Ball mill design is a critical aspect of achieving optimal grinding performance, and it involves several key parameters that influence productivity and efficiency. These parameters include drum diameter, the ratio of drum diameter to length (L:D ratio), physical-chemical properties of the feed material, ball filling and sizes, armor surface shape, rotation speed, milling fineness, and timely removal of ground product. Additionally, factors such as the size and type of grinding medium, the filling ratio of the mill, residence time, and solids loading play significant roles in determining the effectiveness of the grinding process. Understanding and optimizing these parameters are essential for designing a ball mill that meets specific grinding requirements.
Key Points Explained:
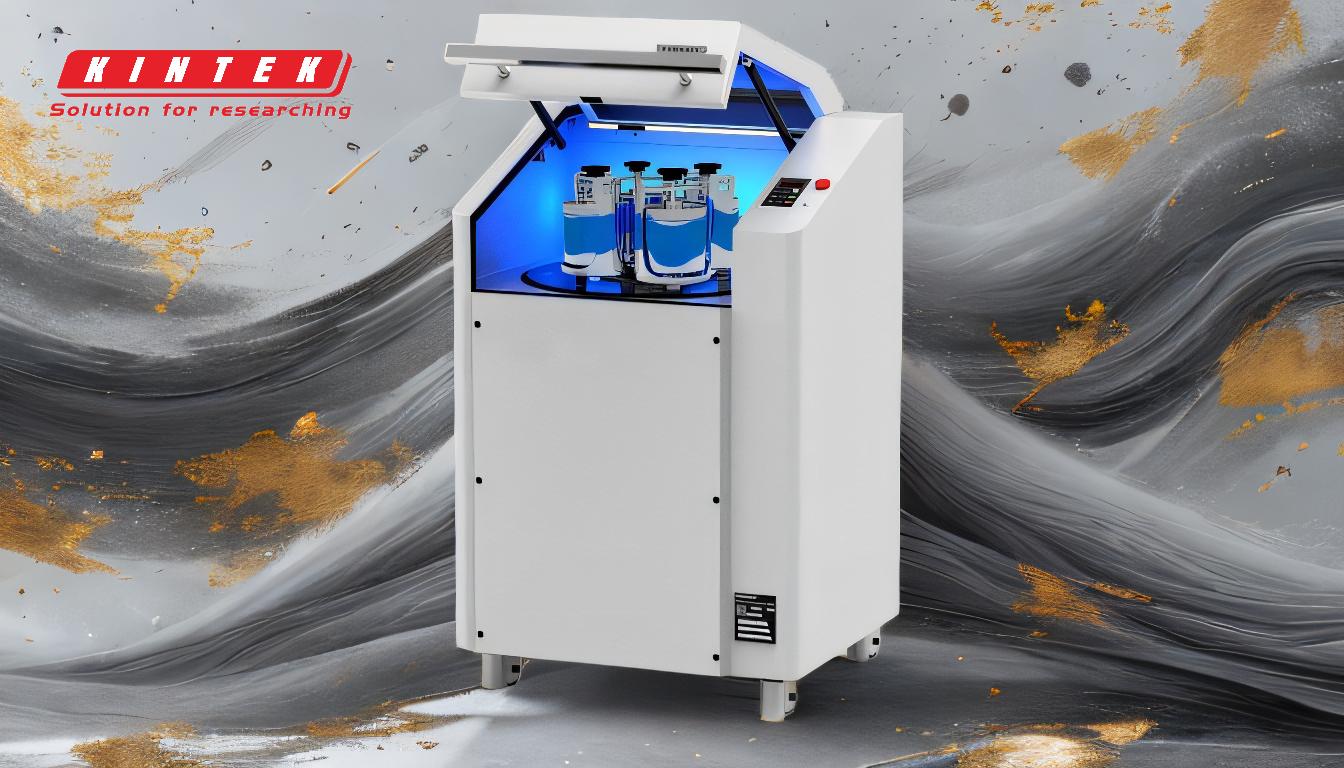
-
Drum Diameter and Length-to-Diameter Ratio (L:D Ratio):
- The drum diameter is a fundamental parameter in ball mill design, as it directly influences the mill's capacity and grinding efficiency. A larger drum diameter generally allows for greater throughput.
