Thermal evaporation, while a cost-effective method for depositing thin films, has several notable disadvantages. These include challenges with material compatibility, such as boat cracking and thermal shock, as well as issues with film quality, including poor uniformity, high impurity levels, and low-density films. Additionally, depositing alloys is difficult due to varying vapor pressures of components, and the method has limited scalability. Despite its higher deposition rates compared to sputtering, these drawbacks make thermal evaporation less suitable for certain applications, particularly those requiring high-purity, uniform, and dense films.
Key Points Explained:
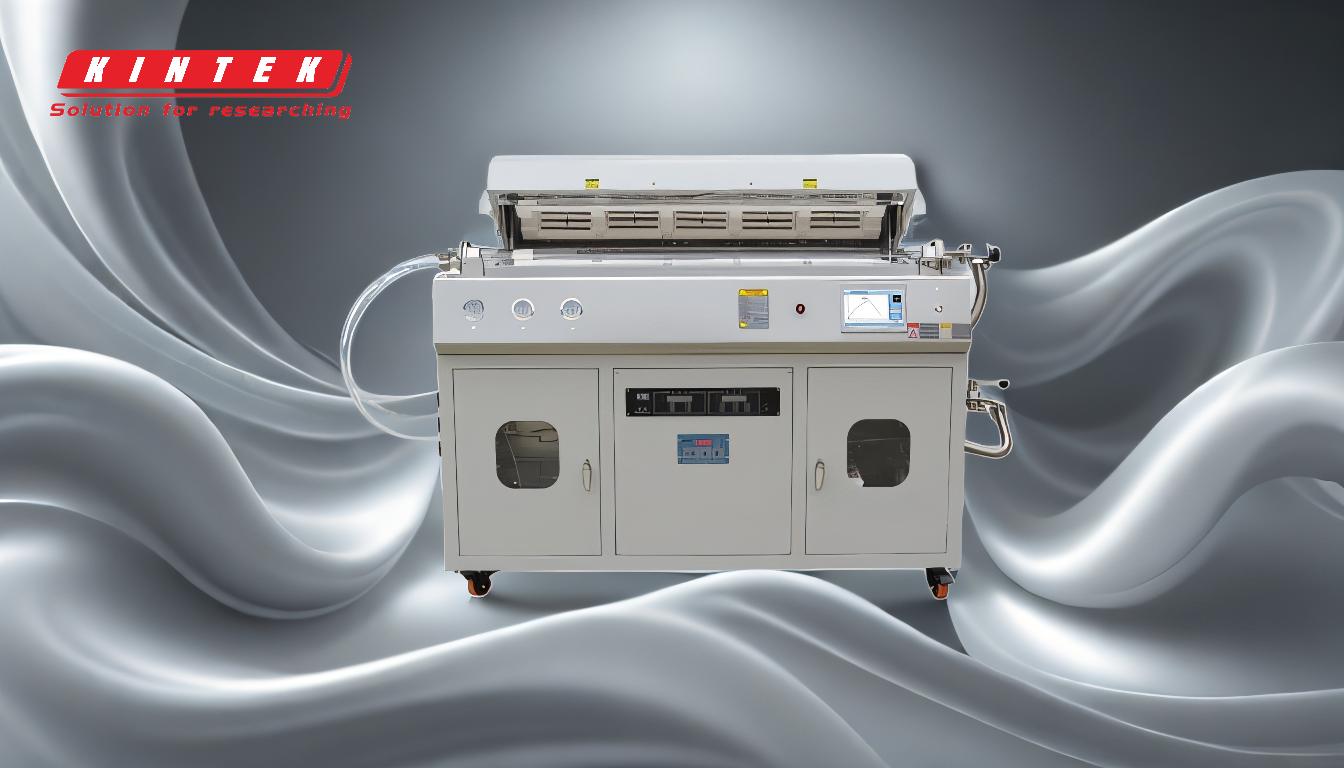
-
Boat Cracking and Thermal Shock:
- Boat Cracking: This occurs due to alloying between the boat material and the evaporant at high temperatures. Once cracked, the boat must be discarded, leading to increased costs and downtime.
- Thermal Shock: Rapid heating and cooling can cause thermal shock, leading to boat cracking. To mitigate this, power to the source must be ramped up and down smoothly to ensure uniform heating.
-
Film Quality Issues:
- Poor Uniformity: Without the use of planetary systems and masks, achieving uniform film thickness is challenging.
- High Impurity Levels: Thermal evaporation tends to have the highest impurity levels among physical vapor deposition (PVD) methods.
- Low-Density Films: The films produced are often of low density, though this can be improved with ion-assist techniques.
- Moderate Film Stress: The films may exhibit moderate stress, which can affect their mechanical properties.
-
Challenges with Alloy Deposition:
- Varying Vapor Pressures: Alloys contain materials with different vapor pressures, making it difficult to control the evaporation rates of each component.
- Complex Processes: One approach involves melting two sources simultaneously in separate crucibles and controlling each evaporation rate separately, which is complex and difficult to manage.
-
Limited Scalability:
- Scalability Issues: Thermal evaporation is not easily scalable, making it less suitable for large-scale industrial applications.
-
Comparison with Sputtering:
- Higher Deposition Rates: Thermal evaporation offers higher deposition rates compared to sputtering, but this advantage is offset by the aforementioned drawbacks.
In summary, while thermal evaporation is a cost-effective method for certain applications, its disadvantages, such as boat cracking, poor film quality, difficulty in alloy deposition, and limited scalability, make it less ideal for high-precision and large-scale uses. For more detailed information on thermal evaporation, you can refer to this thermal evaporation resource.
Summary Table:
Disadvantage | Description |
---|---|
Boat Cracking | Alloying between boat material and evaporant causes cracking, increasing costs. |
Thermal Shock | Rapid heating/cooling leads to cracking; requires smooth power ramping. |
Poor Film Uniformity | Uniform thickness is hard to achieve without planetary systems or masks. |
High Impurity Levels | Highest impurity levels among PVD methods. |
Low-Density Films | Films are often low density but can be improved with ion-assist techniques. |
Alloy Deposition Challenges | Varying vapor pressures make controlling evaporation rates difficult. |
Limited Scalability | Not easily scalable for large-scale industrial applications. |
Need a better solution for thin film deposition? Contact our experts today to explore alternatives!