Inert gas systems are widely used in industries to prevent combustion by reducing the oxygen concentration in a confined space. While they offer significant safety benefits, they also come with several disadvantages. These include high initial and operational costs, complexity in maintenance, potential hazards from improper use, and limitations in certain environments. Understanding these drawbacks is crucial for equipment and consumable purchasers to make informed decisions and ensure safe and efficient operations.
Key Points Explained:
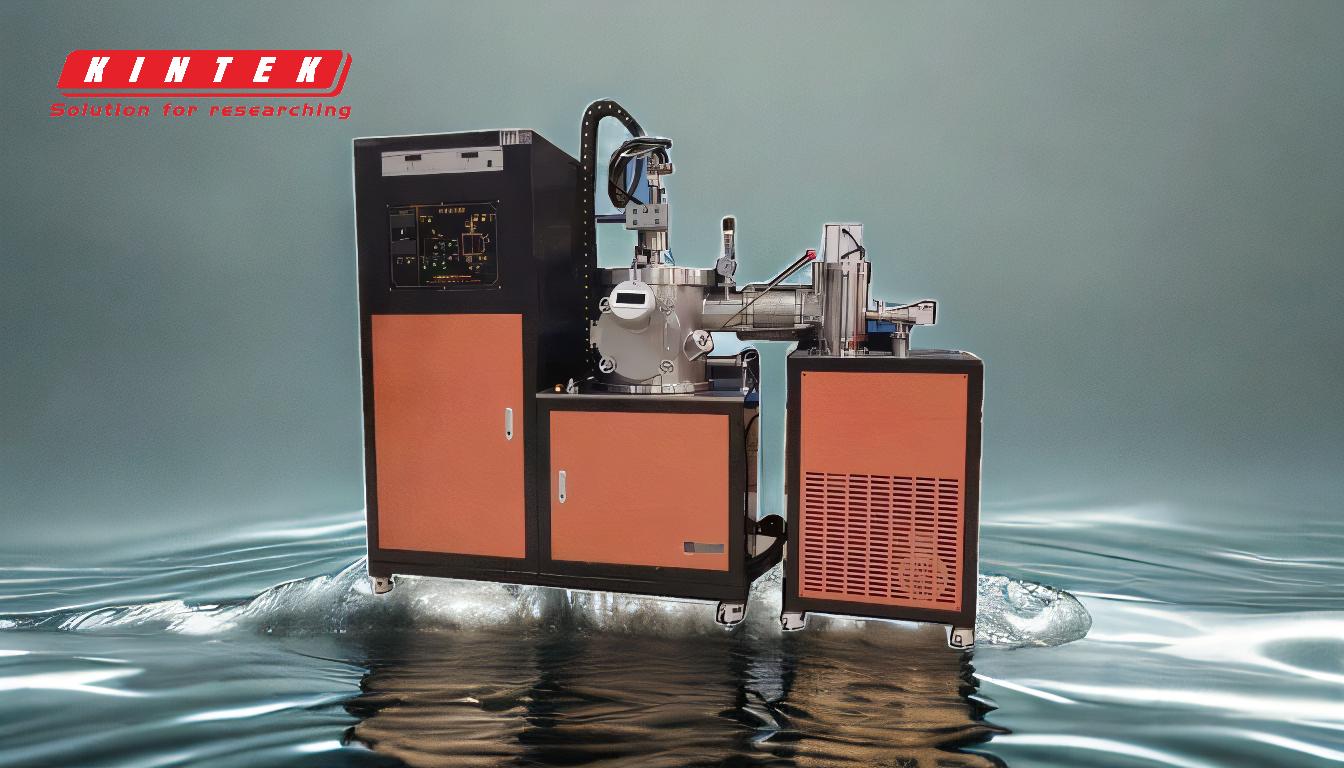
-
High Initial and Operational Costs:
- Initial Investment: Inert gas systems require substantial upfront costs for equipment, installation, and setup. This includes the purchase of gas generators, storage tanks, and distribution systems.
- Operational Expenses: The ongoing costs of maintaining and operating these systems can be significant. This includes the cost of inert gases (e.g., nitrogen, argon), energy consumption for gas generation, and regular maintenance.
- Economic Impact: For smaller operations or industries with tight budgets, these costs can be prohibitive, making it challenging to justify the investment.
-
Complexity in Maintenance:
- Regular Maintenance Requirements: Inert gas systems require frequent inspections, calibration, and servicing to ensure they function correctly. This can be time-consuming and requires skilled personnel.
- Technical Expertise: Proper maintenance often requires specialized knowledge and training, which may not be readily available in all organizations.
- Downtime: Maintenance activities can lead to operational downtime, affecting productivity and potentially leading to financial losses.
-
Potential Hazards from Improper Use:
- Asphyxiation Risk: Inert gases can displace oxygen in the air, creating a risk of asphyxiation for workers if the system is not properly managed or if leaks occur.
- Human Error: Incorrect operation or failure to follow safety protocols can lead to dangerous situations, including oxygen depletion in confined spaces.
- Gas Leaks: Leaks in the system can go unnoticed, leading to a gradual buildup of inert gas and posing a serious health risk to personnel.
-
Limitations in Certain Environments:
- Space Constraints: Inert gas systems require adequate space for installation, which may not be available in all facilities, especially in older or smaller plants.
- Compatibility Issues: Some materials or processes may not be compatible with inert gases, limiting their applicability in certain industries.
- Environmental Conditions: Extreme temperatures or humid conditions can affect the performance of inert gas systems, requiring additional measures to ensure reliability.
-
Regulatory and Compliance Challenges:
- Stringent Regulations: The use of inert gas systems is often subject to strict regulatory requirements, which can vary by region and industry. Compliance with these regulations can be complex and costly.
- Documentation and Reporting: Organizations must maintain detailed records of system performance, maintenance, and safety checks, adding to the administrative burden.
- Inspection and Audits: Regular inspections and audits by regulatory bodies can be time-consuming and may require additional resources to address any identified issues.
-
Impact on Product Quality:
- Contamination Risks: In some cases, the introduction of inert gases can lead to contamination of products, especially in industries like food processing or pharmaceuticals, where purity is critical.
- Process Interference: The presence of inert gases can interfere with certain manufacturing processes, potentially affecting product quality or yield.
- Cost of Quality Control: Additional measures may be required to monitor and control the impact of inert gases on product quality, increasing operational costs.
In conclusion, while inert gas systems offer significant safety benefits, they come with a range of disadvantages that must be carefully considered. High costs, maintenance complexity, potential hazards, environmental limitations, regulatory challenges, and impacts on product quality are all factors that equipment and consumable purchasers need to weigh when deciding whether to implement these systems. Proper planning, training, and ongoing management are essential to mitigate these disadvantages and ensure safe and effective use of inert gas systems.
Summary Table:
Disadvantage | Key Details |
---|---|
High Initial and Operational Costs | Substantial upfront costs for equipment, installation, and ongoing maintenance. |
Complexity in Maintenance | Requires frequent inspections, skilled personnel, and can cause operational downtime. |
Potential Hazards | Risk of asphyxiation, human error, and gas leaks if not properly managed. |
Limitations in Certain Environments | Space constraints, compatibility issues, and environmental challenges. |
Regulatory and Compliance Challenges | Strict regulations, documentation, and frequent inspections. |
Impact on Product Quality | Contamination risks, process interference, and additional quality control costs. |
Need help deciding if an inert gas system is right for your operation? Contact our experts today for personalized advice!