A ball mill operates on the principles of impact and attrition to grind materials into fine particles. It consists of a horizontally-mounted rotating cylinder filled with grinding media, such as steel balls or rods. As the cylinder rotates, the balls are lifted and then dropped onto the material, exerting impact forces that break it into smaller pieces. Simultaneously, the balls rub against each other and the material, causing attrition, which further reduces the particle size. This combination of mechanical forces ensures efficient grinding, making ball mills widely used in industries for material processing and refinement.
Key Points Explained:
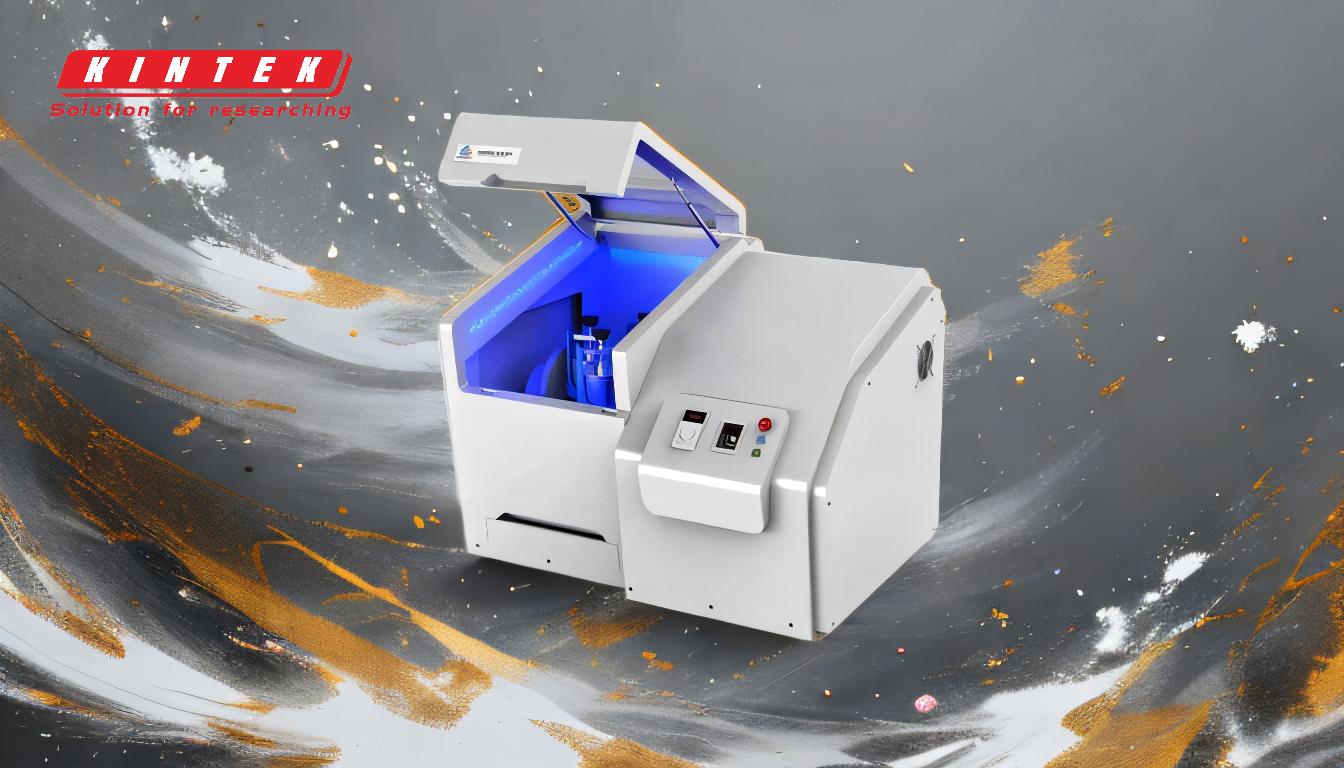
-
Principle of Operation: Impact and Attrition
- Impact: The grinding media (balls or rods) are lifted by the rotating cylinder and then dropped onto the material. The force of the impact breaks the material into smaller pieces.
- Attrition: The grinding media rub against each other and the material, causing friction that further reduces the particle size. This process is particularly effective for fine grinding.
-
Structure of a Ball Mill
- Rotating Cylinder: The core component of a ball mill is a horizontally-mounted cylinder that rotates along its longitudinal axis. This rotation is responsible for lifting and dropping the grinding media.
- Grinding Media: Steel balls or rods are used as grinding media. The size and material of the media can vary depending on the application and the material being ground.
- Metallic Frame: The cylinder is mounted on a sturdy metallic frame to ensure stability during operation.
-
Mechanism of Grinding
- Coarse Grinding: Larger balls are used to break down coarse feed materials. The impact force from these balls is sufficient to fracture larger particles.
- Fine Grinding: Smaller balls are used to fill void spaces and ensure that finer particles are produced. The attrition process is more prominent here, as the smaller balls provide a greater surface area for friction.
-
Applications of Ball Mills
- Material Processing: Ball mills are used in various industries, including mining, ceramics, and pharmaceuticals, for grinding and blending materials.
- Versatility: They can handle a wide range of materials, from hard and brittle substances to softer, more pliable ones.
-
Advantages of Ball Mills
- Efficiency: The combination of impact and attrition ensures efficient grinding, reducing the material to the desired particle size.
- Scalability: Ball mills can be scaled up or down depending on the volume of material to be processed.
- Consistency: The grinding process is consistent, producing uniform particle sizes.
-
Considerations for Equipment Purchasers
- Material Compatibility: Ensure that the grinding media and cylinder material are compatible with the material to be ground to avoid contamination or wear.
- Size and Capacity: Choose a ball mill with the appropriate size and capacity for your specific application.
- Operational Costs: Consider the energy consumption and maintenance requirements when selecting a ball mill.
By understanding these principles and components, equipment purchasers can make informed decisions when selecting a ball mill for their specific needs. The combination of impact and attrition, along with the structural design, ensures that ball mills are effective and versatile tools for material processing.
Summary Table:
Aspect | Details |
---|---|
Principle of Operation | Combines impact (forceful breaking) and attrition (friction-based grinding). |
Structure | Rotating cylinder, grinding media (steel balls/rods), and metallic frame. |
Mechanism | Coarse grinding (larger balls) and fine grinding (smaller balls). |
Applications | Mining, ceramics, pharmaceuticals, and more. |
Advantages | High efficiency, scalability, and consistent particle size. |
Considerations | Material compatibility, size/capacity, and operational costs. |
Ready to optimize your material processing? Contact our experts today to find the perfect ball mill for your needs!