- The L:D ratio is crucial for determining the optimal grinding conditions. Research suggests that an L:D ratio of 1.56–1.64 is ideal for achieving efficient grinding. This ratio ensures a balance between the grinding surface area and the volume of material being processed.
-
Physical-Chemical Properties of Feed Material:
- The nature of the material being ground, including its hardness, density, and chemical composition, significantly affects the grinding process. For example, harder materials may require larger or denser grinding media to achieve the desired fineness.
- The feed material's properties also influence the choice of grinding media and the mill's operating conditions.
-
Ball Filling and Sizes:
- The ball filling ratio (the percentage of the mill volume filled with grinding media) is a critical factor in determining grinding efficiency. Overfilling or underfilling the mill can lead to suboptimal grinding performance.
- The size of the grinding balls is also important. Larger balls are more effective for coarse grinding, while smaller balls are better suited for fine grinding. The selection of ball sizes should be based on the desired fineness of the ground product.
-
Armor Surface Shape:
- The shape and design of the mill's internal armor (liners) can affect the grinding process by influencing the movement of the grinding media and the material being ground. Smooth liners may promote a cascading motion, while lifter bars can enhance the impact and grinding action.
-
Rotation Speed:
- The rotation speed of the mill is a key parameter that determines the motion of the grinding media and the material inside the mill. The optimal rotation speed depends on the mill's diameter and the desired grinding action. Too high a speed can lead to excessive wear, while too low a speed may result in insufficient grinding.
-
Milling Fineness and Timely Removal of Ground Product:
- The desired fineness of the ground product is a critical factor in ball mill design. Achieving the required fineness often involves adjusting parameters such as ball size, rotation speed, and residence time.
- Timely removal of the ground product is essential to prevent over-grinding and to maintain consistent product quality. This can be achieved through proper design of the discharge system.
-
Residence Time and Feed Rate:
- The residence time of the material in the mill chamber is an important factor that influences the degree of grinding. Longer residence times generally result in finer grinding, but they can also lead to increased energy consumption.
- The feed rate and the level of material in the mill must be carefully controlled to ensure consistent grinding performance. Overloading the mill can reduce grinding efficiency, while underloading can lead to excessive wear of the grinding media.
-
Solids Loading:
- The solids loading (the proportion of solids in the slurry) is another critical parameter in ball mill design, particularly for wet grinding operations. Optimal solids loading ensures efficient grinding while minimizing energy consumption.
-
Independent Variables in Dry Grinding:
- In dry grinding operations, the main independent variables include mill diameter, mill speed, media size, solids loading, and residence time. These variables must be carefully controlled to achieve the desired grinding performance.
-
Grinding Medium:
- The type and size of the grinding medium (balls) are critical factors in ball mill design. The grinding medium's density, hardness, and size distribution must be selected based on the material being ground and the desired fineness of the product.
By carefully considering and optimizing these parameters, engineers can design ball mills that achieve the desired grinding performance while minimizing energy consumption and wear. Each parameter plays a unique role in the grinding process, and their interactions must be thoroughly understood to ensure optimal mill design.
Summary Table:
Parameter | Description | Optimal Value/Consideration |
---|---|---|
Drum Diameter | Influences mill capacity and grinding efficiency. | Larger diameter increases throughput. |
L:D Ratio | Balances grinding surface area and material volume. | 1.56–1.64 for efficient grinding. |
Feed Material Properties | Hardness, density, and chemical composition affect grinding. | Harder materials require denser grinding media. |
Ball Filling Ratio | Percentage of mill volume filled with grinding media. | Avoid overfilling or underfilling. |
Ball Sizes | Larger balls for coarse grinding, smaller for fine grinding. | Match ball size to desired fineness. |
Armor Surface Shape | Influences grinding media and material movement. | Smooth liners or lifter bars for specific actions. |
Rotation Speed | Determines grinding media motion and grinding action. | Adjust based on mill diameter and desired output. |
Milling Fineness | Desired fineness of the ground product. | Adjust ball size, speed, and residence time. |
Residence Time | Time material spends in the mill chamber. | Longer time for finer grinding, but higher energy. |
Solids Loading | Proportion of solids in the slurry (wet grinding). | Optimal loading minimizes energy use. |
Grinding Medium | Type and size of grinding balls. | Match density and hardness to material. |
Optimize your ball mill design for maximum efficiency—contact our experts today!