Thermal evaporation, while a widely used physical vapor deposition (PVD) technique, has several notable drawbacks that can impact its effectiveness and suitability for certain applications. The primary disadvantages include high impurity levels, low-density film quality, moderate film stress, limited scalability, and challenges related to boat cracking and thermal shock. Additionally, contamination from crucibles and poor film uniformity without advanced systems like planetary fixtures and masks are significant concerns. These drawbacks can affect the quality, durability, and performance of the deposited films, making it essential to carefully consider these limitations when choosing thermal evaporation for specific applications.
Key Points Explained:
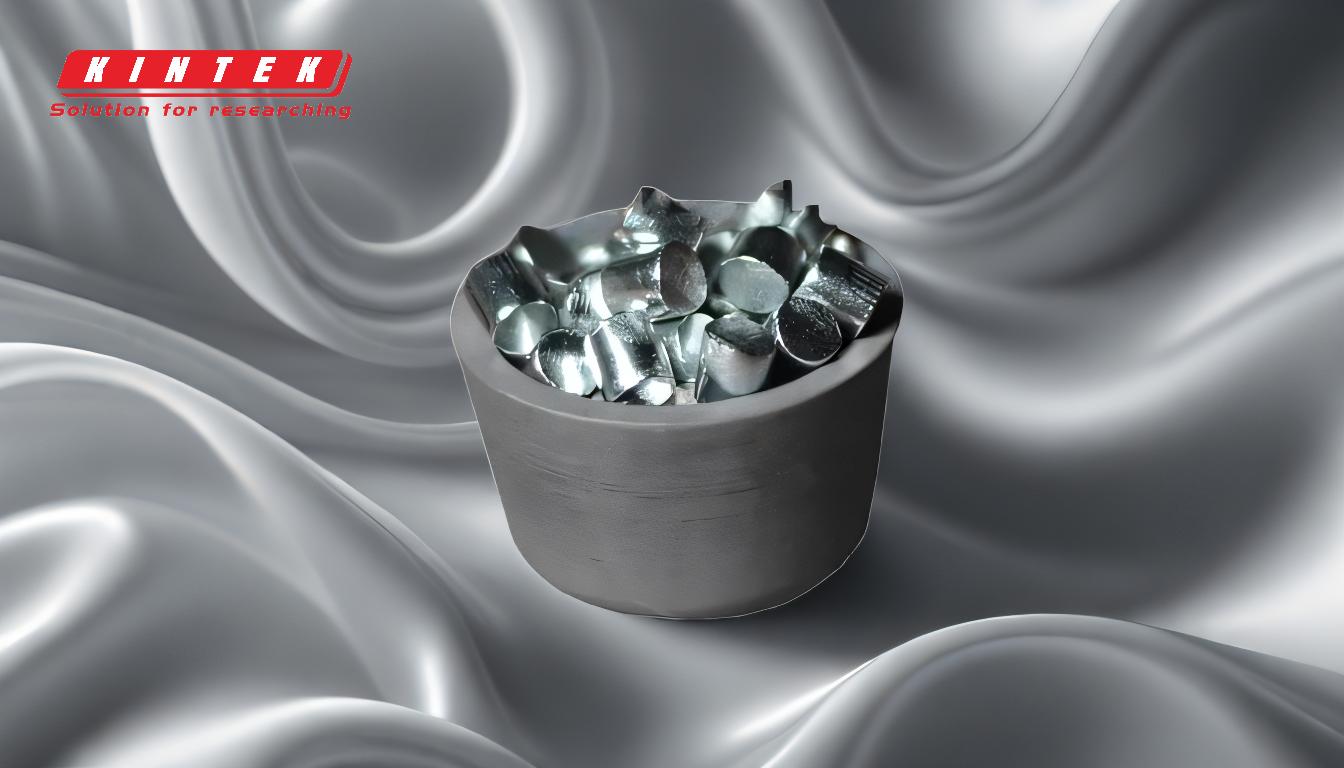
-
High Impurity Levels
- Thermal evaporation is known to have the highest impurity levels among PVD methods.
