Pyrolytic ovens, while highly efficient for self-cleaning, come with several disadvantages that potential buyers should consider. These include high energy consumption, potential damage to oven components, safety concerns, and limited usability during the cleaning cycle. Additionally, the high temperatures required for pyrolysis can release fumes that may be harmful if not properly ventilated. Understanding these drawbacks is crucial for making an informed decision about whether a pyrotic oven is the right choice for your kitchen.
Key Points Explained:
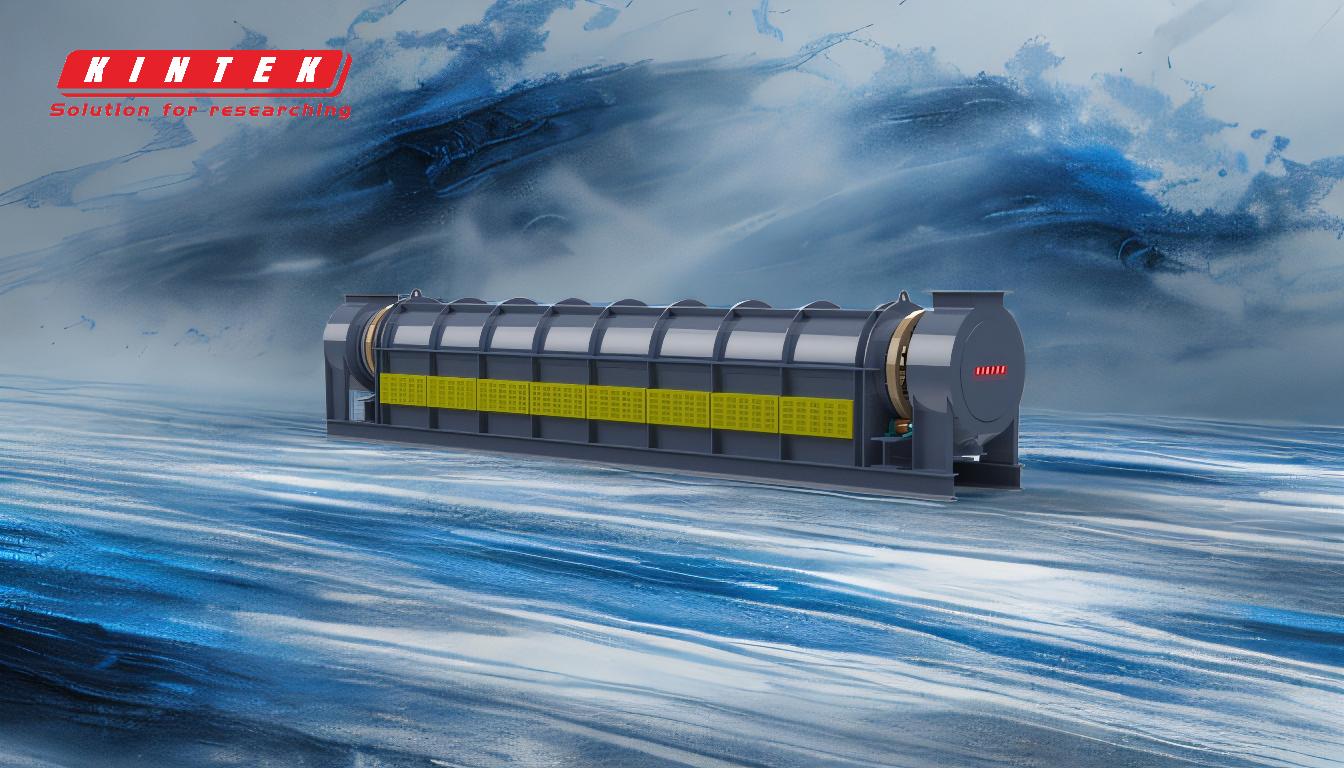
-
High Energy Consumption:
- Pyrolytic ovens require extremely high temperatures (around 500°C or 932°F) to burn off food residues and grease. This process consumes a significant amount of energy, making it less environmentally friendly and more costly in terms of electricity bills.
- The energy-intensive nature of pyrolytic cleaning may not be ideal for households looking to reduce their carbon footprint or energy expenses.
-
Potential Damage to Oven Components:
- The extreme heat used in pyrolytic cleaning can cause wear and tear on the oven's internal components, such as seals, hinges, and heating elements. Over time, this may lead to reduced efficiency or the need for costly repairs.
- Certain materials, like plastic or rubber parts, may degrade faster under these high temperatures, shortening the overall lifespan of the oven.
-
Safety Concerns:
- During the pyrolytic cleaning cycle, the oven's exterior can become extremely hot, posing a burn risk, especially in households with children or pets.
- The process can also release fumes and smoke, which may contain harmful particles. Proper ventilation is essential to avoid inhaling these fumes, and some users may find the odor unpleasant.
-
Limited Usability During Cleaning:
- Pyrolytic cleaning cycles can take several hours, during which the oven cannot be used for cooking. This can be inconvenient for those who rely on their oven frequently or have limited cooking space.
- The cooling-down period after the cleaning cycle further extends the time the oven is out of commission.
-
Cost and Maintenance:
- Pyrolytic ovens are generally more expensive than traditional ovens due to their advanced self-cleaning technology. The initial investment may not be justified for users who do not require frequent deep cleaning.
- Maintenance, such as replacing worn-out parts or addressing issues caused by high temperatures, can add to the long-term costs.
-
Environmental Impact:
- The high energy consumption of pyrolytic ovens contributes to a larger carbon footprint compared to manual cleaning methods or ovens with alternative cleaning technologies.
- The release of fumes and particles during the cleaning process may also have environmental implications, particularly if not properly ventilated.
In summary, while pyrolytic ovens offer the convenience of self-cleaning, their disadvantages—such as high energy use, potential damage, safety risks, and limited usability—should be carefully weighed against their benefits. For those prioritizing energy efficiency, cost-effectiveness, or frequent oven use, alternative cleaning methods or oven types may be more suitable.
Summary Table:
Disadvantage | Key Details |
---|---|
High Energy Consumption | Requires 500°C (932°F), increases electricity bills, less eco-friendly. |
Potential Damage to Components | Extreme heat can wear out seals, hinges, and heating elements, leading to repairs. |
Safety Concerns | Exterior gets extremely hot; fumes may be harmful if not ventilated properly. |
Limited Usability | Cleaning cycle takes hours, oven unavailable for cooking during and after. |
High Cost and Maintenance | More expensive upfront; maintenance costs due to wear and tear. |
Environmental Impact | High energy use increases carbon footprint; fumes may harm the environment. |
Still unsure if a pyrolytic oven is right for you? Contact us today for expert advice!