The performance of a ball mill is influenced by a variety of factors, including the physical dimensions of the mill, the properties of the material being ground, the characteristics of the grinding media, and operational parameters. Key factors include the drum diameter and its ratio to length, the physical-chemical properties of the feed material, the size and filling ratio of the grinding balls, the shape of the armor surface, the rotation speed, the desired fineness of the milled product, and the efficiency of product removal. Additionally, the residence time of the material in the mill, the hardness of the grinding material, and the feed rate also play significant roles in determining the overall grinding efficiency and productivity of the ball mill.
Key Points Explained:
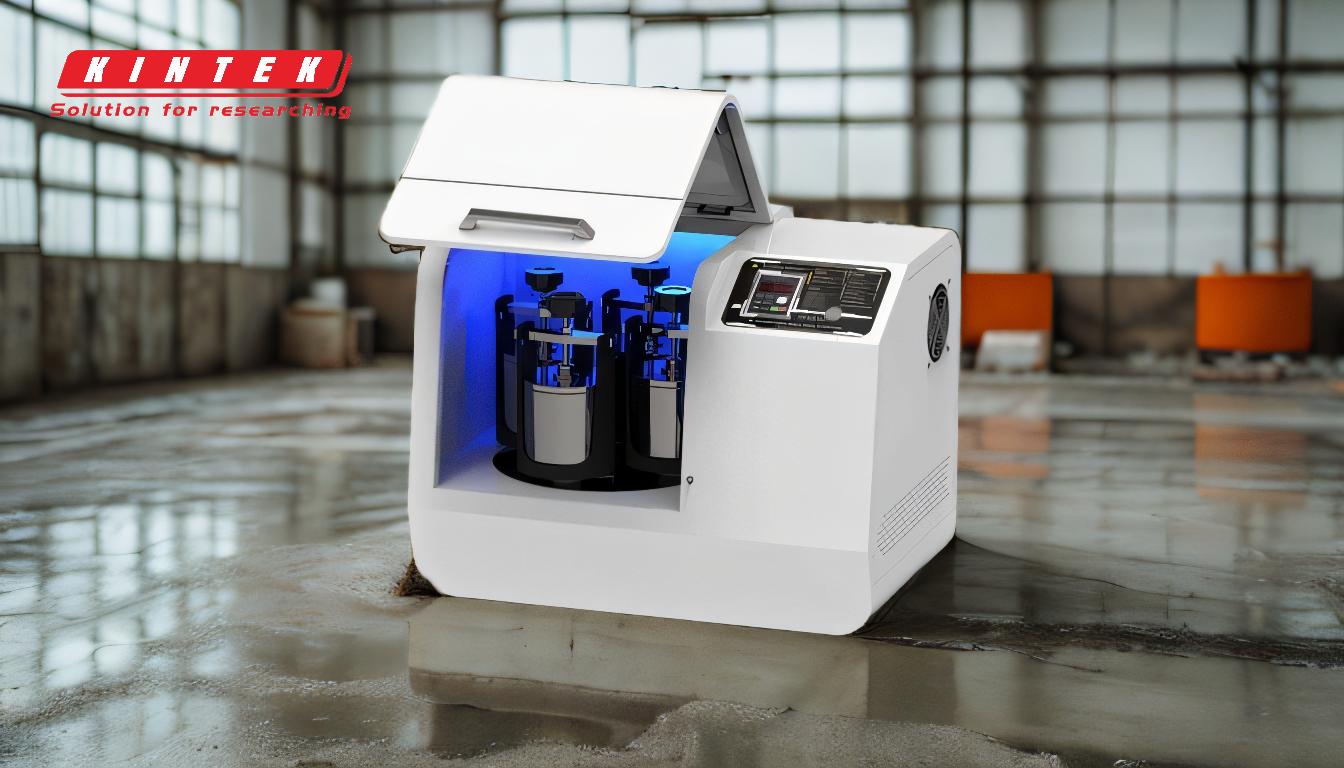
-
Drum Dimensions and Design:
- Drum Diameter and Length Ratio (L:D Ratio): The diameter of the drum and the ratio of its length to diameter (L:D ratio) are critical for optimal performance. An optimum L:D ratio typically falls between 1.56 and 1.64. This ratio ensures efficient grinding by balancing the material's residence time and the energy input.
- Armor Surface Shape: The shape of the internal armor surface can influence the trajectory of the grinding balls and the material, affecting the grinding efficiency. A well-designed surface can enhance the grinding action by optimizing the impact and abrasion forces.
-
Material Properties:
- Physical-Chemical Properties of Feed Material: The hardness, density, and chemical composition of the material being ground significantly affect the grinding process. Harder materials require more energy and time to grind, while materials with specific chemical properties might react differently under grinding conditions.
- Nature of the Grinding Material: The nature of the material, such as its brittleness or toughness, also plays a role. Brittle materials tend to fracture more easily, while tougher materials may require more intensive grinding.
-
Grinding Media Characteristics:
- Ball Size and Filling Ratio: The size of the grinding balls and the percentage of the mill volume filled with these balls (filling ratio) are crucial. Larger balls can deliver more impact force, suitable for coarse grinding, while smaller balls are better for fine grinding. The filling ratio affects the energy transfer and the grinding efficiency.
- Density and Number of Balls: The density and number of balls influence the grinding kinetics. Higher density balls can provide more grinding power, while the number of balls affects the frequency of impacts and the overall grinding action.
-
Operational Parameters:
- Rotation Speed: The speed at which the mill rotates determines the centrifugal force acting on the grinding balls and the material. Optimal rotation speed ensures that the balls are lifted to the right height before cascading down, providing the necessary impact for grinding.
- Feed Rate and Level: The rate at which material is fed into the mill and the level of material in the vessel affect the grinding efficiency. Overloading the mill can reduce the grinding action, while underloading can lead to inefficient use of energy.
- Residence Time: The time the material spends in the mill chamber affects the degree of grinding. Longer residence times can lead to finer grinding but may also reduce throughput.
-
Product Removal:
- Timely Removal of Ground Product: Efficient removal of the ground product is essential to prevent over-grinding and to maintain a steady flow of material through the mill. Proper discharge mechanisms ensure that the mill operates at optimal capacity without clogging or unnecessary energy consumption.
-
Milling Fineness:
- Desired Fineness of Milled Product: The target fineness of the product influences the grinding parameters. Achieving a finer product may require adjustments in ball size, rotation speed, and residence time to ensure that the material is ground to the desired specification.
By carefully considering and optimizing these factors, the performance of a ball mill can be significantly enhanced, leading to improved grinding efficiency, higher productivity, and better-quality milled products.
Summary Table:
Category | Key Factors |
---|---|
Drum Dimensions & Design | - Drum diameter & L:D ratio (1.56–1.64 optimal) - Armor surface shape |
Material Properties | - Hardness, density, chemical composition - Brittleness or toughness |
Grinding Media | - Ball size & filling ratio - Density & number of balls |
Operational Parameters | - Rotation speed - Feed rate & level - Residence time |
Product Removal | - Timely removal of ground product |
Milling Fineness | - Desired fineness of milled product |
Ready to optimize your ball mill performance? Contact our experts today for tailored solutions!