Pyrolysis is a thermal decomposition process that occurs in the absence of oxygen, converting organic materials into gas, liquid, and solid products. The operational conditions of pyrolysis are critical in determining the efficiency, product distribution, and quality of the outputs. Key factors include temperature, pressure, residence time, heating rate, feedstock composition, and particle size. These variables influence the thermal decomposition pathways, product yields, and the properties of the resulting gas, liquid, and solid fractions. Understanding and optimizing these conditions is essential for achieving desired outcomes in industrial and environmental applications.
Key Points Explained:
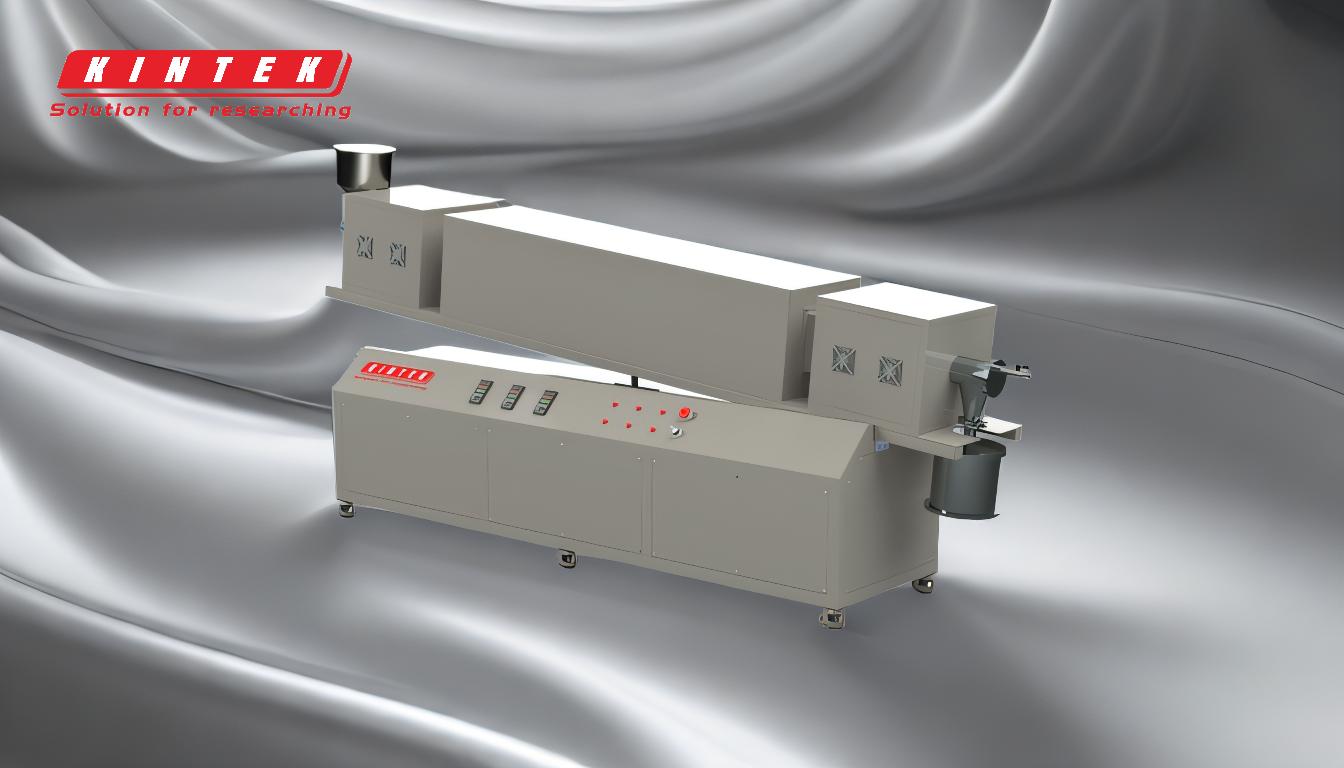
-
Temperature:
- Role: Temperature is the most critical factor in pyrolysis, as it directly influences the thermal decomposition of organic materials.
-
Impact:
- High Temperatures (above 700°C): Favor the production of non-condensable gases (e.g., hydrogen, methane) due to the complete breakdown of high-molecular-weight compounds.
- Moderate Temperatures (450–550°C): Promote the formation of liquid organic products (bio-oil), which are valuable for fuel and chemical production.
- Low Temperatures (below 400°C): Yield solid residues like char or coke, which are useful for applications such as soil amendment or carbon sequestration.
- Example: For biomass, temperatures between 450°C and 550°C are optimal for maximizing bio-oil yield.
-
Pressure:
- Role: Pressure affects the phase behavior and reaction kinetics during pyrolysis.
-
Impact:
- Increased Pressure: Enhances secondary reactions like condensation and polymerization, leading to higher char yields.
- Reduced Pressure: Favors the production of gaseous and liquid products by minimizing secondary reactions.
- Example: In vacuum pyrolysis, lower pressures are used to maximize liquid yields and reduce char formation.
-
Residence Time:
- Role: Residence time refers to the duration that the feedstock remains in the pyrolysis reactor.
-
Impact:
- Long Residence Times: Allow for more complete thermal conversion, increasing gas yields and reducing liquid and solid outputs.
- Short Residence Times: Favor the production of liquid products by minimizing secondary cracking reactions.
- Example: Fast pyrolysis processes use short residence times (less than 2 seconds) to maximize bio-oil production.
