Diamond-like carbon (DLC) coatings are widely recognized for their excellent properties, such as high hardness, low friction, and wear resistance. However, they also come with several disadvantages that can limit their applicability in certain scenarios. These include challenges related to deposition processes, material compatibility, and performance under specific conditions. Understanding these limitations is crucial for making informed decisions when considering DLC coatings for various applications.
Key Points Explained:
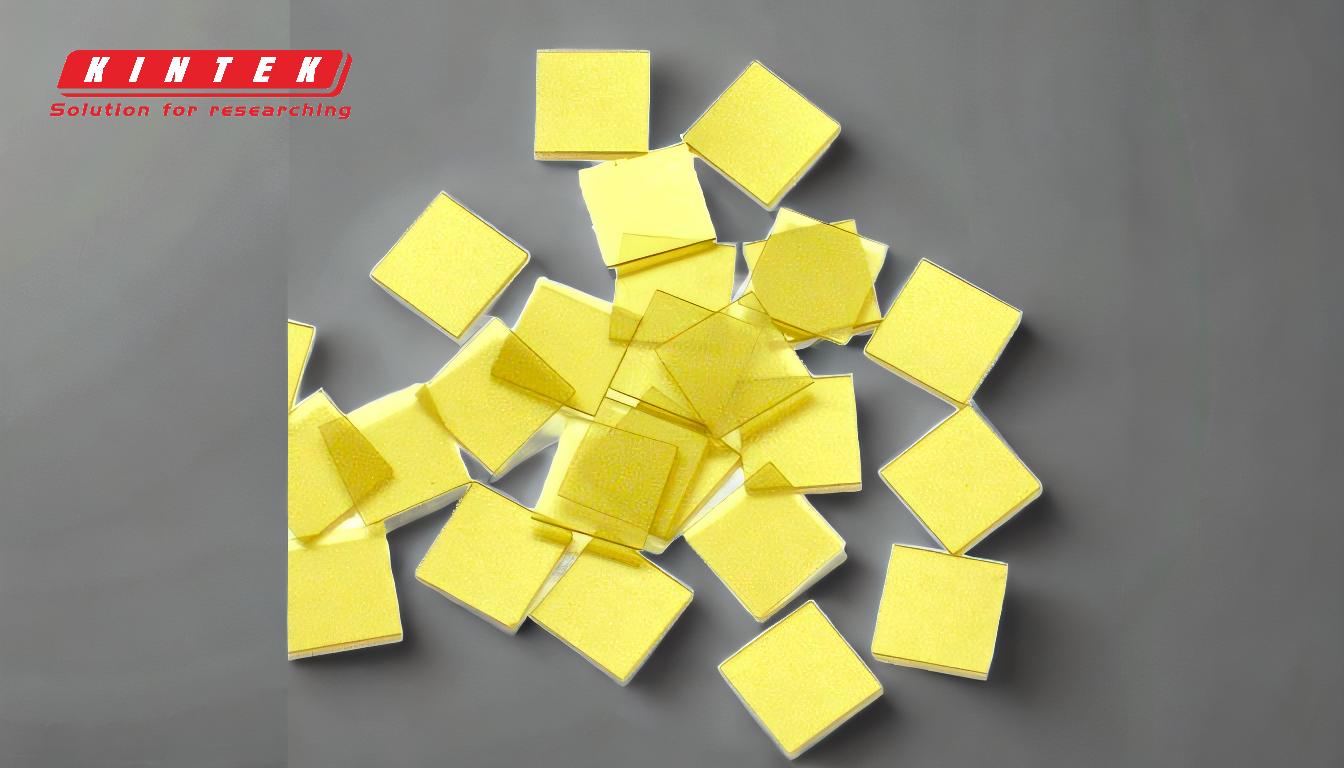
-
Deposition Process Limitations:
- High Processing Temperatures: DLC coatings, particularly those applied via Chemical Vapor Deposition (CVD), often require high processing temperatures (800–1000 °C). This limits their use to materials that can withstand such heat, such as cemented carbide. Many materials, especially polymers and some metals, cannot endure these temperatures, restricting the range of applications.
