Hydraulic pump failure can occur due to a variety of reasons, often stemming from improper maintenance, contamination, or operational issues. Common causes include fluid contamination, overheating, cavitation, aeration, and misalignment. Contaminants like dirt, water, or metal particles can damage internal components, while overheating can degrade the hydraulic fluid and seals. Cavitation and aeration lead to air bubbles forming in the fluid, causing damage to the pump's internal surfaces. Misalignment of the pump with the drive shaft can result in excessive wear and tear. Proper maintenance, regular inspections, and using high-quality fluids are essential to prevent these issues and ensure the longevity of hydraulic pumps.
Key Points Explained:
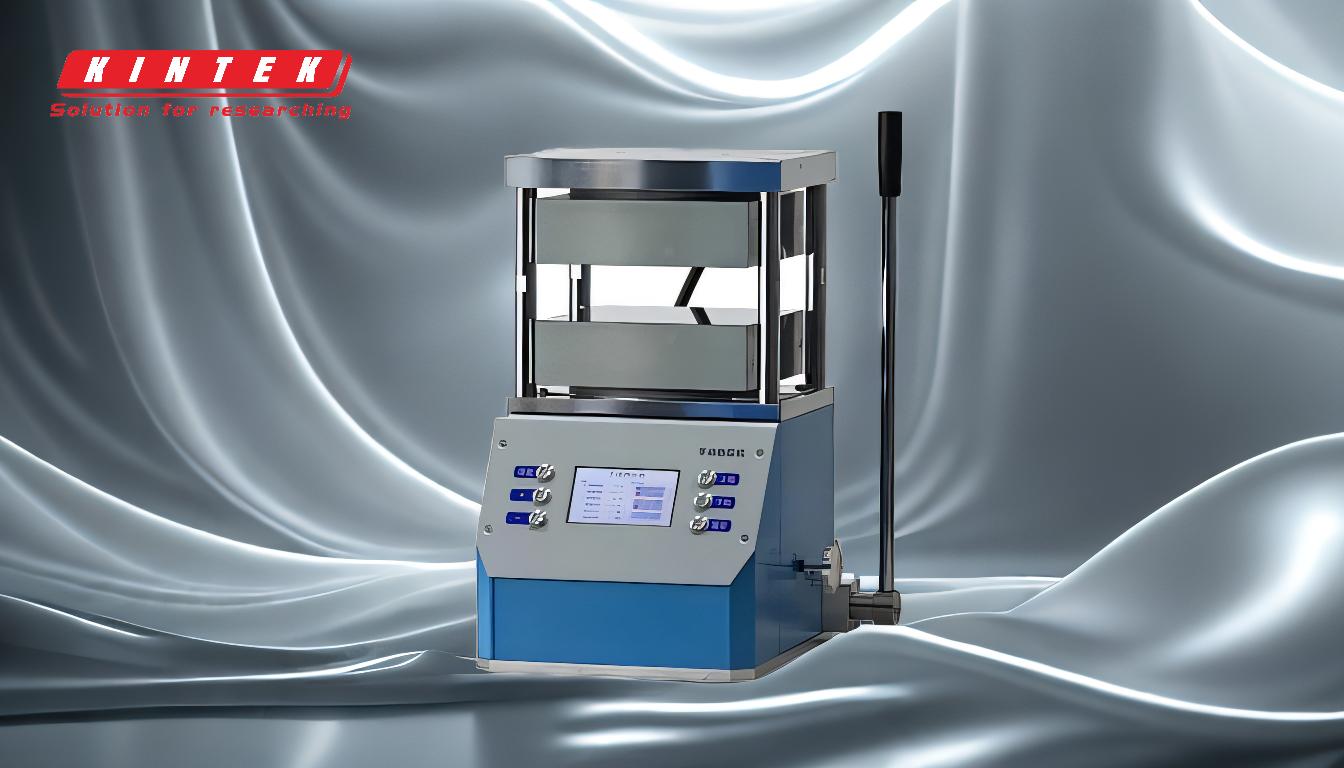
-
Fluid Contamination:
- Contaminants such as dirt, water, or metal particles can enter the hydraulic system and cause significant damage to the pump's internal components. These particles can scratch or wear down the surfaces of the pump, leading to reduced efficiency and eventual failure.
- Prevention: Use high-quality filters and regularly check and replace them. Ensure that the hydraulic fluid is clean and free from contaminants. Implement a strict maintenance schedule to monitor and clean the system.
-
Overheating:
- Excessive heat can degrade the hydraulic fluid, causing it to lose its lubricating properties. This can lead to increased friction and wear on the pump's internal parts. Overheating can also cause seals and gaskets to fail, leading to leaks.
- Prevention: Ensure that the hydraulic system has adequate cooling. Monitor the temperature of the hydraulic fluid and address any issues that cause overheating, such as blocked cooling lines or excessive load on the system.
-
Cavitation:
- Cavitation occurs when the hydraulic fluid cannot fill the pump's inlet fast enough, creating a vacuum that forms air bubbles. When these bubbles collapse, they create shock waves that can damage the pump's internal surfaces.
- Prevention: Ensure that the pump is properly sized for the application and that the inlet lines are not restricted. Use a reservoir that is large enough to supply the pump with an adequate amount of fluid.
-
Aeration:
- Aeration happens when air enters the hydraulic fluid, usually through leaks in the suction line or low fluid levels in the reservoir. Air bubbles in the fluid can cause the pump to operate less efficiently and lead to damage over time.
- Prevention: Regularly check for leaks in the suction line and ensure that the fluid level in the reservoir is maintained. Use a reservoir design that minimizes the chance of air entering the system.
-
Misalignment:
- Misalignment between the pump and the drive shaft can cause excessive wear and tear on the pump's components. This misalignment can be due to improper installation or shifting over time.
- Prevention: Ensure that the pump and drive shaft are properly aligned during installation. Regularly check the alignment and make adjustments as necessary. Use flexible couplings to accommodate minor misalignments.
-
Improper Maintenance:
- Neglecting regular maintenance can lead to a buildup of issues that eventually cause pump failure. This includes not changing the hydraulic fluid, ignoring leaks, or failing to replace worn-out components.
- Prevention: Implement a regular maintenance schedule that includes checking and replacing the hydraulic fluid, inspecting for leaks, and replacing worn-out parts. Keep detailed records of maintenance activities to track the condition of the pump over time.
By addressing these key points, you can significantly reduce the risk of hydraulic pump failure and ensure the reliable operation of your hydraulic system.
Summary Table:
Cause | Description | Prevention |
---|---|---|
Fluid Contamination | Dirt, water, or metal particles damage internal components. | Use high-quality filters, clean fluid, and implement strict maintenance schedules. |
Overheating | Degrades hydraulic fluid and seals, leading to leaks and wear. | Ensure adequate cooling, monitor fluid temperature, and address overheating causes. |
Cavitation | Air bubbles form and collapse, damaging pump surfaces. | Properly size the pump, avoid restricted inlet lines, and use a sufficiently large reservoir. |
Aeration | Air enters the fluid, reducing efficiency and causing damage. | Check for suction line leaks, maintain fluid levels, and use air-minimizing reservoir designs. |
Misalignment | Pump and drive shaft misalignment causes excessive wear. | Ensure proper alignment during installation and use flexible couplings for minor adjustments. |
Improper Maintenance | Neglecting maintenance leads to fluid degradation and component wear. | Implement regular maintenance schedules, replace worn parts, and keep detailed records. |
Protect your hydraulic system from failure—contact our experts today for tailored solutions and support!