Physical Vapor Deposition (PVD) coating is a widely used technique for applying thin films to various substrates, offering benefits such as improved hardness, wear resistance, and corrosion protection. However, it also comes with several disadvantages that can impact its suitability for certain applications. These drawbacks include high costs due to specialized equipment and energy requirements, limitations as a "line of sight" process, slow processing speeds, and challenges related to color preservation and material wastage. Understanding these limitations is crucial for making informed decisions when considering PVD coating for specific projects.
Key Points Explained:
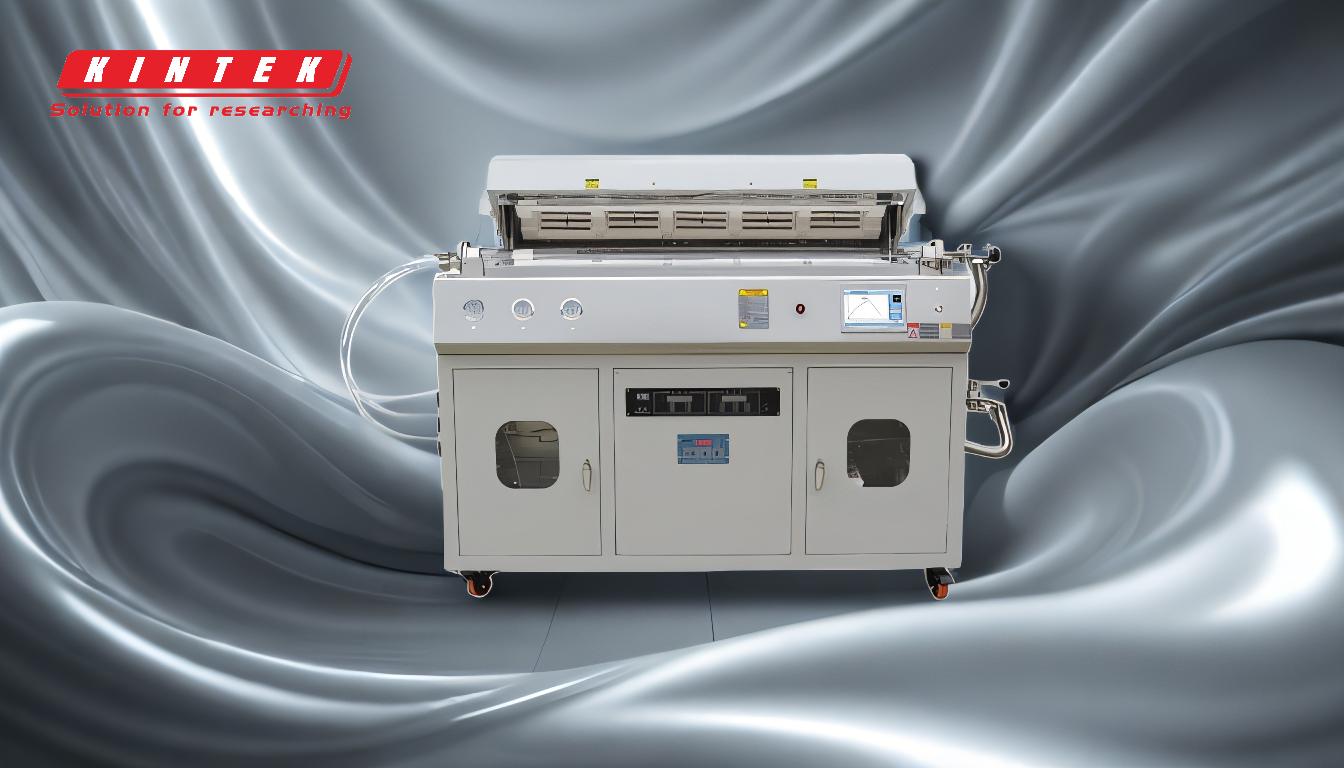
-
High Cost
- PVD coating is an expensive process due to the need for specialized equipment, such as large vacuum chambers and advanced heating and cooling systems. The energy-intensive nature of the process, which involves intense heating and cooling cycles, further drives up costs. Additionally, the expertise required to operate and maintain the equipment adds to the overall expense.
- Compared to other thin film deposition methods, such as Chemical Vapor Deposition (CVD) or electroplating, PVD can be significantly more costly, especially for high-end techniques like ion beam sputtering or magnetron sputtering.
-
Line of Sight Limitation
- PVD is a "line of sight" process, meaning it can only coat surfaces that are directly exposed to the vapor source. This makes it unsuitable for coating complex geometries or hidden surfaces, such as the interiors of deep holes or the backsides of components.
- This limitation can be a significant drawback for applications requiring uniform coating on all surfaces, as it may necessitate additional processing steps or alternative coating methods.
-
Slow Processing Speed
- PVD coating is relatively slow compared to other coating techniques. The deposition rates are typically low, which can lead to longer processing times, especially for thicker coatings or large batches of components.
- This slow speed can be a bottleneck in high-volume production environments, where faster coating methods may be preferred to meet production deadlines.
-
Color Destruction and Material Wastage
- One notable drawback of PVD coating is its tendency to aggressively alter or destroy colors, particularly in decorative applications. This can result in material wastage and additional costs for rework or refinishing.
- The process may also require careful masking or pretreatment to preserve specific colors or patterns, adding complexity and time to the overall process.
-
Dependence on Substrate Material
- The properties of PVD coatings are heavily influenced by the underlying substrate material. For example, coatings like TiN (Titanium Nitride) may improve fatigue limits and endurance in certain alloys but may not provide the same benefits for other materials.
- This dependence means that the effectiveness of PVD coatings can vary significantly based on the substrate, requiring careful material selection and testing.
-
Equipment and Expertise Requirements
- PVD coating requires specialized equipment, including large vacuum chambers and precise control systems, which can be expensive to purchase and maintain.
- The process also demands a high level of expertise to ensure proper operation and quality control, which can further increase costs and limit accessibility for smaller operations.
-
Size and Geometry Limitations
- The size of components that can be coated using PVD is limited by the dimensions of the vacuum chamber. Large or complex parts may need to be disassembled or coated in multiple stages, adding time and complexity to the process.
- This limitation can make PVD less suitable for large-scale or on-site applications, where alternative methods like CVD or thermal spray coating may be more practical.
In summary, while PVD coating offers numerous advantages, its disadvantages—such as high costs, line of sight limitations, slow processing speeds, and challenges with color preservation—must be carefully considered. These factors can impact the feasibility and cost-effectiveness of using PVD for specific applications, particularly in industries requiring high-volume production, complex geometries, or precise color control.
Summary Table:
Disadvantage | Description |
---|---|
High Cost | Expensive due to specialized equipment, energy requirements, and expertise. |
Line of Sight Limitation | Only coats surfaces directly exposed to the vapor source. |
Slow Processing Speed | Low deposition rates lead to longer processing times. |
Color Destruction | Aggressively alters or destroys colors, causing material wastage. |
Dependence on Substrate | Coating effectiveness varies based on the substrate material. |
Equipment Requirements | Requires costly, specialized equipment and expertise. |
Size Limitations | Limited by vacuum chamber size, making it unsuitable for large or complex parts. |
Need help deciding if PVD coating is right for your project? Contact our experts today for personalized advice!