The operating procedures for a ball mill involve a series of steps to ensure efficient and safe grinding of materials. These steps include preparation, loading, operation, monitoring, and maintenance. The process begins with inspecting the equipment and materials, followed by loading the grinding media and material into the mill. During operation, the mill is monitored for performance and safety, and adjustments are made as needed. Post-operation, the mill is cleaned and maintained to ensure longevity and reliability. Below is a detailed breakdown of the key points in the operating procedures.
Key Points Explained:
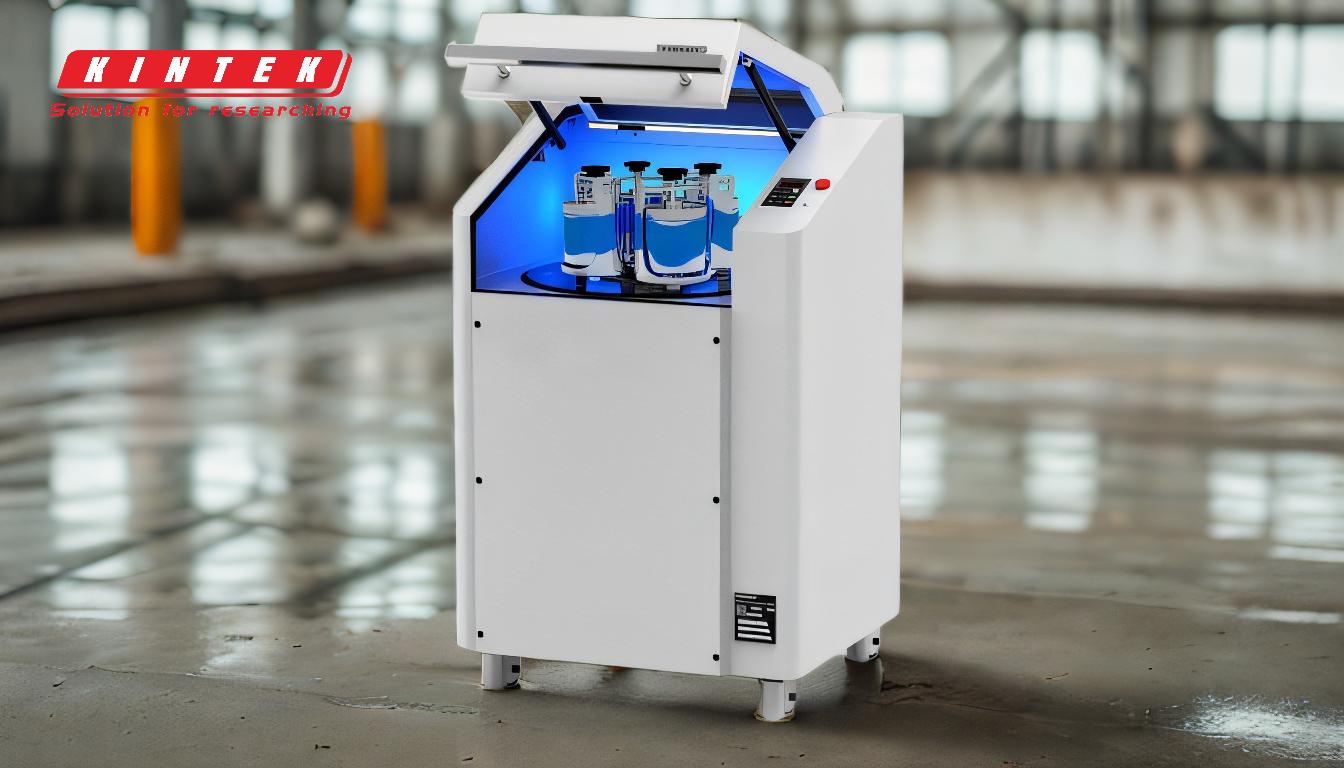
-
Preparation and Inspection
- Inspect the Ball Mill: Before starting, ensure the ball mill is in good working condition. Check for any visible damage, loose parts, or obstructions in the cylinder.
- Verify Material and Grinding Media: Confirm that the material to be ground and the grinding media (steel balls or rods) are suitable for the process. Ensure the grinding media is clean and free of contaminants.
- Safety Checks: Ensure all safety guards and emergency stop mechanisms are in place and functional.
-
Loading the Ball Mill
- Add Grinding Media: Load the appropriate amount of grinding media into the cylinder. The quantity and size of the media depend on the material being ground and the desired fineness.
- Add Material to be Ground: Introduce the material into the mill. Avoid overloading, as this can reduce grinding efficiency and damage the mill.
- Secure the Mill: Close and secure the mill's lid or access point to prevent spillage or accidents during operation.
-
Operation
- Start the Mill: Begin rotating the cylinder at the recommended speed. The speed should be optimized for the material and grinding media being used.
- Monitor the Process: Continuously observe the mill's performance. Listen for unusual noises, which may indicate issues such as media imbalance or mechanical problems.
- Adjust as Needed: If the grinding process is not achieving the desired results, adjust parameters such as rotation speed, grinding media size, or material load.
-
Monitoring and Safety
- Check Temperature: Monitor the temperature of the mill to prevent overheating, which can damage the equipment or degrade the material.
- Vibration and Noise: Excessive vibration or noise may indicate mechanical issues. Stop the mill immediately if such signs are detected and inspect the equipment.
- Safety Protocols: Always follow safety protocols, such as wearing protective gear and avoiding direct contact with moving parts.
-
Post-Operation Procedures
- Stop the Mill: Once grinding is complete, stop the mill and allow it to come to a complete stop before opening.
- Unload the Material: Carefully remove the ground material and grinding media. Use appropriate tools to avoid injury.
- Clean the Mill: Clean the cylinder and grinding media to remove any residual material. This prevents contamination in future batches.
-
Maintenance
- Inspect for Wear: Regularly inspect the mill and grinding media for signs of wear or damage. Replace worn parts as needed to maintain efficiency.
- Lubricate Moving Parts: Apply lubrication to moving parts to reduce friction and extend the life of the equipment.
- Record Maintenance: Keep a log of maintenance activities to track the mill's condition and performance over time.
By following these operating procedures, you can ensure the ball mill operates efficiently, safely, and reliably, delivering consistent grinding results while minimizing downtime and maintenance costs.
Summary Table:
Step | Key Actions |
---|---|
Preparation | Inspect equipment, verify materials, and perform safety checks. |
Loading | Add grinding media and material, secure the mill. |
Operation | Start the mill, monitor performance, and adjust parameters as needed. |
Monitoring & Safety | Check temperature, vibration, and noise; follow safety protocols. |
Post-Operation | Stop the mill, unload material, and clean the equipment. |
Maintenance | Inspect for wear, lubricate moving parts, and record maintenance activities. |
Optimize your ball mill operations—contact our experts today for personalized guidance!