E-beam evaporation, while advantageous for producing high-density thin films and controlling specific wavelength reflections, has several disadvantages. These include challenges in material handling, such as particle fracturing or explosions, and the risk of material decomposition during the process. Additionally, the quality of the thin film can be affected by factors like vacuum pressure, molecular weight of the source material, and substrate surface roughness. The process also requires precise control over deposition rates and substrate rotation speeds to achieve uniform film thickness, which can be technically demanding and costly.
Key Points Explained:
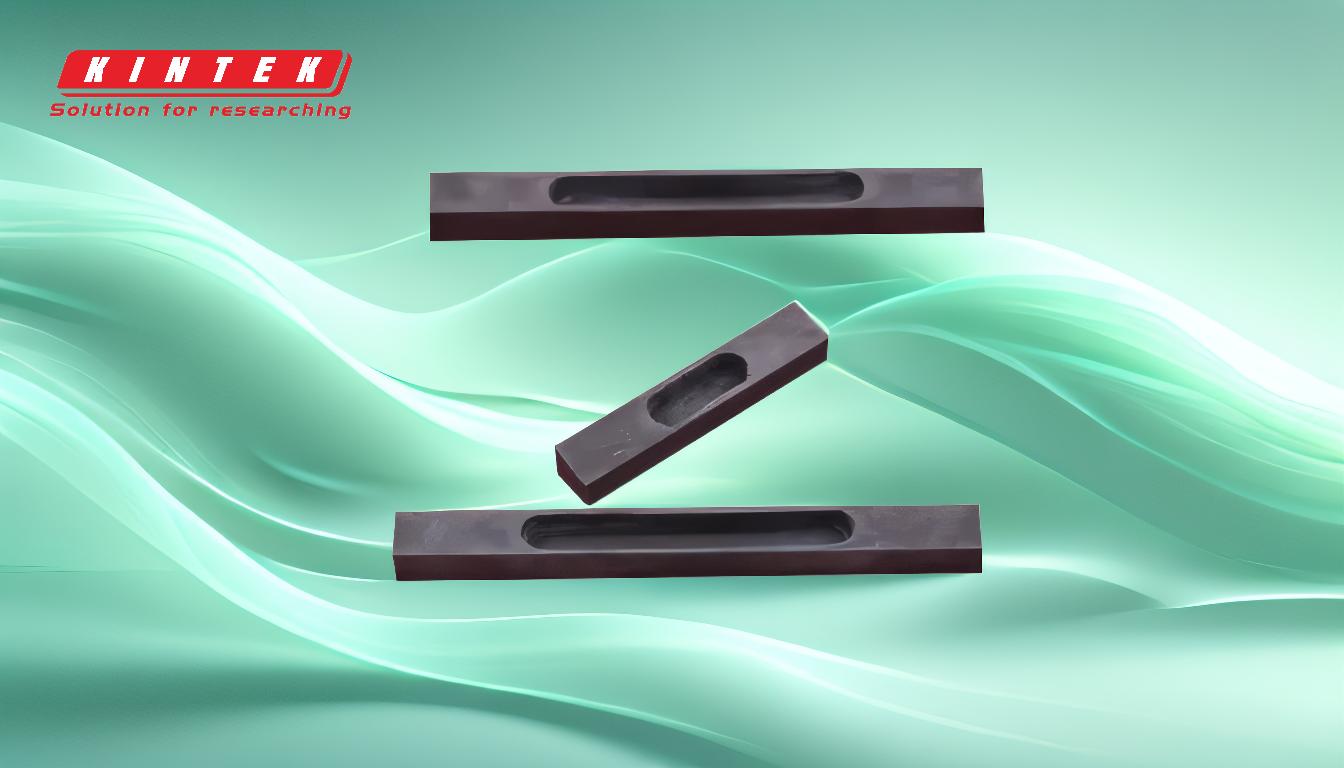
-
Material Handling Risks:
- Particle Fracturing and Explosions: The process of e-beam evaporation involves intense heat, which can lead to particle fracturing or even explosions, especially if the material in the crucible is not evenly heated or if there is an imbalance in the material quantity.
- Material Decomposition: High-energy electron beams can cause the decomposition of certain materials, leading to impurities in the deposited film and potentially altering the desired properties of the thin film.
-
Quality Control Challenges:
- Vacuum Pressure: The quality of the thin film is highly dependent on the vacuum pressure within the chamber. A higher degree of vacuum is necessary to ensure a longer free path for the source material molecules, reducing impurities. However, achieving and maintaining such high vacuum levels can be technically challenging and expensive.
- Molecular Weight and Evaporation Rate: The molecular weight of the source material and its evaporation rate must be carefully controlled. Materials with higher molecular weights may require more energy to evaporate, which can complicate the process and affect the uniformity of the film.
- Substrate Surface Roughness: A rough substrate surface can lead to non-uniform deposition, resulting in films with inconsistent thickness and potentially compromised performance.
-
Technical and Operational Demands:
- Precision in Deposition Rates: E-beam evaporation requires precise control over the deposition rates to ensure uniform film thickness. This often involves the use of quartz crystal microbalances and sophisticated control systems, which add to the complexity and cost of the process.
- Substrate Rotation Speed: The rotation speed of the substrate holder must be optimized to ensure even deposition across the substrate. This requires careful calibration and monitoring, adding another layer of technical difficulty.
-
Cost Implications:
- Equipment and Maintenance: The equipment for e-beam evaporation, including high-vacuum chambers and electron beam guns, is expensive to purchase and maintain. Regular maintenance is required to ensure the system operates efficiently and safely.
- Operational Costs: The process consumes a significant amount of energy, particularly in maintaining the high vacuum and generating the electron beam. This results in higher operational costs compared to other deposition methods.
In summary, while e-beam evaporation offers significant advantages in terms of film quality and control, it also presents several challenges that can impact the efficiency, cost, and feasibility of the process. These include risks associated with material handling, stringent quality control requirements, and high technical and operational demands.
Summary Table:
Category | Key Challenges |
---|---|
Material Handling Risks | - Particle fracturing and explosions - Material decomposition |
Quality Control | - Vacuum pressure requirements - Molecular weight and evaporation rate - Substrate surface roughness |
Technical Demands | - Precision in deposition rates - Substrate rotation speed optimization |
Cost Implications | - Expensive equipment and maintenance - High operational energy costs |
Need help navigating the challenges of e-beam evaporation? Contact our experts today for tailored solutions!