Rotary kilns, including electric rotary kilns, are widely used in industries for thermal processing, but they come with several disadvantages. These include operational challenges such as dust generation, low thermal efficiency, and non-uniform product quality. Structural issues like thermal stresses and poor mixing due to material tumbling can also affect performance. However, electric heating rotary kilns offer some advantages, such as avoiding corrosion and environmental pollution, making them a more economical and eco-friendly option compared to gas or oil-fired kilns.
Key Points Explained:
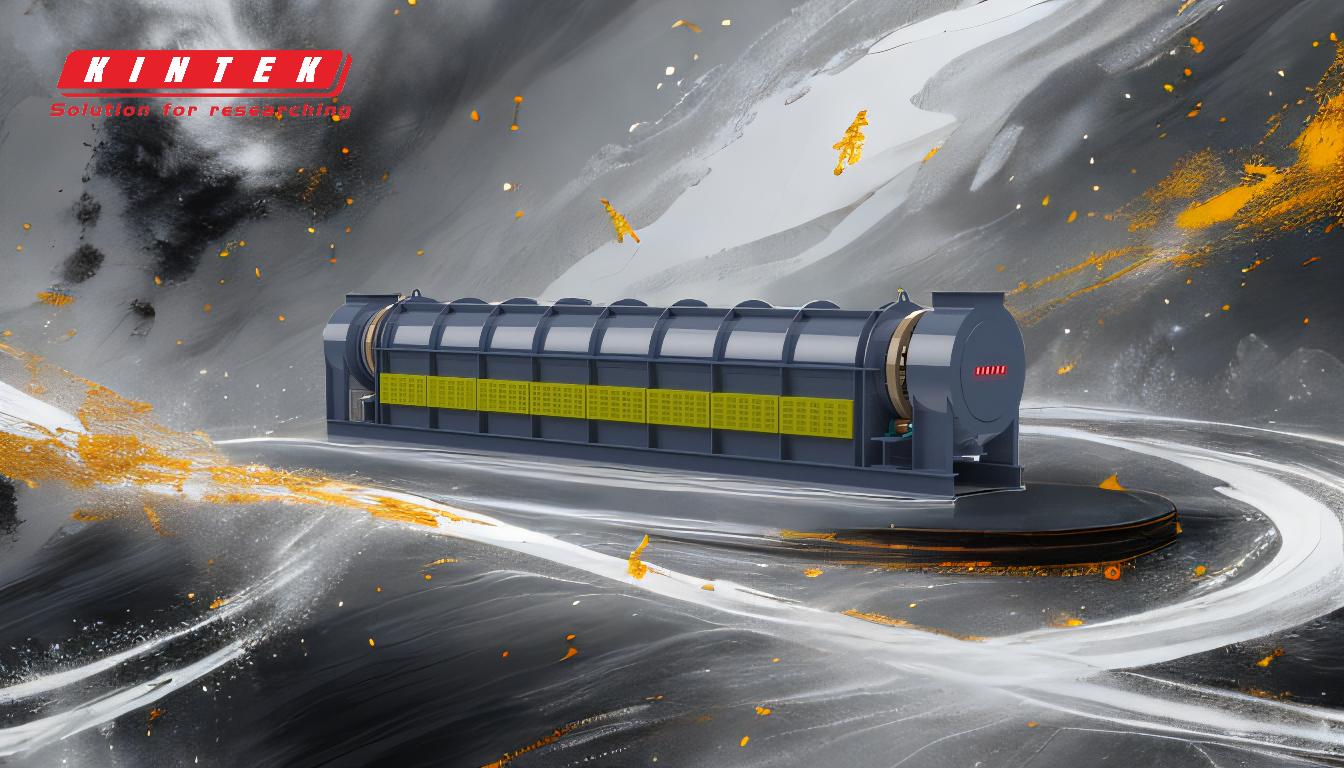
-
Operational Challenges:
- Dust Generation: Rotary kilns often produce significant amounts of dust during operation, which can lead to environmental and health concerns. This requires additional dust collection systems, increasing operational costs.
- Low Thermal Efficiency: The thermal efficiency of rotary kilns is generally lower compared to other types of furnaces. This inefficiency results in higher energy consumption and increased operational costs.
- Non-Uniform Product Quality: Achieving consistent product quality can be challenging due to uneven heating and mixing within the kiln. This can lead to variations in the final product, affecting its performance and market value.
-
Structural and Material Handling Issues:
- Poor Mixing: While dams in rotary kilns increase retention time and bed depth, not all materials tumble well. Poor mixing can lead to large temperature variations and inconsistent product quality.
- Thermal Stresses: The structural integrity of the kiln can be compromised due to thermal stresses. These stresses can cause cracks and other damage, leading to maintenance issues and potential downtime.
-
Advantages of Electric Heating Rotary Kilns:
- Avoidance of Corrosion: Electric heating rotary kilns do not produce SO2 gas, which can cause corrosion in gas or oil-fired kilns. This extends the lifespan of the kiln and reduces maintenance costs.
- Environmental Benefits: Electric kilns are more environmentally friendly as they do not emit harmful gases like SO2. This makes them a preferable option in regions with strict environmental regulations.
- Economic Efficiency: Despite the initial higher cost, electric rotary kilns can be more economical in the long run due to lower maintenance costs and higher operational efficiency.
By understanding these disadvantages and advantages, purchasers can make more informed decisions when selecting rotary kilns for their specific industrial needs.
Summary Table:
Category | Disadvantages | Solutions/Advantages |
---|---|---|
Operational Challenges | - Dust generation: Environmental and health concerns, increased costs. | - Electric kilns avoid SO2 emissions, reducing environmental impact. |
- Low thermal efficiency: Higher energy consumption and operational costs. | - Electric kilns offer higher operational efficiency and lower long-term costs. | |
- Non-uniform product quality: Uneven heating and mixing. | - Improved mixing mechanisms and consistent heating in electric kilns. | |
Structural Issues | - Poor mixing: Large temperature variations and inconsistent product quality. | - Advanced design features in electric kilns ensure better material handling. |
- Thermal stresses: Cracks, maintenance issues, and potential downtime. | - Electric kilns reduce thermal stresses, extending lifespan and reducing maintenance. | |
Environmental Impact | - Gas/oil-fired kilns emit harmful gases like SO2, causing corrosion and pollution. | - Electric kilns are eco-friendly, emitting no harmful gases and complying with regulations. |
Discover how electric rotary kilns can overcome traditional challenges—contact us today to learn more!