Sputtering deposition is a widely used technique for thin-film deposition, but it comes with several disadvantages that can affect its efficiency, cost, and application scope. These include issues like overheating, charge build-up, high costs of materials, difficulty in controlling stoichiometry, and challenges in reactive sputtering. Understanding these drawbacks is crucial for selecting the appropriate deposition method for specific applications.
Key Points Explained:
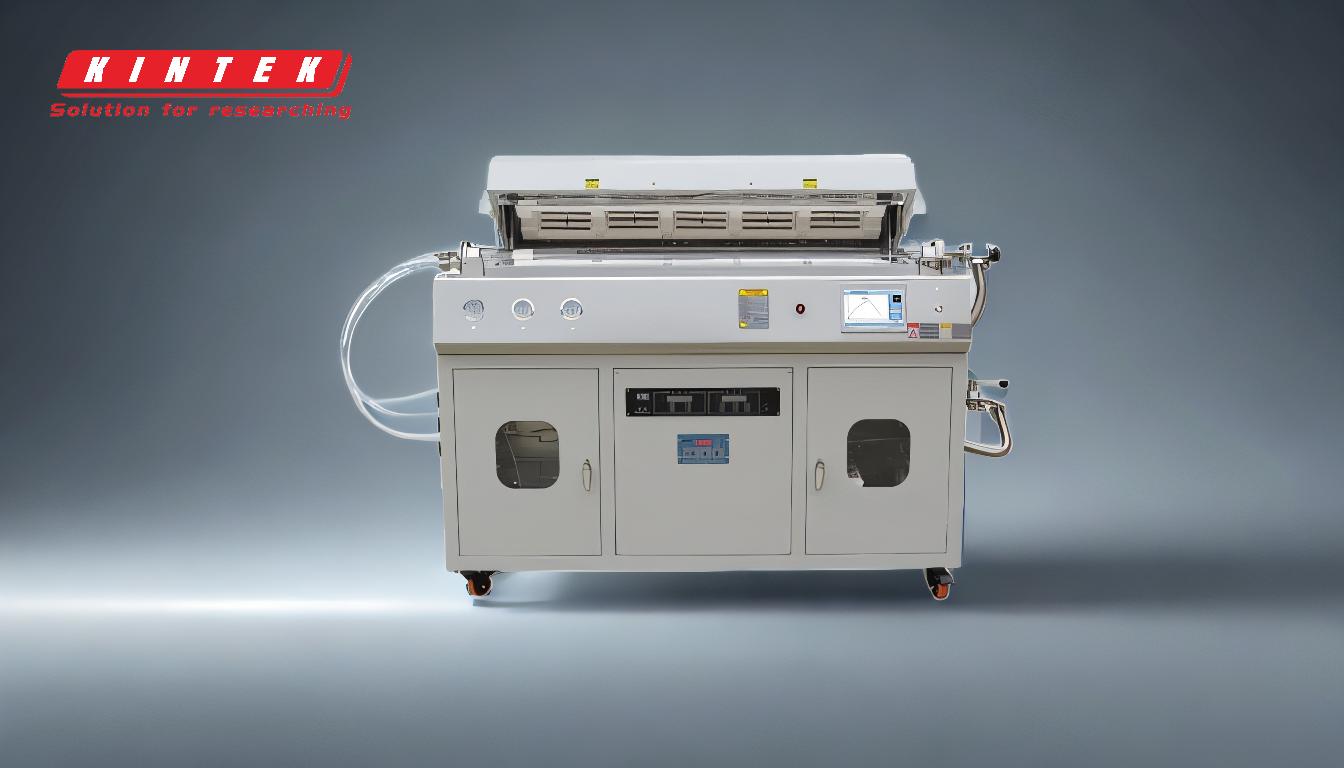
-
Overheating in RF Sputtering:
- RF sputtering requires higher power input to generate radio waves, which can lead to overheating. This is particularly problematic in applications where precise temperature control is necessary to maintain the integrity of the substrate or the quality of the deposited film.
-
Charge Build-up in DC Sputtering:
- In DC sputtering, the large number of ions in the chamber can lead to charge build-up on the target material. This can cause arcing and damage to the target, reducing the efficiency of the deposition process and potentially leading to defects in the thin film.
-
High Cost of Materials:
- The materials used in sputtering, especially metals, can be quite expensive. This high cost can restrict the use of sputtering in certain applications where budget constraints are a significant consideration.
-
Difficulty in Stoichiometry Control:
- Achieving the desired chemical composition (stoichiometry) in the deposited film can be challenging. This is particularly true for complex materials where precise control over the deposition of multiple elements is required.
-
Challenges in Reactive Sputtering:
- Reactive sputtering, which involves the use of reactive gases to form compounds on the substrate, can lead to undesired outcomes. These include the formation of non-stoichiometric compounds or the incorporation of impurities, which can degrade the performance of the thin film.
-
Complexity and Cost of Equipment:
- Sputtering systems are complex and require significant investment in terms of equipment and maintenance. The need for high vacuum conditions and precise control over process parameters adds to the overall cost and complexity of the system.
-
Limited Deposition Rates:
- Compared to other deposition techniques, sputtering can have relatively low deposition rates. This can be a disadvantage in high-throughput manufacturing processes where speed is a critical factor.
-
Potential for Contamination:
- The sputtering process can introduce contaminants into the thin film, especially if the vacuum chamber or target material is not sufficiently clean. This can affect the quality and performance of the final product.
Understanding these disadvantages is essential for making informed decisions about the use of sputtering deposition in various applications. While it offers many benefits, such as high-quality thin films and versatility in materials, the drawbacks must be carefully considered to ensure the best outcomes for specific projects.
Summary Table:
Disadvantage | Description |
---|---|
Overheating in RF Sputtering | High power input causes overheating, affecting substrate integrity and film quality. |
Charge Build-up in DC Sputtering | Ion accumulation leads to arcing, damaging the target and reducing deposition efficiency. |
High Cost of Materials | Expensive materials, especially metals, limit budget-sensitive applications. |
Difficulty in Stoichiometry Control | Challenges in achieving precise chemical composition for complex materials. |
Challenges in Reactive Sputtering | Reactive gases can cause non-stoichiometric compounds or impurities, degrading film performance. |
Complexity and Cost of Equipment | High investment in equipment and maintenance due to system complexity and vacuum requirements. |
Limited Deposition Rates | Slower deposition rates compared to other techniques, impacting high-throughput processes. |
Potential for Contamination | Contaminants from vacuum chambers or targets can reduce film quality and performance. |
Need help choosing the right deposition method for your project? Contact our experts today for tailored solutions!