A ball mill is a versatile and widely used grinding machine that consists of several key components working together to achieve efficient material grinding. The main components include the cylindrical shell, grinding media, drive system, discharge system, and liners. Each component plays a critical role in the operation and performance of the ball mill. The cylindrical shell houses the grinding media and material, while the drive system ensures rotation. The discharge system allows the ground material to exit, and the liners protect the shell from wear. Together, these components ensure the ball mill operates effectively for grinding various materials.
Key Points Explained:
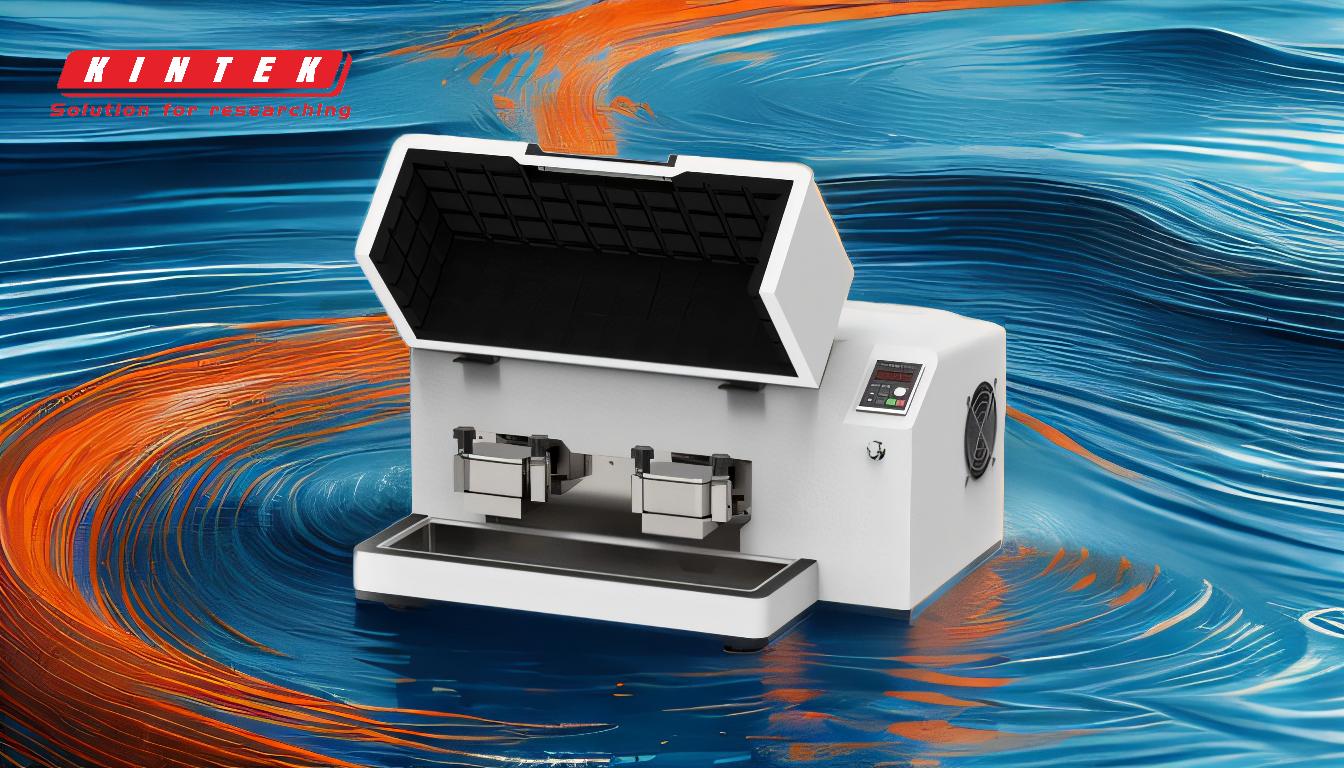
-
Cylindrical Shell
- The cylindrical shell is the primary structure of the ball mill, typically made of metal and designed to rotate about its axis.
- It can be either horizontal or slightly inclined, depending on the design and application.
- The shell is partially filled with grinding media and the material to be ground.
- Its rotation facilitates the tumbling and grinding action of the media, ensuring efficient material breakdown.
-
Grinding Media
- Grinding media are the balls or other shapes placed inside the cylindrical shell to perform the grinding action.
- These balls are typically made of materials such as steel, stainless steel, ceramic, or rubber, depending on the application and the material being ground.
- Larger balls are used to break down coarse materials, while smaller balls reduce void spaces and produce finer products.
- The choice of grinding media material and size significantly impacts the grinding efficiency and final product quality.
-
Drive System
- The drive system is responsible for rotating the cylindrical shell.
- It typically includes an electric motor, gearbox, and other mechanical components to ensure smooth and controlled rotation.
- The rotation speed can be adjusted to optimize grinding efficiency for different materials and desired particle sizes.
- A well-designed drive system ensures consistent operation and minimizes energy consumption.
-
Discharge System
- The discharge system allows the ground material to exit the ball mill after the grinding process is complete.
- It can include mechanisms such as grate plates, screens, or overflow systems, depending on the design.
- The discharge system ensures that only properly ground material exits the mill, while larger particles continue to be ground.
- Proper design of the discharge system is crucial for maintaining grinding efficiency and preventing blockages.
-
Liners
- Liners are protective layers installed on the inner surface of the cylindrical shell to prevent wear and tear caused by the grinding media and material.
- Common liner materials include manganese steel, rubber, or other abrasion-resistant materials.
- Liners not only protect the shell but also enhance the grinding efficiency by optimizing the movement of the grinding media.
- Regular inspection and replacement of liners are necessary to maintain the ball mill's performance and longevity.
-
Metallic Frame
- The metallic frame provides structural support for the entire ball mill assembly.
- It ensures stability during operation and supports the weight of the cylindrical shell, grinding media, and material.
- The frame is typically made of durable materials to withstand the stresses and vibrations generated during grinding.
- A robust frame design is essential for safe and reliable operation.
-
Material to be Ground
- The material to be ground is fed into the cylindrical shell along with the grinding media.
- The type and properties of the material (e.g., hardness, moisture content) influence the choice of grinding media and operating parameters.
- Proper feeding and distribution of the material within the mill are critical for achieving uniform grinding and desired particle size.
By understanding these key components, equipment and consumable purchasers can make informed decisions when selecting or maintaining a ball mill. Each component must be carefully chosen and maintained to ensure optimal performance and longevity of the equipment.
Summary Table:
Component | Role | Key Features |
---|---|---|
Cylindrical Shell | Houses grinding media and material; rotates for grinding action | Made of metal; horizontal or inclined; facilitates tumbling and grinding |
Grinding Media | Performs grinding action; breaks down material | Made of steel, ceramic, or rubber; size and material affect grinding efficiency |
Drive System | Rotates the cylindrical shell | Includes motor and gearbox; adjustable speed for optimal grinding |
Discharge System | Allows ground material to exit the mill | Uses grate plates, screens, or overflow systems; prevents blockages |
Liners | Protects shell from wear; enhances grinding efficiency | Made of manganese steel, rubber, or abrasion-resistant materials |
Metallic Frame | Provides structural support for the ball mill | Durable materials; ensures stability and safety during operation |
Material to be Ground | Fed into the mill for grinding | Influences choice of grinding media and operating parameters |
Ready to optimize your grinding process? Contact us today for expert advice on ball mill components and maintenance!