Grinding efficiency is a critical factor in determining the performance of grinding equipment such as bead mills and ball mills. It is influenced by several key factors, including bead size, rotor speed, type of rotor, mass of beads, rotation speed, grinding medium, material properties, filling ratio, number of grinding cycles, and residence time. These factors collectively determine the impact energy, frequency of contact between grinding media and particles, and the overall effectiveness of the grinding process. Understanding these factors helps optimize grinding operations to achieve desired particle sizes and processing rates.
Key Points Explained:
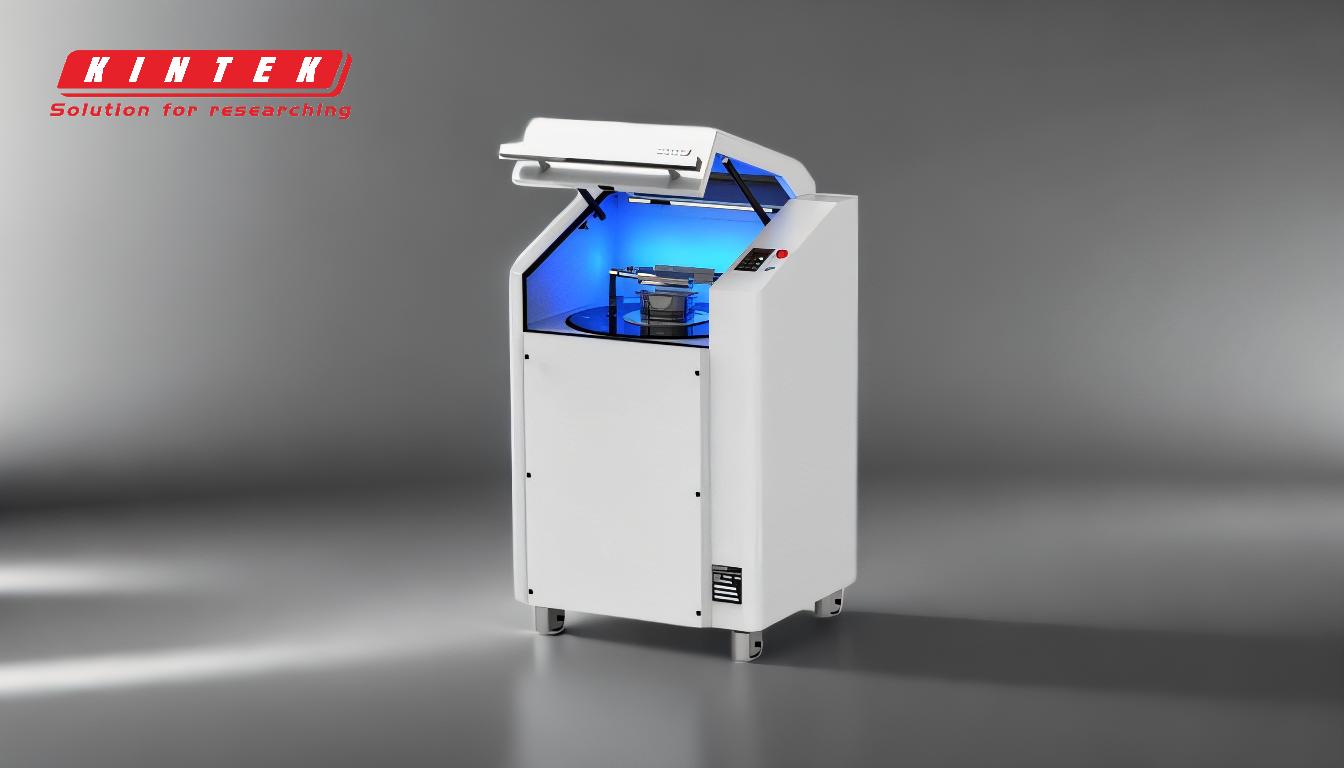
-
Bead Size:
- The size of the grinding beads directly impacts the grinding efficiency. Smaller beads provide a larger surface area for contact with particles, leading to more effective grinding. However, excessively small beads may lack the necessary impact energy to break down larger particles. Conversely, larger beads can deliver higher impact energy but may reduce the frequency of contact with particles.
- Consideration for Purchasers: When selecting beads, balance the size to ensure sufficient impact energy and contact frequency for the specific material being ground.
-
Rotor Speed:
- Rotor speed determines the kinetic energy imparted to the grinding beads. Higher speeds increase the impact energy and frequency of collisions, enhancing grinding efficiency. However, excessively high speeds can lead to overheating and wear of the equipment.
