis |
Ready to choose the right pyrolysis unit for your needs? Contact our experts today for personalized guidance!