Pyrolysis yield is influenced by a combination of factors, including operating conditions, biomass properties, and reactor design. Key factors include temperature, residence time, heating rate, biomass composition, moisture content, particle size, and reactor type. Each of these factors interacts to determine the distribution of pyrolysis products such as bio-oil, char, and gas. For example, higher temperatures favor gas production, while lower temperatures and slower heating rates favor char formation. Proper control of these variables is essential to optimize the yield and quality of the desired end products.
Key Points Explained:
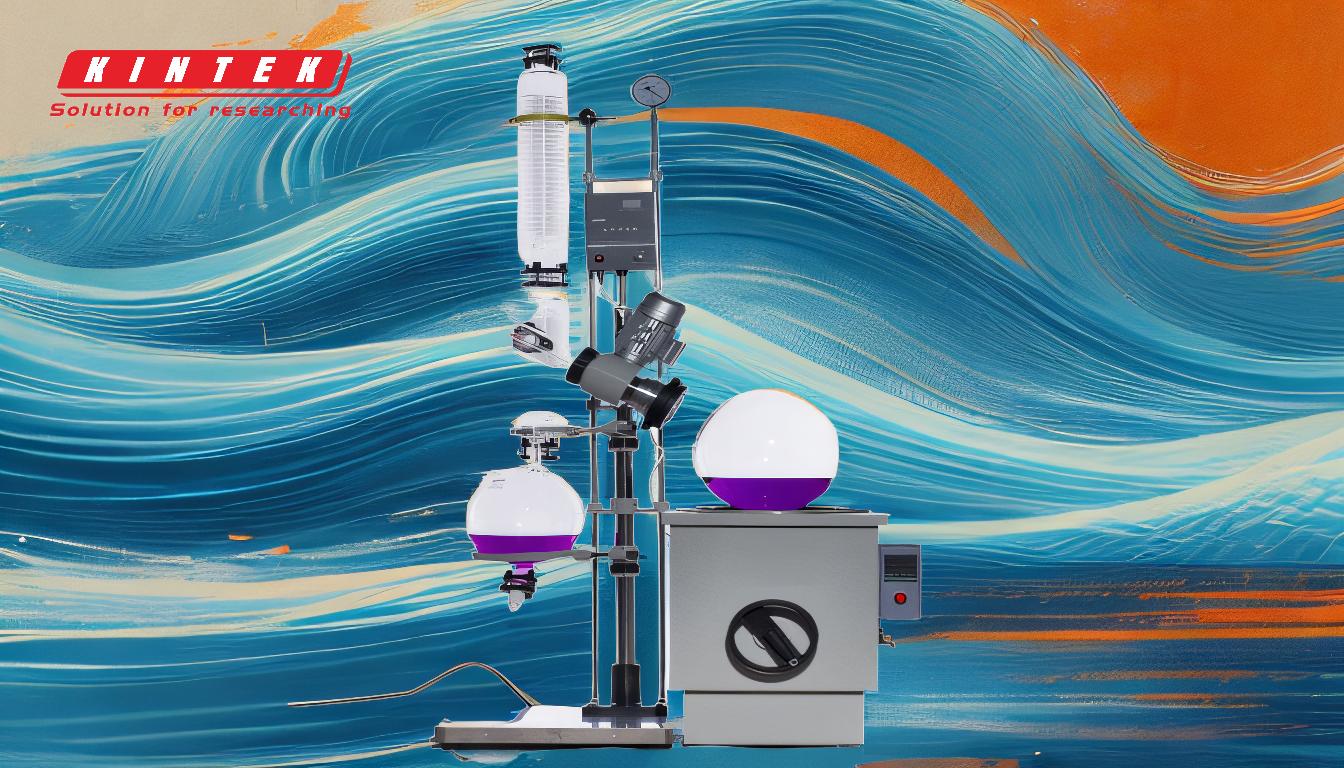
-
Temperature:
- Impact on Product Distribution: Temperature is one of the most critical factors affecting pyrolysis yield. Higher temperatures (typically above 500°C) favor the production of non-condensable gases due to the complete thermal decomposition of organic compounds. Conversely, lower temperatures (around 300-450°C) favor the formation of solid char and liquid bio-oil.