- Consideration for Purchasers: Choose equipment with adjustable rotor speeds to optimize grinding conditions for different materials and desired particle sizes.
-
Type of Rotor:
- The design of the rotor affects the movement and distribution of grinding beads within the mill. Different rotor types can create varying flow patterns, influencing the grinding efficiency and uniformity of particle size reduction.
- Consideration for Purchasers: Select a rotor design that matches the specific grinding requirements, such as achieving a narrow particle size distribution or handling abrasive materials.
-
Mass of Beads:
- The quantity of beads charged into the mill affects the grinding efficiency. An optimal mass ensures sufficient contact between beads and particles without overcrowding, which can reduce the effectiveness of the grinding process.
- Consideration for Purchasers: Follow manufacturer guidelines for bead mass to ensure optimal grinding performance and avoid overloading the mill.
-
Rotation Speed (Ball Mills):
- In ball mills, the rotation speed influences the movement of the grinding medium (balls) and the material. The critical speed is the point at which the centrifugal force equals the gravitational force, causing the balls to cascade and impact the material effectively.
- Consideration for Purchasers: Ensure the mill operates at or near the critical speed for maximum grinding efficiency.
-
Grinding Medium:
- The type and size of the grinding medium (beads or balls) play a crucial role in grinding efficiency. Different materials (e.g., steel, ceramic, or glass) and sizes are suited for specific grinding tasks, depending on the hardness and size of the material being ground.
- Consideration for Purchasers: Choose grinding media that are compatible with the material being processed and the desired particle size.
-
Material Properties:
- The hardness, brittleness, and initial particle size of the material being ground affect the grinding efficiency. Harder materials may require more energy or specialized grinding media to achieve the desired particle size.
- Consideration for Purchasers: Understand the properties of the material to select appropriate grinding equipment and media.
-
Filling Ratio:
- The filling ratio, or the percentage of the mill volume filled with grinding medium, impacts the grinding efficiency. An optimal filling ratio ensures sufficient contact between the grinding medium and the material without excessive energy consumption.
- Consideration for Purchasers: Adjust the filling ratio based on the material and desired grinding outcomes to maximize efficiency.
-
Number of Grinding Cycles:
- The number of times the material passes through the grinding process affects the final particle size. More cycles generally result in finer particles but may also increase processing time and energy consumption.
- Consideration for Purchasers: Balance the number of grinding cycles with production efficiency to achieve the desired particle size without unnecessary energy expenditure.
-
Residence Time:
- The duration that material spends inside the grinding process influences the degree of size reduction. Longer residence times allow for more extensive grinding but may also lead to over-processing or increased energy usage.
- Consideration for Purchasers: Optimize residence time to achieve the desired particle size while maintaining efficient production rates.
By carefully considering these factors, purchasers can select and operate grinding equipment that meets their specific needs, ensuring efficient and effective grinding processes.
Summary Table:
Factor | Impact on Grinding Efficiency | Consideration for Purchasers |
---|---|---|
Bead Size | Smaller beads increase surface area but may lack impact energy; larger beads deliver more energy. | Balance bead size for sufficient impact energy and contact frequency. |
Rotor Speed | Higher speeds increase impact energy but may cause overheating. | Choose equipment with adjustable rotor speeds for optimal grinding conditions. |
Type of Rotor | Rotor design affects bead movement and grinding uniformity. | Select a rotor design suited for specific grinding needs, like narrow particle size distribution. |
Mass of Beads | Optimal bead mass ensures effective contact without overcrowding. | Follow manufacturer guidelines for bead mass to avoid overloading. |
Rotation Speed | Critical speed ensures effective cascading and impact in ball mills. | Operate the mill near critical speed for maximum efficiency. |
Grinding Medium | Material and size of beads/balls influence grinding effectiveness. | Choose media compatible with material hardness and desired particle size. |
Material Properties | Hardness and brittleness affect grinding energy requirements. | Understand material properties to select appropriate equipment and media. |
Filling Ratio | Optimal filling ratio ensures sufficient contact without excessive energy use. | Adjust filling ratio based on material and desired outcomes. |
Grinding Cycles | More cycles result in finer particles but increase energy use. | Balance cycles with production efficiency to avoid unnecessary energy expenditure. |
Residence Time | Longer residence times allow for more extensive grinding but may increase energy usage. | Optimize residence time for desired particle size and efficient production rates. |
Ready to optimize your grinding process? Contact our experts today for tailored solutions!