Electron beam (e-beam) deposition, while advantageous in certain applications, has several notable disadvantages that limit its suitability for specific industries and use cases. These drawbacks include high costs due to complex equipment and energy-intensive processes, limited scalability, and challenges in coating substrates with complex geometries. Additionally, e-beam deposition struggles with precision for high-precision optical coatings and faces issues like filament degradation, which can lead to non-uniform evaporation rates. These limitations make it less ideal compared to alternative methods like sputter deposition or chemical vapor deposition in industries requiring high accuracy and scalability.
Key Points Explained:
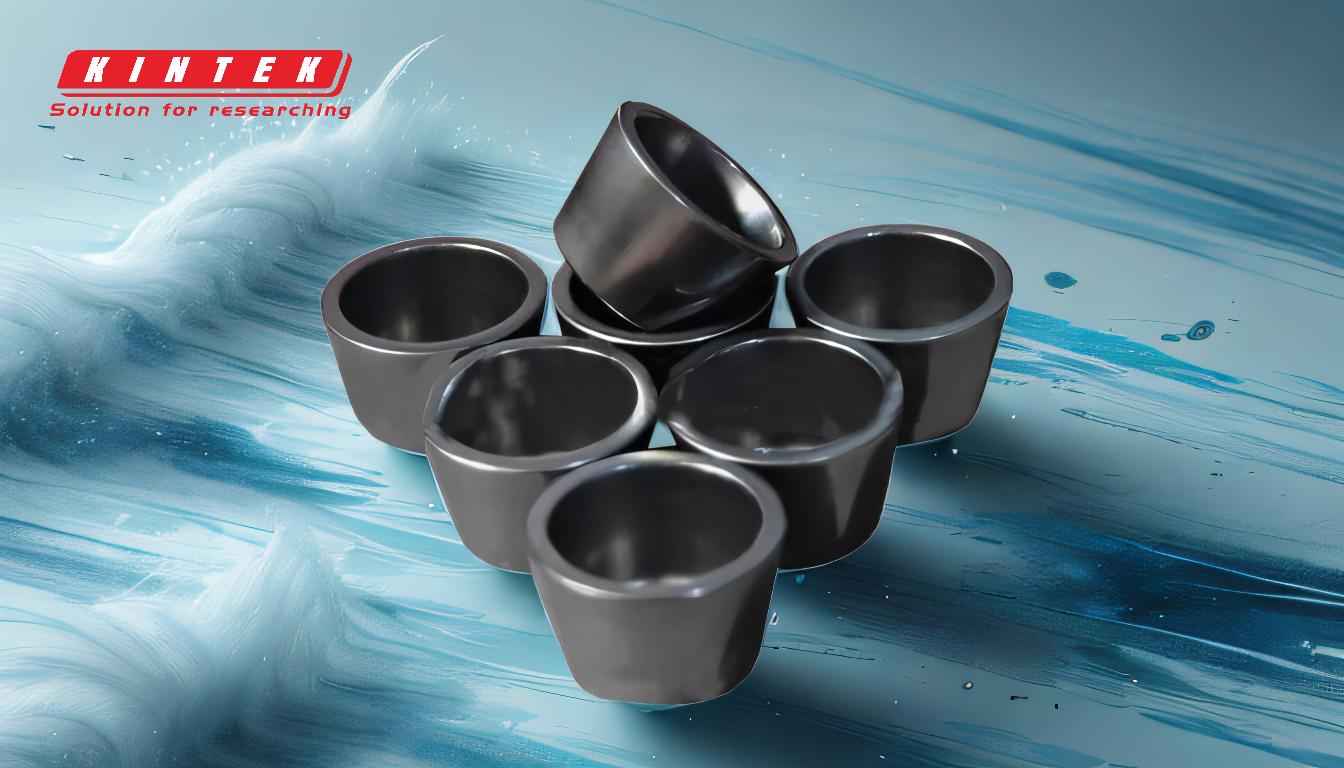
-
High Cost and Complexity:
- Equipment and Energy Costs: E-beam deposition systems are expensive due to their complex design and energy-intensive processes. The need for high-power electron beams and vacuum environments adds to operational costs.
- Maintenance and Filament Degradation: The filaments used in e-beam systems degrade over time, leading to non-uniform evaporation rates. This degradation necessitates frequent maintenance and replacement, further increasing costs.
-
Limited Scalability and Deposition Rates:
- Reduced Deposition Rates: E-beam deposition often operates at lower deposition rates compared to methods like sputter deposition or chemical vapor deposition. This limitation makes it less efficient for large-scale or high-volume production.
- Lower Utilization: The process has lower material utilization rates, meaning more raw material is wasted, which can be costly for expensive or rare materials.
-
Unsuitability for Complex Geometries:
- Line-of-Sight Limitation: E-beam deposition is primarily a line-of-sight process, meaning it cannot effectively coat the inner surfaces of complex geometries or substrates with intricate shapes. This limitation makes it unsuitable for applications requiring uniform coating on non-planar surfaces.
- Step Coverage Issues: The method struggles with step coverage, which is critical for applications like semiconductor manufacturing or optical coatings. Alternative methods like sputter deposition are preferred for such applications.
-
Precision and Accuracy Challenges:
- Insufficient for High-Precision Coatings: E-beam deposition may not provide the level of precision required for high-precision optical coatings, which are essential in industries like astronomy, biotech, medical, and aerospace. The process can produce less precise results due to factors like filament degradation and non-uniform evaporation rates.
- Radiolytic Byproduct Formation: In applications like sterilization, e-beam radiation can produce radiolytic byproducts (e.g., *OH radicals), which may damage sensitive materials or packaging systems.
-
Limited Availability and Penetration:
- Bulk Sterilization Challenges: E-beam sterilization facilities are less common and more expensive to construct compared to gamma radiation facilities. This limits their availability for bulk sterilization.
- Lower Penetration Depth: E-beam radiation has lower penetration compared to gamma radiation, making it less effective for sterilizing dense or thick materials.
-
Material Limitations:
- Evaporative Material Constraints: While e-beam deposition can use a wide range of evaporative materials, it is less effective for materials that require high precision or are sensitive to heat. This limitation restricts its use in certain high-tech applications.
In conclusion, while e-beam deposition offers advantages like simplicity and flexibility for specific applications, its high costs, limited scalability, and challenges with precision and complex geometries make it less suitable for industries requiring high accuracy, large-scale production, or uniform coating on intricate surfaces. Alternative methods like sputter deposition or chemical vapor deposition are often preferred in such cases.
Summary Table:
Disadvantage | Key Details |
---|---|
High Cost and Complexity | Expensive equipment, energy-intensive processes, and frequent maintenance. |
Limited Scalability | Lower deposition rates and material utilization, unsuitable for large-scale use. |
Unsuitability for Complex Shapes | Line-of-sight process struggles with non-planar surfaces and step coverage. |
Precision Challenges | Insufficient for high-precision coatings and radiolytic byproduct formation. |
Limited Availability | Fewer sterilization facilities and lower penetration depth compared to gamma. |
Material Constraints | Limited effectiveness for heat-sensitive or high-precision materials. |
Looking for a better deposition solution? Contact us today to explore alternatives tailored to your needs!