- Masking Difficulties: CVD coatings are difficult to mask, often resulting in an all-or-nothing coating. This means that selective coating of specific areas is challenging, which can be a significant drawback when only certain parts of a component require coating.
- Size Constraints: The size of the parts that can be coated is limited by the capacity of the reaction chamber. Large or complex components may need to be broken down into smaller parts, complicating the process and increasing costs.
-
Coating Thickness and Stress Issues:
- Thick Coatings and Tensile Stress: DLC coatings, especially those applied via CVD, can be relatively thick (10–20 μm). During cooling, these thick coatings can generate tensile stress, leading to fine cracks. These cracks may propagate under external impact, causing the coating to peel off. This makes DLC coatings less suitable for applications involving interrupted cutting processes, such as milling, where the coating is more prone to failure.
- Adhesion Challenges: The adhesion of DLC coatings to certain substrates can be problematic, particularly if the substrate material is not compatible with the high temperatures or if the surface preparation is inadequate. Poor adhesion can lead to delamination and reduced coating performance.
-
Performance Limitations in Specific Conditions:
- Interrupted Cutting Processes: DLC coatings are not ideal for interrupted cutting processes like milling. The repeated impact and thermal cycling in such processes can exacerbate the formation of cracks and lead to coating failure. This limits their use in certain machining applications where other coatings might perform better.
- Hydrogen Content and Stability: Some DLC coatings contain hydrogen, which can affect their stability and performance, especially at elevated temperatures. Hydrogenated DLC coatings may degrade or lose their properties when exposed to high temperatures, limiting their use in high-temperature applications.
-
Cost and Complexity:
- High Cost of Deposition: The equipment and processes required for depositing DLC coatings, particularly via CVD, are complex and expensive. This can make DLC coatings cost-prohibitive for some applications, especially when compared to alternative coatings.
- Process Complexity: The need for high temperatures, specialized equipment, and precise control of deposition parameters adds to the complexity of the process. This can increase production time and costs, making DLC coatings less attractive for high-volume or low-cost applications.
-
Material Compatibility and Application Range:
- Limited Substrate Compatibility: DLC coatings are not universally compatible with all materials. For example, they may not adhere well to certain metals or polymers, limiting their use in applications where these materials are prevalent.
- Restricted Application Range: Due to the limitations mentioned above, DLC coatings are often restricted to specific applications where their unique properties, such as low friction and high wear resistance, are essential. In other cases, alternative coatings might be more suitable.
In summary, while DLC coatings offer significant advantages in terms of hardness, friction reduction, and wear resistance, they also come with notable disadvantages. These include challenges related to the deposition process, coating thickness and stress, performance under specific conditions, cost, and material compatibility. Understanding these limitations is crucial for selecting the appropriate coating for a given application and ensuring optimal performance and durability.
Summary Table:
Disadvantage | Description |
---|---|
High Processing Temperatures | Requires 800–1000 °C, limiting use to heat-resistant materials. |
Masking Difficulties | Selective coating is challenging; often results in all-or-nothing application. |
Size Constraints | Limited by reaction chamber size, complicating large or complex components. |
Thick Coatings & Tensile Stress | Thick coatings (10–20 μm) can crack under stress, leading to peeling. |
Adhesion Challenges | Poor adhesion to certain substrates can cause delamination. |
Interrupted Cutting Processes | Not ideal for milling due to crack formation under repeated impact. |
Hydrogen Content & Stability | Hydrogenated coatings may degrade at high temperatures. |
High Cost of Deposition | Complex and expensive equipment increases overall costs. |
Limited Substrate Compatibility | Not universally compatible with all materials, restricting application range. |
Need help choosing the right coating for your application? Contact our experts today!