Chemical vapor deposition (CVD) is a versatile and widely used method for depositing thin films on substrates through chemical reactions in the vapor phase. The process involves several critical steps, including the transport of gaseous species, adsorption, surface reactions, and desorption. The quality and efficiency of CVD are influenced by various factors, such as the type of precursor, deposition temperature, pressure, and the nature of the substrate. Understanding these factors is essential for optimizing the CVD process to achieve high-quality films with desired properties.
Key Points Explained:
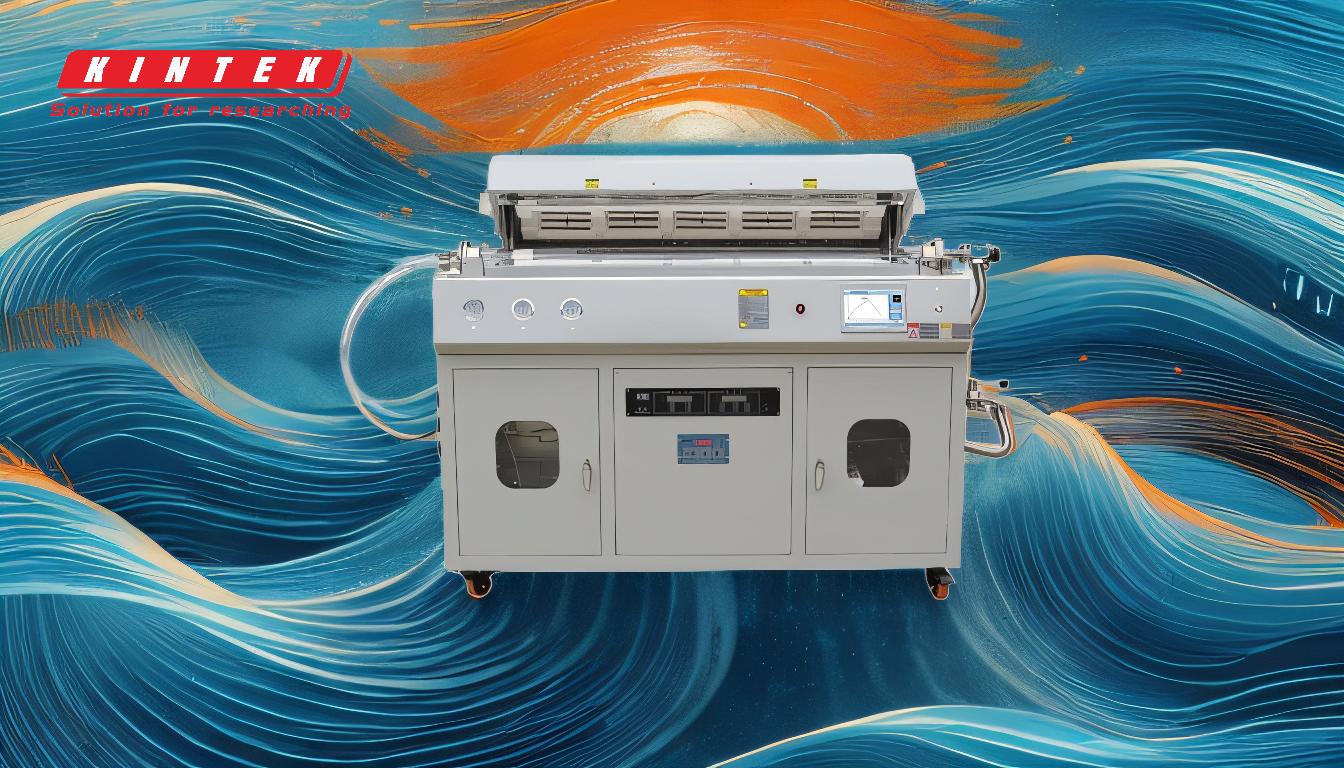
-
Types of CVD Processes:
- Aerosol-Assisted CVD: This method uses an aerosol to deliver the precursor to the substrate. It is particularly useful for precursors that are not easily vaporized.
- Direct Liquid Injection CVD: In this approach, a liquid precursor is injected into a heated chamber, where it vaporizes and reacts to form the thin film.
- Plasma-Based CVD: Instead of relying solely on heat, this method uses plasma to activate the precursor gases, allowing for lower deposition temperatures and better control over film properties.
-
Steps in the CVD Process:
- Transport of Reacting Gaseous Species: The precursor gases are transported to the substrate surface.
- Adsorption: The gaseous species adsorb onto the substrate surface.
- Surface Reactions: Heterogeneous surface-catalyzed reactions occur, leading to the formation of the film.
- Surface Diffusion: The adsorbed species diffuse across the surface to growth sites.
- Nucleation and Growth: The film nucleates and grows on the substrate.
- Desorption and Transport of Byproducts: Gaseous reaction products desorb from the surface and are transported away.
-
Factors Affecting CVD:
- Precursor Type: The choice of precursor affects the deposition rate, film quality, and the types of materials that can be deposited.
- Deposition Temperature: Temperature influences the rate of chemical reactions and the mobility of atoms on the substrate surface.
- Pressure: The pressure in the deposition chamber affects the mean free path of the gas molecules and the rate of reactions.
- Substrate Nature: The material and surface condition of the substrate can influence the adhesion and uniformity of the deposited film.
- Gas Flow Rates: The flow rates of the precursor and carrier gases determine the concentration of reacting species and the uniformity of the film.
-
Advantages of CVD:
- Versatility: CVD can deposit a wide variety of materials, including metals, semiconductors, and insulators.
- Wrap-Around Properties: CVD can coat complex surfaces uniformly, making it suitable for intricate geometries.
- High Purity and Density: The films produced by CVD are typically of high purity and density, with low residual stress.
- Controlled Properties: By adjusting deposition parameters, the properties of the film, such as thickness, composition, and crystallinity, can be precisely controlled.
- Simple Equipment: CVD equipment is relatively simple and easy to operate and maintain.
-
Applications of CVD:
- Electrical Circuits: CVD is ideal for producing ultra-thin layers of materials required in electrical circuits.
- Optical Coatings: The high purity and controlled properties of CVD films make them suitable for optical applications.
- Protective Coatings: CVD can be used to deposit hard, wear-resistant coatings on tools and components.
- Semiconductor Devices: CVD is widely used in the fabrication of semiconductor devices, including transistors and diodes.
In conclusion, the factors affecting chemical vapor deposition are multifaceted, involving the type of precursor, deposition conditions, and substrate characteristics. By carefully controlling these factors, it is possible to optimize the CVD process to produce high-quality thin films with tailored properties for a wide range of applications.
Summary Table:
Factor | Impact on CVD |
---|---|
Precursor Type | Affects deposition rate, film quality, and material compatibility. |
Deposition Temperature | Influences reaction rates and atomic mobility on the substrate. |
Pressure | Determines gas molecule mean free path and reaction rates. |
Substrate Nature | Impacts film adhesion, uniformity, and overall quality. |
Gas Flow Rates | Controls concentration of reacting species and film uniformity. |
Optimize your CVD process for superior results—contact our experts today!