The sputtering process is a complex physical phenomenon influenced by a variety of parameters that determine the efficiency, quality, and characteristics of the deposited film. Key factors include the mass of ions, angle of incidence, target atoms, incident ion energy, sputtering yield, chamber pressure, kinetic energy of emitted particles, type of power source, and operational variables like sputter current, voltage, and gas pressure. These parameters collectively affect the sputtering rate, deposition rate, and the overall quality of the coating. Understanding these factors is crucial for optimizing the sputtering process to achieve desired film properties and performance.
Key Points Explained:
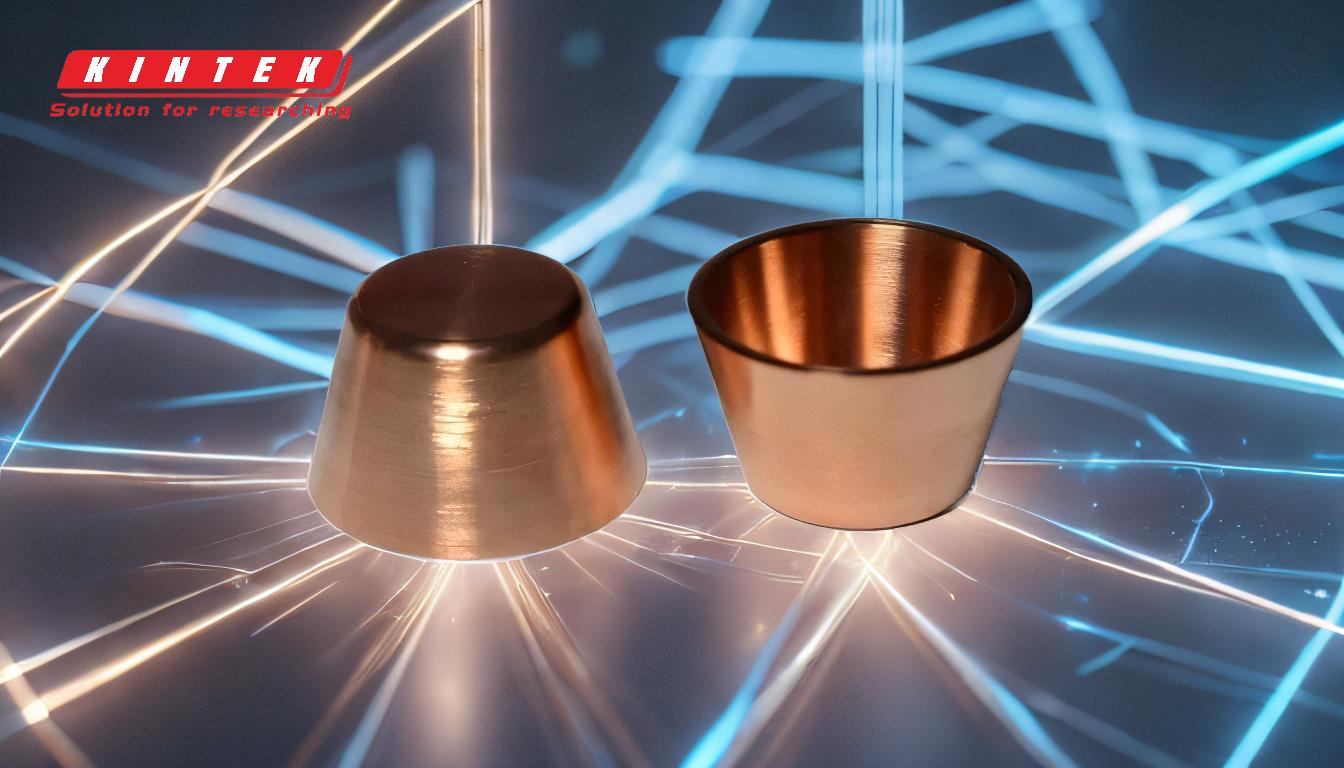
-
Mass of Ions and Target Atoms:
- The mass of the ions and the target atoms significantly influence the sputtering yield, which is the number of target atoms ejected per incident ion. Heavier ions tend to transfer more momentum to the target atoms, resulting in a higher sputtering yield. Similarly, the mass of the target atoms affects how easily they can be dislodged from the surface.
-
Angle of Incidence:
- The angle at which ions strike the target surface affects the sputtering yield. Typically, there is an optimal angle of incidence that maximizes the yield. Angles that are too shallow or too steep can reduce the efficiency of the sputtering process.
-
Incident Ion Energy:
- The energy of the incident ions is a critical factor. Higher energy ions can dislodge more target atoms, increasing the sputtering yield. However, excessively high energy can lead to undesirable effects such as deep implantation or damage to the target material.
-
Sputtering Yield:
- Defined as the number of target atoms ejected per incident ion, the sputtering yield is a direct measure of the efficiency of the sputtering process. It depends on the mass of the ions, the angle of incidence, and the energy of the incident ions.
-
Chamber Pressure:
- The pressure within the sputtering chamber affects the mean free path of the sputtered particles and the plasma density. Optimal pressure conditions can improve the uniformity and coverage of the deposited film. Too high or too low pressure can negatively impact the process.
-
Kinetic Energy of Emitted Particles:
- The kinetic energy of the particles ejected from the target determines their trajectory and how they deposit on the substrate. Higher kinetic energy can lead to better adhesion and film density but may also cause damage if too high.
-
Type of Power Source (DC or RF):
- The choice between DC (Direct Current) and RF (Radio Frequency) power sources affects the deposition rate, material compatibility, and cost. DC sputtering is typically used for conductive materials, while RF sputtering can be used for both conductive and insulating materials.
-
Operational Variables:
- Sputter Current and Voltage: These parameters control the energy and flux of the ions bombarding the target, directly affecting the sputtering rate and the quality of the deposited film.
- Pressure (Vacuum) in the Sample Chamber: Maintaining the correct vacuum level is crucial for controlling the sputtering process and ensuring consistent results.
- Distance from Target to Sample: The distance affects the deposition rate and the uniformity of the film. A shorter distance generally results in a higher deposition rate but may reduce uniformity.
- Sputter Gas: The type of gas used (e.g., Argon) can influence the sputtering process by affecting the plasma characteristics and the energy transfer to the target atoms.
- Target Thickness and Material: The thickness and material of the target affect the sputtering rate and the properties of the deposited film. Different materials have different sputtering yields and behaviors under ion bombardment.
- Sample Material(s): The material of the substrate can influence the adhesion and properties of the deposited film. Compatibility between the target material and the substrate is important for achieving desired film characteristics.
Understanding and optimizing these parameters is essential for achieving high-quality sputtered films with desired properties for various applications.
Summary Table:
Parameter | Impact on Sputtering Process |
---|---|
Mass of Ions and Target Atoms | Influences sputtering yield; heavier ions and lighter target atoms increase yield. |
Angle of Incidence | Optimal angle maximizes yield; too shallow or steep angles reduce efficiency. |
Incident Ion Energy | Higher energy increases yield but excessive energy can damage the target. |
Sputtering Yield | Measures efficiency; depends on ion mass, angle, and energy. |
Chamber Pressure | Affects particle trajectory and plasma density; optimal pressure improves film uniformity. |
Kinetic Energy of Particles | Higher energy improves adhesion but may cause damage if too high. |
Type of Power Source (DC/RF) | DC for conductive materials; RF for conductive and insulating materials. |
Operational Variables | Includes sputter current, voltage, gas pressure, target material, and substrate compatibility. |
Optimize your sputtering process for superior results—contact our experts today!