Rotary kiln incinerators, while effective for certain types of waste disposal, come with several significant disadvantages. These include low thermal efficiency, poor temperature control, and environmental pollution. Additionally, they pose safety hazards, have a short lifespan, and require high maintenance. The challenges of dust generation, non-uniform product quality, and structural limitations further complicate their operation. These factors make rotary kiln incinerators less efficient and more problematic compared to other waste disposal methods, especially in terms of environmental impact and operational costs.
Key Points Explained:
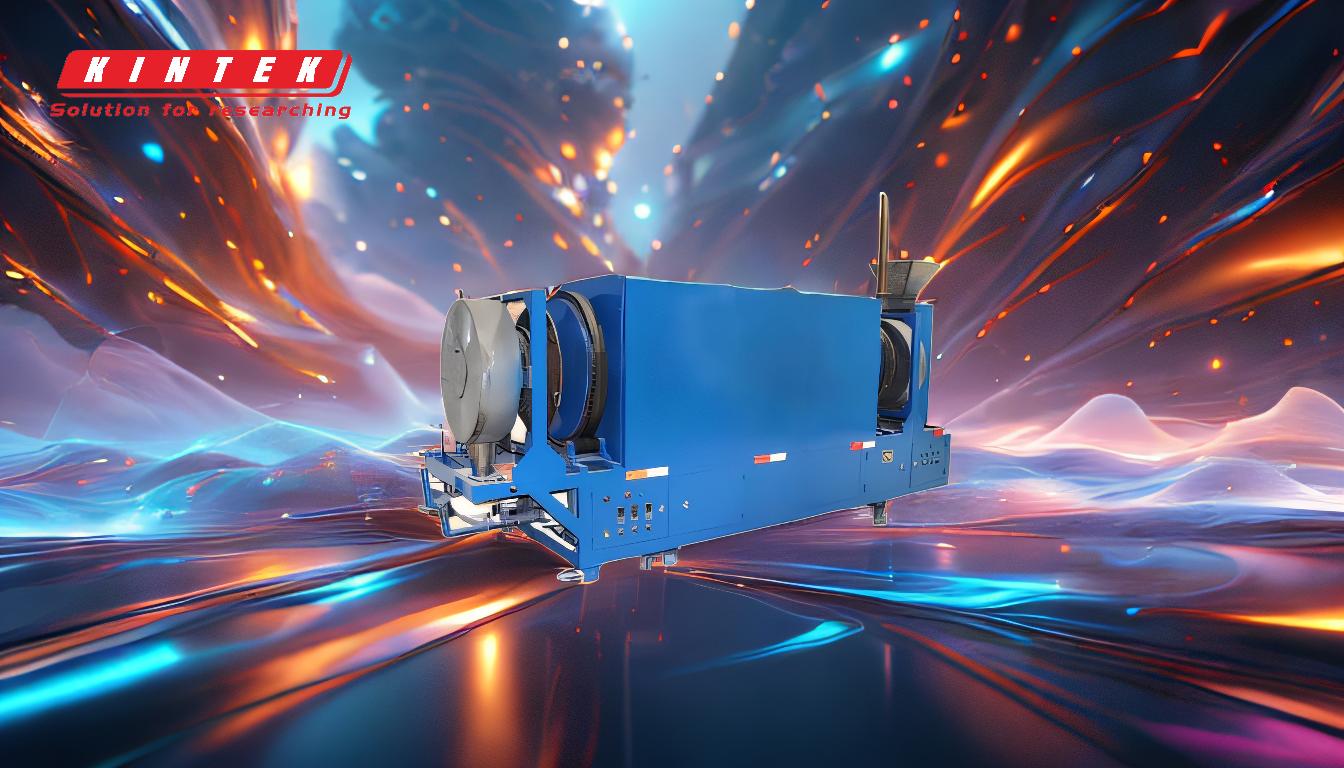
-
Low Thermal Efficiency:
- Rotary kiln incinerators often have a low heat conversion efficiency, typically ranging from 30% to 70%. This means a significant portion of the heat generated is not effectively used, leading to higher energy consumption and operational costs.
- The inefficiency is partly due to heat loss through the kiln's walls and the difficulty in maintaining optimal combustion conditions.
-
Poor Temperature Control:
- Accurate temperature control is challenging in rotary kiln incinerators. This can result in inconsistent product quality, including variations in yield and color differences.
- Poor temperature regulation can also lead to incomplete combustion, which may produce harmful by-products and reduce the overall efficiency of the incineration process.
-
Short Lifespan and High Maintenance:
- Rotary kilns generally have a shorter lifespan compared to other types of incinerators. This is due to the high wear and tear from continuous operation at high temperatures.
- Maintenance is labor-intensive and difficult, often requiring specialized skills and equipment. This increases downtime and operational costs.
-
Safety Hazards:
- There are significant safety risks associated with rotary kiln incinerators, including electric leakage, electric shock, and gas leakage fires. These hazards can pose serious threats to operators and the surrounding environment.
- The high temperatures and volatile nature of the materials being processed further exacerbate these risks.
-
Environmental Pollution:
- Rotary kiln incinerators are not environmentally friendly. They produce emissions that can contribute to air pollution, including particulate matter, toxic gases, and greenhouse gases.
- Regulatory compliance can be challenging, as these incinerators are subject to stringent environmental and safety regulations.
-
Dust Generation and Non-Uniform Product Quality:
- Dust generation is a common issue in rotary kiln operations, which can lead to environmental contamination and health hazards for workers.
- Non-uniform product quality is another drawback, as the inconsistent processing conditions can result in variations in the final product, affecting its usability and market value.
-
Structural Limitations:
- The length and diameter of rotary kilns are limited by structural constraints. Very long kilns face challenges in coping with thermal expansion and contraction, while large diameters can lead to shell deformation and flexure during rotation.
- These structural limitations can affect the kiln's performance and longevity, requiring additional engineering solutions to mitigate these issues.
In summary, while rotary kiln incinerators offer certain advantages such as high temperature and long residence time for waste disposal, their disadvantages in terms of efficiency, safety, environmental impact, and maintenance make them less favorable compared to alternative technologies.
Summary Table:
Disadvantage | Details |
---|---|
Low Thermal Efficiency | Heat conversion efficiency ranges from 30% to 70%, leading to energy waste. |
Poor Temperature Control | Inconsistent product quality and incomplete combustion risks. |
Short Lifespan & High Maintenance | High wear and tear, labor-intensive repairs, and increased downtime. |
Safety Hazards | Risks of electric leakage, gas fires, and operator safety concerns. |
Environmental Pollution | Emissions of particulate matter, toxic gases, and greenhouse gases. |
Dust Generation | Environmental contamination and health hazards for workers. |
Non-Uniform Product Quality | Variations in yield, color, and usability due to inconsistent processing. |
Structural Limitations | Length and diameter constraints affect performance and longevity. |
Looking for a better waste disposal solution? Contact our experts today to explore alternatives!