DC sputtering, while a widely used technique in thin film deposition, has several disadvantages that can limit its effectiveness in certain applications. These include its inability to sputter non-conductive materials, lower deposition rates compared to more advanced techniques, and challenges related to target erosion and process control. Understanding these limitations is crucial for selecting the appropriate sputtering method for specific industrial needs.
Key Points Explained:
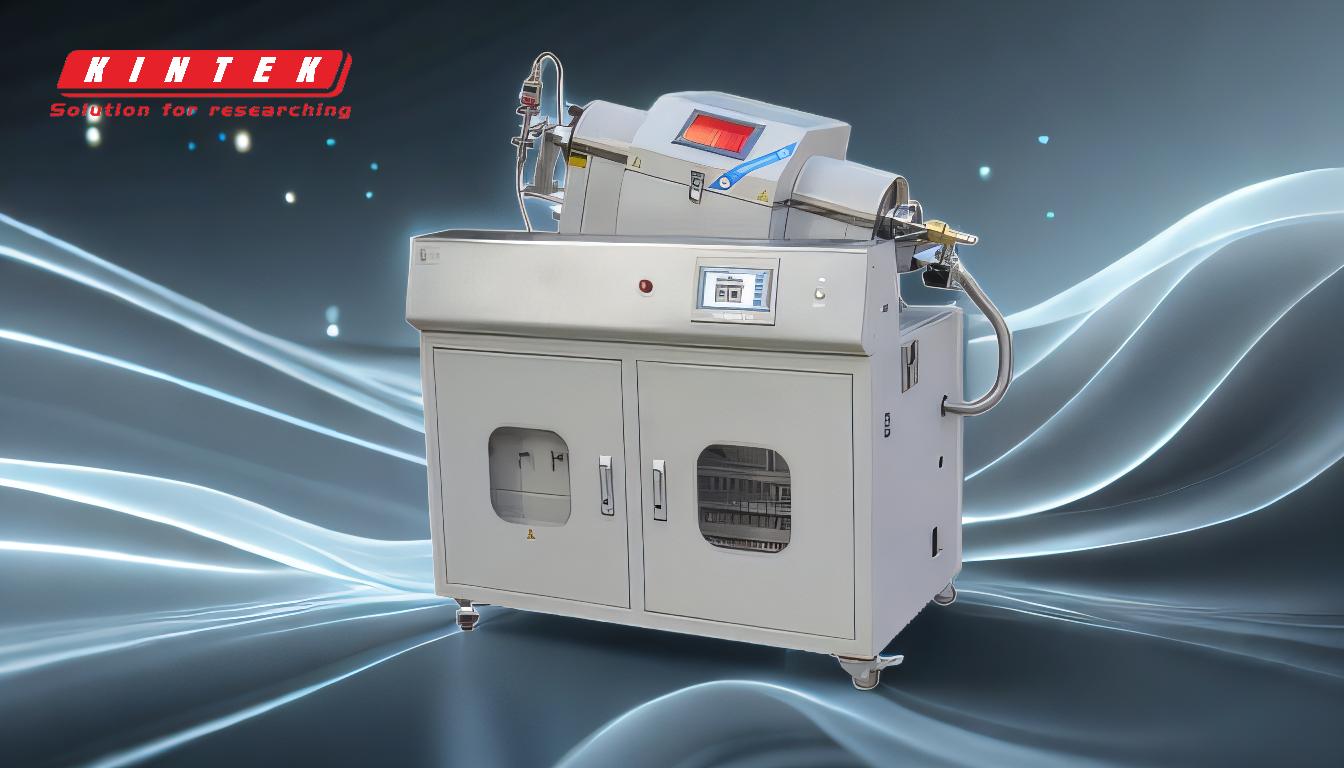
-
Inability to Sputter Non-Conductive Materials:
- DC sputtering is limited to conductive materials. Non-conductive materials, such as insulators, cannot be effectively sputtered using DC methods because they accumulate charge, which disrupts the sputtering process. This limitation is significant in industries where insulating materials are commonly used, such as in certain semiconductor applications. For such materials, RF magnetron sputtering is often employed as it uses alternating current to prevent charge buildup.
-
Lower Deposition Rates:
- Compared to more advanced sputtering techniques like High Power Impulse Magnetron Sputtering (HIPIMS), DC sputtering generally offers lower deposition rates. This is due to lower plasma densities and higher gas densities in the DC sputtering process. Lower deposition rates can lead to longer processing times, which may not be ideal for high-throughput manufacturing environments.
-
Target Erosion and Non-Uniformity:
- One of the notable disadvantages of DC magnetron sputtering is the non-uniform erosion of the target material. This uneven wear can lead to a reduction in the target's lifespan and can also affect the quality and uniformity of the deposited film. Regular maintenance and target replacement are necessary to mitigate these effects, adding to the operational costs.
-
Sensitivity to Process Parameters:
- Achieving optimal results with DC sputtering requires precise control over various process parameters, including gas pressure, target-substrate distance, and voltage. Any deviation from the optimal settings can significantly impact the quality of the deposited film. This sensitivity necessitates sophisticated control systems and skilled operators, increasing the complexity and cost of the process.
-
Challenges with Multi-Layer Deposition:
- As the number of layers increases, production yields in DC sputtering can decline. This is due to the cumulative effect of defects and inconsistencies in each layer, which can compromise the overall quality of the multi-layer structure. This limitation is particularly problematic in applications requiring high precision and reliability, such as in the production of optical devices and semiconductors.
-
Material Limitations:
- DC sputtering is not suitable for all types of materials. For example, materials that are sensitive to moisture or have weak adhesion properties may not perform well with DC sputtering. These materials may require additional treatments or alternative deposition methods to achieve the desired film properties.
In summary, while DC sputtering offers several advantages, such as simplicity and cost-effectiveness, it also comes with notable disadvantages that can affect its suitability for certain applications. Understanding these limitations is essential for making informed decisions in the selection of sputtering techniques for specific industrial needs.
Summary Table:
Disadvantage | Description |
---|---|
Inability to Sputter Non-Conductive Materials | DC sputtering is limited to conductive materials; insulators cannot be effectively sputtered. |
Lower Deposition Rates | DC sputtering offers slower deposition rates compared to advanced techniques like HIPIMS. |
Target Erosion and Non-Uniformity | Non-uniform target erosion reduces lifespan and affects film quality. |
Sensitivity to Process Parameters | Requires precise control of gas pressure, distance, and voltage for optimal results. |
Challenges with Multi-Layer Deposition | Yields decline with increased layers due to defects and inconsistencies. |
Material Limitations | Unsuitable for moisture-sensitive or weakly adhesive materials. |
Need help choosing the right sputtering method for your application? Contact our experts today!