-
Heating Rate:
- Role: The rate at which the feedstock is heated influences the decomposition pathways and product distribution.
-
Impact:
- High Heating Rates: Promote rapid thermal decomposition, favoring the production of liquid and gaseous products.
- Low Heating Rates: Encourage char formation through slower, more controlled decomposition.
- Example: Fast pyrolysis employs heating rates of 100–1,000°C/s to maximize bio-oil yields.
-
Feedstock Composition:
- Role: The chemical and physical properties of the feedstock (e.g., moisture content, volatile matter, fixed carbon) significantly influence pyrolysis outcomes.
-
Impact:
- High Moisture Content: Reduces the efficiency of pyrolysis by requiring additional energy for evaporation.
- High Volatile Matter: Increases the yield of liquid and gaseous products.
- High Fixed Carbon: Favors the production of solid residues like char.
- Example: Biomass with high cellulose and hemicellulose content produces more bio-oil, while lignin-rich feedstocks yield more char.
-
Particle Size:
- Role: The size of the feedstock particles affects heat transfer and reaction kinetics.
-
Impact:
- Smaller Particles: Enhance heat transfer, leading to faster and more uniform thermal decomposition and higher liquid yields.
- Larger Particles: Result in slower heating and increased char formation due to incomplete decomposition.
- Example: In fast pyrolysis, feedstocks are typically ground to small particle sizes (less than 2 mm) to optimize heat transfer.
-
Atmosphere:
- Role: The gaseous environment in the pyrolysis reactor can influence the reaction pathways.
-
Impact:
- Inert Atmosphere (e.g., nitrogen): Prevents oxidation and ensures pure thermal decomposition.
- Reactive Atmosphere (e.g., steam): Can enhance gas yields and modify product composition through secondary reactions.
- Example: Steam pyrolysis is used to increase hydrogen production from biomass.
-
Feed Rate:
- Role: The rate at which feedstock is introduced into the reactor affects the overall process efficiency and product distribution.
-
Impact:
- High Feed Rates: Can lead to incomplete decomposition and reduced product quality.
- Optimal Feed Rates: Ensure consistent thermal conversion and maximize product yields.
- Example: Continuous pyrolysis systems require precise feed rate control to maintain stable operating conditions.
-
Secondary Reactions:
- Role: Secondary reactions (e.g., cracking, polymerization) occur after the initial thermal decomposition and influence the final product composition.
-
Impact:
- Cracking: Breaks down larger molecules into smaller ones, increasing gas yields.
- Polymerization: Forms larger molecules, leading to char and tar formation.
- Example: In fast pyrolysis, minimizing secondary cracking reactions is crucial for maximizing bio-oil yields.
-
Environmental and Economic Considerations:
- Role: Operational conditions must also consider environmental impacts (e.g., greenhouse gas emissions) and economic feasibility.
-
Impact:
- Energy Efficiency: Optimizing temperature, pressure, and residence time can reduce energy consumption and operating costs.
- Emissions Control: Proper management of process conditions can minimize greenhouse gas emissions and other pollutants.
- Example: Integrating waste heat recovery systems can improve the overall energy efficiency of pyrolysis plants.
By carefully controlling these operational conditions, pyrolysis processes can be tailored to produce specific products (gas, liquid, or solid) with desired properties, making it a versatile and valuable technology for waste management, renewable energy, and chemical production.
Summary Table:
Factor | Role | Impact | Example |
---|---|---|---|
Temperature | Most critical factor; influences thermal decomposition. | High temps favor gas, moderate temps favor liquid, low temps favor solid products. | 450–550°C optimal for bio-oil from biomass. |
Pressure | Affects phase behavior and reaction kinetics. | Increased pressure enhances char yields; reduced pressure favors gas and liquid products. | Vacuum pyrolysis maximizes liquid yields. |
Residence Time | Duration feedstock remains in the reactor. | Long times increase gas yields; short times favor liquid production. | Fast pyrolysis uses <2 seconds for bio-oil. |
Heating Rate | Rate of feedstock heating influences decomposition pathways. | High rates favor liquid and gas; low rates encourage char formation. | Fast pyrolysis uses 100–1,000°C/s for bio-oil. |
Feedstock Composition | Chemical/physical properties affect outcomes. | High volatile matter increases liquid/gas; high fixed carbon favors char. | Cellulose-rich biomass yields more bio-oil. |
Particle Size | Affects heat transfer and reaction kinetics. | Smaller particles enhance heat transfer and liquid yields; larger particles increase char formation. | Fast pyrolysis uses <2 mm particles. |
Atmosphere | Gaseous environment influences reaction pathways. | Inert atmospheres prevent oxidation; reactive atmospheres (e.g., steam) enhance gas yields. | Steam pyrolysis increases hydrogen production. |
Feed Rate | Rate of feedstock introduction affects efficiency and product quality. | High rates reduce quality; optimal rates ensure consistent conversion. | Continuous systems require precise feed rate control. |
Secondary Reactions | Occur post-decomposition; influence final product composition. | Cracking increases gas; polymerization leads to char/tar. | Minimizing cracking maximizes bio-oil in fast pyrolysis. |
Environmental/Economic | Considers emissions and feasibility. | Optimized conditions reduce energy use and emissions; waste heat recovery improves efficiency. | Integrating heat recovery systems boosts plant efficiency. |
Ready to optimize your pyrolysis process? Contact our experts today for tailored solutions!