Magnetron sputtering is a widely used technique in thin-film deposition, offering advantages such as high deposition rates, precise control, and versatility. However, it also faces several challenges, including limitations in effective coating area, poor bonding strength, high system costs, and issues with deposition uniformity and substrate heating. These problems can affect the quality and applicability of the films produced, particularly for large-scale or temperature-sensitive applications. Despite these challenges, ongoing research and advancements continue to improve the technique, making it suitable for a wide range of applications in microelectronics, semiconductors, and decorative coatings.
Key Points Explained:
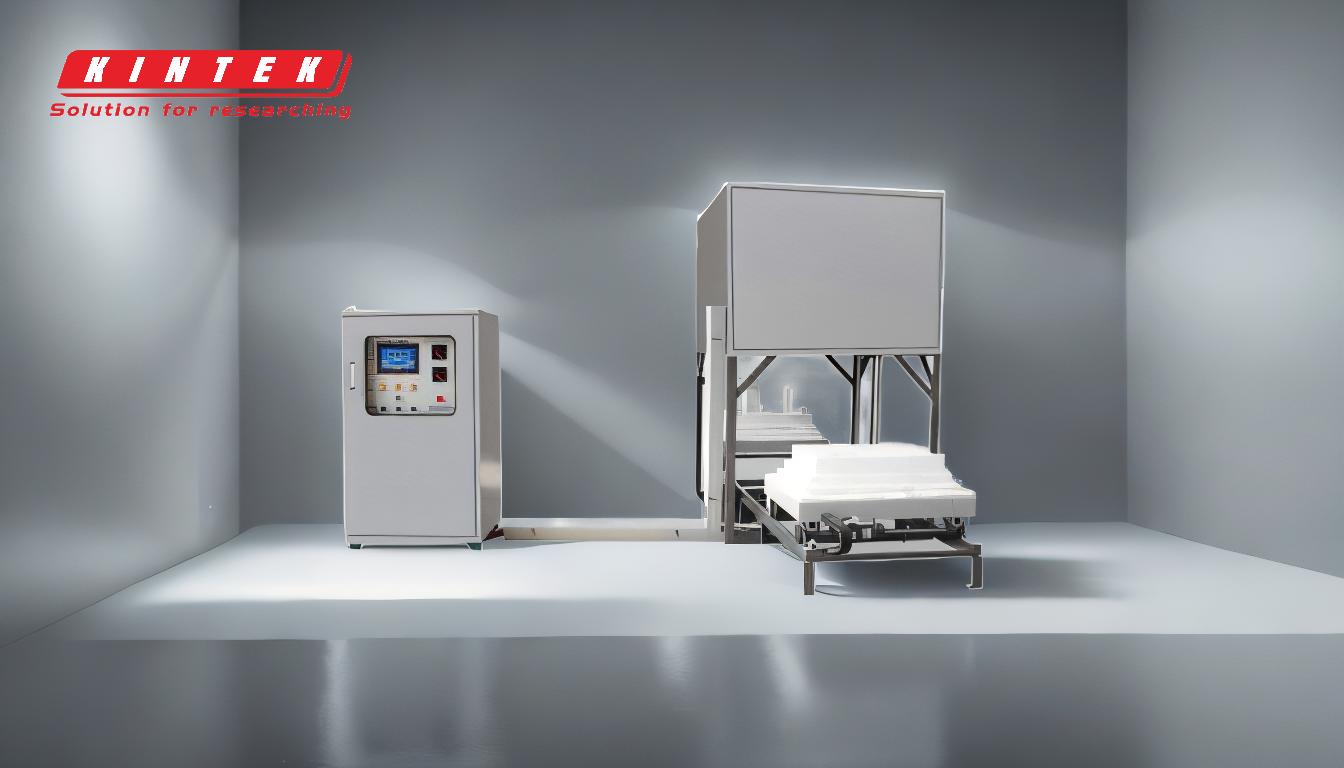
-
Limited Effective Coating Area:
- The effective coating area in balanced magnetron sputtering is relatively short, restricting the geometric size of workpieces that can be plated. The plasma concentration decreases rapidly beyond 60 mm from the target surface, which limits the placement of workpieces. This can be a significant drawback for large-scale applications or when coating complex geometries.
-
Poor Bonding Strength and Film Quality:
- The energy of the flying target particles in magnetron sputtering is often low, leading to poor bonding strength between the film and the substrate. This can result in the formation of porous and rough columnar structures, which may compromise the mechanical and functional properties of the film. Raising the workpiece temperature can improve film properties, but this approach is not feasible for materials that cannot withstand high temperatures.
-
High System Cost and Complexity:
- Magnetron sputtering systems are generally expensive and complex to operate. The high initial investment and maintenance costs can be a barrier for smaller-scale operations or research facilities. Additionally, the complexity of the system requires skilled personnel for operation and troubleshooting.
-
Substrate Heating Issues:
- The process can cause significant heating of the substrate due to the energetic target material. This can be problematic for temperature-sensitive materials or applications where precise temperature control is required. Substrate heating can also lead to thermal stress and deformation, affecting the quality of the deposited film.
-
Deposition Rate and Directionality:
- While magnetron sputtering offers high deposition rates for many materials, it can be less effective for dielectrics, which may have lower deposition rates. Additionally, the technique often suffers from low directionality, which can be improved with system geometry but remains a challenge for achieving uniform coatings on complex or three-dimensional substrates.
-
Homogeneity and Large-Surface Applicability:
- Achieving homogeneity in the deposited film can be challenging, especially for large surfaces. The technique may struggle to provide uniform thickness and composition across the entire substrate, which is critical for applications requiring consistent film properties. This limitation makes magnetron sputtering less suitable for certain large-scale or high-precision applications.
-
High-Temperature Post-Coating Processes:
- Some applications require high-temperature processes after coating to enhance film properties, such as adhesion and density. However, these high-temperature treatments can be disadvantageous for materials that are sensitive to heat or for applications where thermal budget is a concern.
-
Advantages and Ongoing Improvements:
- Despite these challenges, magnetron sputtering remains a highly efficient and versatile technique. It offers high deposition rates, thorough material coverage, high purity of films, and the ability to operate at low temperatures. Ongoing research and technological advancements continue to address many of the limitations, making it a valuable tool for thin-film preparation in various industries.
In summary, while magnetron sputtering is a powerful and versatile technique for thin-film deposition, it is not without its challenges. Understanding these limitations is crucial for optimizing the process and expanding its applicability to a wider range of materials and applications.
Summary Table:
Challenge | Description |
---|---|
Limited Effective Coating Area | Plasma concentration decreases beyond 60 mm, restricting large-scale applications. |
Poor Bonding Strength | Low energy of target particles leads to porous, rough films with weak adhesion. |
High System Cost and Complexity | Expensive initial investment and maintenance; requires skilled personnel. |
Substrate Heating Issues | Energetic target material causes heating, problematic for temperature-sensitive materials. |
Deposition Rate and Directionality | Low directionality and slower rates for dielectrics; challenges for complex substrates. |
Homogeneity and Large-Surface Applicability | Difficulty achieving uniform thickness and composition on large surfaces. |
High-Temperature Post-Coating Processes | Heat treatments can damage temperature-sensitive materials. |
Ongoing Improvements | Research continues to address limitations, enhancing versatility and efficiency. |
Discover how to overcome magnetron sputtering challenges and optimize your thin-film processes—contact our experts today!