A mould is a crucial tool in manufacturing processes like injection molding, and its design directly impacts the quality and functionality of the final product. At its core, a mould consists of two main halves: the cavity and the core. The cavity forms the outer shape of the product, while the core shapes the inner or backside. These halves work together to create the desired part. Beyond these primary components, moulds may include additional features like runners, gates, and ejector pins to facilitate material flow and part removal. Understanding the main parts of a mould is essential for ensuring efficient production and high-quality outputs.
Key Points Explained:
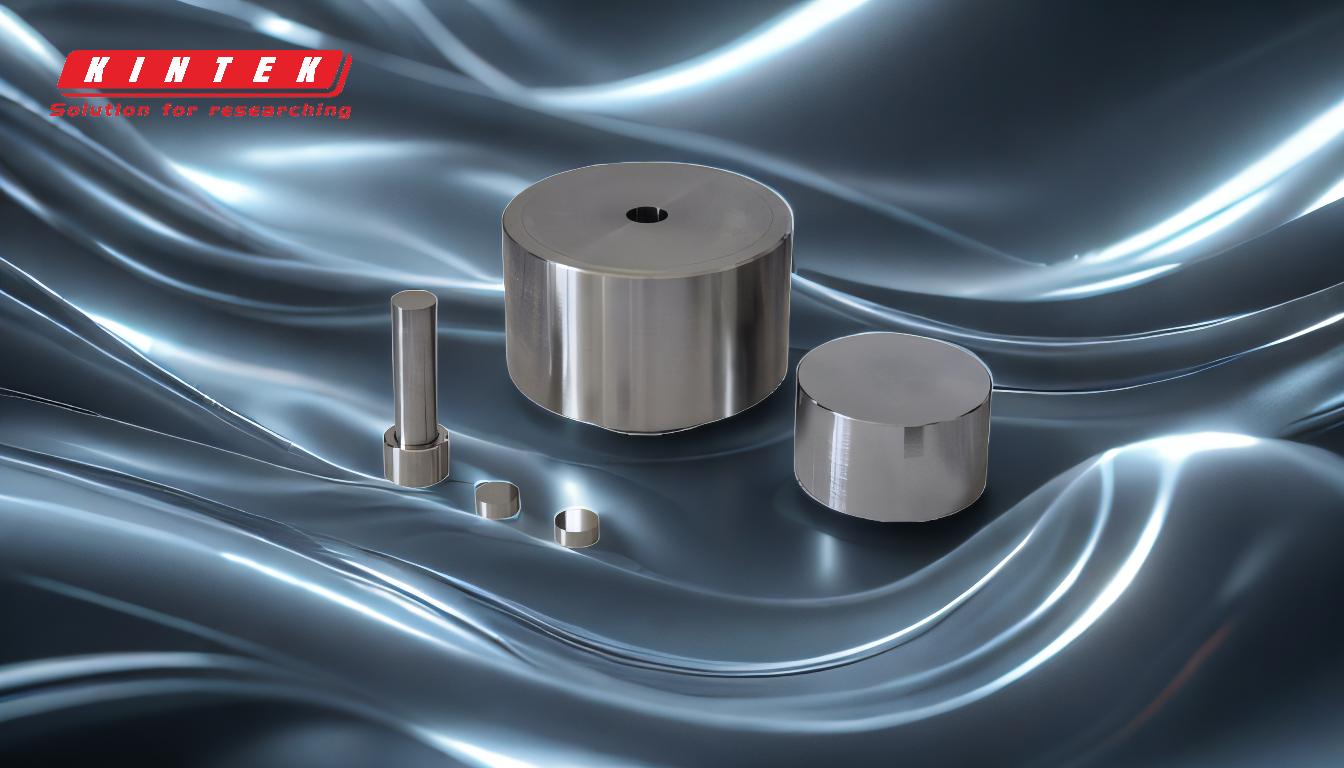
-
Cavity and Core:
- The cavity is the part of the mould that forms the outer surface of the product. It is typically the A-side, which is the cosmetic side with a better outward appearance.
- The core is the part that forms the inner or backside of the product, known as the B-side. It often includes functional features like ribs or bosses.
-
Metal Plates:
- Moulds are constructed from two metal plates that house the cavity and core. These plates are precision-machined to match the desired shape of the finished part.
- The plates must withstand high pressure and temperature during the molding process, so they are typically made from durable materials like steel or aluminum.
-
Cavities:
- Cavities are the hollow spaces within the mould plates where the material (e.g., plastic or rubber) is injected to form the product.
- The design of the cavities directly influences the final product's dimensions, surface finish, and structural integrity.
-
Runners and Gates:
- Runners are channels that guide the molten material from the injection molding machine nozzle to the cavities.
- Gates are the entry points where the material flows into the cavities. Their design affects the flow rate, cooling, and final appearance of the product.
-
Ejector System:
- After the material solidifies, the ejector system helps remove the finished part from the mould. This system typically includes ejector pins that push the part out of the cavity.
- Proper ejection is critical to avoid damaging the part or the mould.
-
Cooling System:
- Moulds often include cooling channels to regulate temperature and ensure uniform cooling of the material. This helps prevent defects like warping or sink marks.
- Efficient cooling is essential for maintaining cycle times and product quality.
-
Alignment and Support Features:
- Moulds may include guide pins and bushings to ensure precise alignment of the cavity and core halves.
- Support features like mold bases and clamping plates provide structural stability during the molding process.
By understanding these main parts of a mould, manufacturers can optimize their designs for better performance, durability, and product quality. Each component plays a vital role in the overall functionality of the mould, and their proper integration is key to successful production.
Summary Table:
Component | Function |
---|---|
Cavity | Forms the outer surface (A-side) of the product. |
Core | Shapes the inner or backside (B-side) of the product. |
Metal Plates | Houses cavity and core; made of durable materials like steel or aluminum. |
Runners and Gates | Channels and entry points for molten material flow. |
Ejector System | Removes the finished part from the mould using ejector pins. |
Cooling System | Regulates temperature to ensure uniform cooling and prevent defects. |
Alignment Features | Ensures precise alignment of cavity and core halves. |
Optimize your mould design for better production efficiency—contact our experts today!