Thin films are influenced by a variety of factors that determine their properties, quality, and performance. These factors can be broadly categorized into deposition process parameters, substrate characteristics, environmental conditions, and post-deposition considerations. Key factors include substrate temperature, deposition rate, residual gas composition, energy of incoming adatoms, and surface mobility. Additionally, structural defects, film roughness, and thickness significantly impact optical properties, while quality control, cost, and efficiency are critical for manufacturing. Understanding these factors is essential for optimizing thin film production and ensuring they meet specific application requirements.
Key Points Explained:
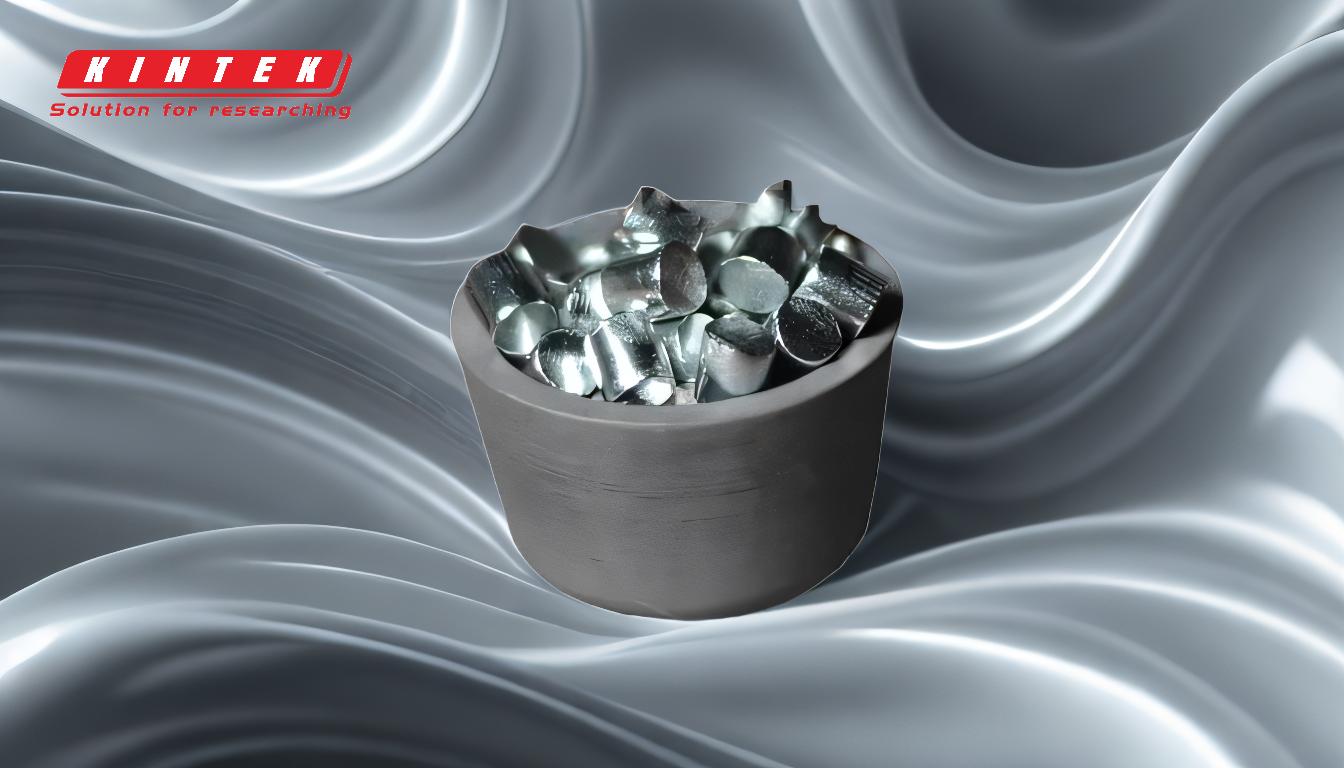
-
Deposition Process Parameters:
- Substrate Temperature: The temperature of the substrate during deposition plays a crucial role in determining the quality of the thin film. Higher temperatures (e.g., above 150 °C) provide evaporated atoms with sufficient energy to move freely, leading to better adhesion and a more uniform film.
- Deposition Rate: The rate at which material is deposited onto the substrate affects the film's microstructure. A controlled deposition rate ensures uniformity and minimizes defects.
- Energy of Incoming Adatoms: The energy of atoms or molecules arriving at the substrate influences their surface mobility and ability to form a dense, defect-free film. Higher energy can improve film quality but may also introduce stress.
-
Substrate Characteristics:
- Nature of the Substrate: The material and surface properties of the substrate (e.g., roughness, chemical composition) affect how the thin film adheres and grows. A smooth and chemically compatible substrate promotes better film formation.
- Surface Mobility: The ability of deposited atoms to move across the substrate surface impacts the film's microstructure. Higher surface mobility leads to smoother and more uniform films.
-
Environmental Conditions:
- Residual Gas Composition: The presence of residual gases in the vacuum chamber can interact with the deposited material, affecting the film's purity and properties. A high-quality vacuum minimizes contamination.
- Shadowing and Re-sputtering: These phenomena occur during deposition and can alter the film's microstructure. Shadowing happens when certain areas are blocked from deposition, while re-sputtering involves the removal of already deposited material by energetic particles.
-
Film Properties:
- Structural Defects: Defects such as voids, localized imperfections, and oxide bonds can degrade the film's performance. Minimizing these defects is critical for achieving desired optical, electrical, and mechanical properties.
- Roughness and Thickness: The roughness of the film surface and its thickness directly influence optical properties like transmission and reflection coefficients. Precise control of these parameters is essential for applications in optics and electronics.
-
Manufacturing Considerations:
- Quality Control: Ensuring consistent film properties requires rigorous quality control measures, including monitoring deposition parameters and inspecting the final product.
- Client Specifications: Thin films must meet specific requirements for their intended applications, such as optical coatings, semiconductor devices, or protective layers.
- Cost and Efficiency: Balancing production costs with efficiency is crucial for commercial viability. Optimizing deposition processes and minimizing material waste are key strategies.
-
Post-Deposition Processes:
- Ion Implantation and Additional Treatments: Post-deposition processes like ion implantation can modify the film's properties, such as hardness or electrical conductivity, to meet specific application needs.
By carefully controlling these factors, manufacturers can produce thin films with tailored properties for a wide range of applications, from electronics to optics and beyond.
Summary Table:
Category | Key Factors | Impact on Thin Films |
---|---|---|
Deposition Process | Substrate temperature, deposition rate, energy of incoming adatoms | Determines film adhesion, uniformity, and defect density |
Substrate Characteristics | Nature of substrate, surface mobility | Influences film adhesion, growth, and microstructure |
Environmental Conditions | Residual gas composition, shadowing, re-sputtering | Affects film purity, microstructure, and uniformity |
Film Properties | Structural defects, roughness, thickness | Impacts optical, electrical, and mechanical properties |
Manufacturing | Quality control, client specifications, cost and efficiency | Ensures consistent film properties and commercial viability |
Post-Deposition | Ion implantation, additional treatments | Modifies film properties to meet specific application needs |
Need tailored thin films for your application? Contact our experts today to optimize your production process!