Pyrolysis of plastic is a thermal decomposition process that occurs in the absence of oxygen, converting plastic waste into valuable products such as biochar, bio-oil, and syngas. While it offers environmental benefits by reducing reliance on fossil fuels and preventing greenhouse gas emissions from waste decomposition, the process is not without its environmental challenges. Emissions from pyrolysis can include harmful gases like carbon monoxide (CO) and carbon dioxide (CO2), as well as tars and ashes, which may pose risks to air quality and ecosystems. The sustainability of pyrolysis depends on factors such as feedstock sourcing, process efficiency, and the management of byproducts.
Key Points Explained:
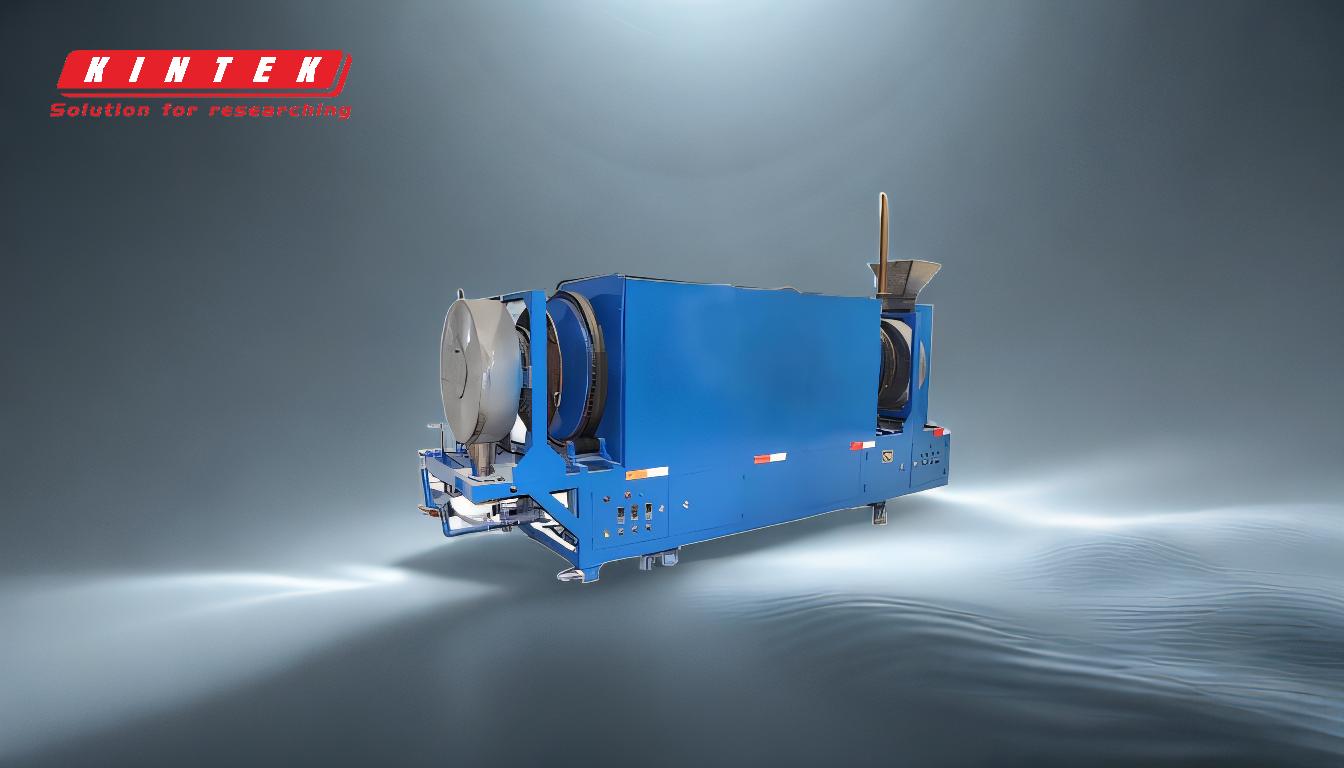
-
Emissions from Pyrolysis of Plastic:
- Gaseous Emissions: The pyrolysis of plastic releases gases such as carbon monoxide (CO) and carbon dioxide (CO2). These gases are byproducts of the thermal decomposition process and can contribute to air pollution if not properly managed.
- Liquid Byproducts: The process also produces liquid byproducts like tars and pyrolysis oil. While these liquids can be further refined and utilized, improper handling can lead to environmental contamination.
- Solid Residues: Ashes and biochar are solid residues generated during pyrolysis. Biochar has potential applications in soil amendment and carbon sequestration, but ashes may contain heavy metals or other pollutants that require careful disposal.
-
Environmental Benefits of Pyrolysis:
- Greenhouse Gas Reduction: Pyrolysis helps mitigate greenhouse gas emissions by preventing the release of CO2 and methane (CH4) from plastic waste decomposition. It is estimated that pyrolysis can offset up to 4 tonnes of CO2 equivalent per tonne of waste processed.
- Resource Recovery: The process transforms non-recyclable plastics into value-added products like biochar, pyrolysis oil, and syngas, which can replace fossil fuels and reduce environmental contamination.
- Complementary Technology: Pyrolysis can be integrated with other waste management technologies, such as anaerobic digestion, to enhance overall efficiency and sustainability.
-
Potential Environmental Risks:
- Air Pollution: The release of gases like CO and CO2 during pyrolysis can contribute to air pollution if emission control systems are not in place.
- Water and Soil Contamination: Improper disposal of liquid byproducts or solid residues can lead to contamination of water and soil, posing risks to ecosystems and human health.
- Back-up Fuel Requirements: The process may require additional fuel to maintain optimal operating conditions, which could offset some of its environmental benefits if the fuel is derived from non-renewable sources.
-
Sustainability Considerations:
- Feedstock Sourcing: The environmental impact of pyrolysis depends on the sustainability of the feedstock. Unsustainably sourced biomass or plastic waste can exacerbate deforestation and resource depletion.
- Process Efficiency: Advanced pyrolysis technologies with efficient emission control systems can minimize environmental risks and maximize resource recovery.
- Byproduct Management: Proper handling and utilization of byproducts are crucial to ensure that pyrolysis remains an environmentally friendly waste management solution.
In conclusion, while pyrolysis of plastic offers significant environmental benefits by reducing greenhouse gas emissions and recovering valuable resources, it also poses challenges related to emissions and byproduct management. Addressing these challenges through sustainable practices and advanced technologies is essential to maximize the positive impact of pyrolysis on the environment.
Summary Table:
Aspect | Details |
---|---|
Gaseous Emissions | CO, CO2 released; contributes to air pollution if not managed. |
Liquid Byproducts | Tars and pyrolysis oil; improper handling can cause contamination. |
Solid Residues | Biochar (useful) and ashes (potential pollutants); require careful disposal. |
Environmental Benefits | Reduces greenhouse gases, recovers resources, integrates with other tech. |
Potential Risks | Air pollution, water/soil contamination, back-up fuel requirements. |
Sustainability Factors | Feedstock sourcing, process efficiency, byproduct management. |
Learn how to optimize plastic pyrolysis for sustainability—contact our experts today!