- Impurities can originate from the evaporation source, crucible, or surrounding environment.
- Contamination-free crucibles are expensive, and high-temperature evaporation often requires graphite crucibles, which may introduce carbon impurities.
- This drawback can compromise the purity and performance of the deposited films, particularly in applications requiring high material quality, such as electronics or optics.
-
Low-Density Film Quality
- Films produced by thermal evaporation tend to have low density, which can affect their mechanical and optical properties.
- Low-density films may exhibit poor adhesion, reduced durability, and inferior performance in demanding environments.
- While ion-assisted deposition (IAD) can improve film density, it adds complexity and cost to the process.
-
Moderate Film Stress
- Thermal evaporation often results in films with moderate internal stress.
- This stress can lead to issues such as cracking, delamination, or reduced adhesion to the substrate.
- Managing film stress requires careful process optimization, which can increase production time and cost.
-
Limited Scalability
- Thermal evaporation is less scalable compared to other PVD methods, such as sputtering.
- The process is typically limited to smaller-scale applications due to challenges in achieving uniform deposition over large areas.
- Scaling up the process often requires additional equipment, such as planetary systems, which increases complexity and cost.
-
Boat Cracking and Thermal Shock
- Boat cracking is a common issue in thermal evaporation, caused by alloying between the boat material and the evaporant at high temperatures.
- Once cracked, the boat must be replaced, leading to increased material costs and downtime.
- Thermal shock, resulting from rapid heating and cooling, can also cause boat cracking. To mitigate this, power must be ramped up and down smoothly, which can slow down the process.
-
Poor Film Uniformity Without Advanced Systems
- Achieving uniform film thickness and composition can be challenging without the use of planetary systems and masks.
- Non-uniform films can lead to inconsistent performance, particularly in applications requiring precise control over film properties.
- Implementing advanced systems to improve uniformity increases equipment complexity and cost.
-
Contamination from Crucibles
- Crucibles used in thermal evaporation can introduce contaminants into the deposited material.
- High-purity crucibles are expensive, and for very high-temperature evaporation, graphite crucibles may be the only option, potentially introducing carbon impurities.
- Careful selection and maintenance of crucibles are necessary to minimize contamination, adding to the operational complexity.
-
Material Limitations
- Thermal evaporation is not suitable for all materials, particularly those with high melting points or complex compositions.
- Some materials may decompose or react with the crucible or boat material during evaporation, limiting the range of materials that can be effectively deposited.
Conclusion:
While thermal evaporation offers advantages such as high deposition rates and material utilization efficiency, its drawbacks must be carefully considered. High impurity levels, low-density films, moderate film stress, limited scalability, boat cracking, thermal shock, poor uniformity, and contamination risks are significant challenges that can impact the quality and performance of the deposited films. For applications requiring high purity, uniformity, and scalability, alternative PVD methods may be more suitable. However, with proper process optimization and the use of advanced techniques like ion-assisted deposition, some of these drawbacks can be mitigated, making thermal evaporation a viable option for specific applications.
Summary Table:
Disadvantage | Key Issues |
---|---|
High Impurity Levels | Contamination from crucibles, environment, or evaporation source. |
Low-Density Film Quality | Poor adhesion, reduced durability, and inferior mechanical properties. |
Moderate Film Stress | Risk of cracking, delamination, or reduced adhesion to substrates. |
Limited Scalability | Challenges in uniform deposition over large areas; requires costly systems. |
Boat Cracking & Thermal Shock | Alloying and thermal shock lead to frequent boat replacements. |
Poor Film Uniformity | Non-uniform thickness and composition without advanced systems. |
Contamination from Crucibles | High-purity crucibles are expensive; graphite crucibles may introduce carbon. |
Material Limitations | Unsuitable for high-melting-point or complex materials. |
Need help choosing the right PVD method for your application? Contact our experts today for tailored solutions!