- Thermal Cracking: At elevated temperatures, thermal cracking of tar and other high-molecular-weight compounds occurs, increasing gas yield while reducing oil and char yields.
- Optimal Range: For liquid products, moderate temperatures (450-550°C) are ideal, while char production is optimized at lower temperatures.
-
Residence Time:
- Definition: Residence time refers to the duration that the biomass remains in the pyrolysis chamber.
- Effect on Conversion: Longer residence times allow for more complete thermal conversion, increasing gas yield and reducing char and liquid yields. Shorter residence times favor the production of liquid bio-oil.
- Vapor Composition: Extended residence times can lead to secondary reactions, altering the composition of pyrolysis vapors and affecting product quality.
-
Heating Rate:
- Fast vs. Slow Heating: Fast heating rates (typically above 100°C/min) promote the production of liquid bio-oil by rapidly decomposing biomass before secondary reactions occur. Slow heating rates favor char formation due to prolonged exposure to heat.
- Impact on Yield: High heating rates combined with moderate temperatures maximize liquid yield, while low heating rates at high temperatures favor gas production.
-
Biomass Composition:
- Volatile Matter and Fixed Carbon: Biomass with high volatile matter content tends to produce more gas and liquid products, while high fixed carbon content favors char formation.
- Moisture Content: High moisture content can reduce pyrolysis efficiency by requiring additional energy for evaporation, leading to lower yields of desired products.
- Particle Size: Smaller particle sizes enhance heat transfer and thermal decomposition, increasing the yield of pyrolysis oil. Larger particles may lead to incomplete pyrolysis and higher char yields.
-
Reactor Type:
- Design Influence: Different reactor designs (e.g., fluidized bed, fixed bed, rotary kiln) affect heat transfer, residence time, and product distribution.
- Pressure Conditions: Elevated pressure can favor char formation through secondary condensation reactions, while atmospheric pressure is typically used for liquid and gas production.
-
Pretreatment Conditions:
- Drying and Size Reduction: Pretreatment steps like drying and grinding can improve pyrolysis efficiency by reducing moisture content and ensuring uniform particle size.
- Chemical Pretreatment: Some pretreatments (e.g., torrefaction) can modify biomass properties, enhancing pyrolysis yield and product quality.
-
Pressure:
- Effect on Product Distribution: Increased pressure promotes secondary reactions like condensation and synthesis, favoring char formation. Lower pressure conditions are better suited for gas and liquid production.
- Reactor Settings: Pressure control is crucial for optimizing pyrolysis outcomes, especially in pressurized reactors.
-
Waste Composition:
- Organic Fraction: The efficiency of pyrolysis is highly dependent on the organic content of the feedstock. Higher organic fractions lead to greater gas yields, while inorganic materials can reduce overall efficiency.
- Heterogeneity: Mixed waste streams with varying compositions can complicate pyrolysis, requiring tailored process conditions to achieve optimal yields.
By carefully controlling these factors, pyrolysis processes can be optimized to maximize the yield of desired products, whether they are bio-oil, char, or gas. Each factor interacts with the others, making it essential to balance conditions for specific feedstock and desired outcomes.
Summary Table:
Factor | Impact on Pyrolysis Yield | Optimal Conditions |
---|---|---|
Temperature | Higher temps favor gas; lower temps favor char and bio-oil. | 450-550°C for bio-oil; 300-450°C for char. |
Residence Time | Longer times increase gas yield; shorter times favor bio-oil. | Adjust based on desired product (gas or bio-oil). |
Heating Rate | Fast rates favor bio-oil; slow rates favor char. | >100°C/min for bio-oil; slower rates for char. |
Biomass Composition | High volatile matter → gas/oil; high fixed carbon → char. | Optimize feedstock composition for target product. |
Reactor Type | Design affects heat transfer, residence time, and product distribution. | Choose reactor (e.g., fluidized bed) based on desired output. |
Pressure | Higher pressure favors char; lower pressure favors gas and bio-oil. | Adjust pressure for specific product goals. |
Particle Size | Smaller particles enhance heat transfer, increasing bio-oil yield. | Grind biomass to uniform, small particle sizes. |
Moisture Content | High moisture reduces efficiency; drying improves pyrolysis performance. | Dry feedstock to minimize moisture. |
Ready to optimize your pyrolysis process? Contact our experts today for tailored solutions!