Methane pyrolysis, while a promising technology for producing hydrogen and solid carbon with lower greenhouse gas emissions compared to traditional methods, faces several significant challenges. These include the high energy requirements for thermal decomposition, catalyst deactivation due to carbon deposition, and the need for advanced reactor designs to manage high temperatures and ensure continuous operation. Additionally, safety concerns related to explosion risks and toxic gas emissions must be addressed. These technical and operational hurdles highlight the need for further research and innovation to make methane pyrolysis a viable and scalable solution for sustainable energy production.
Key Points Explained:
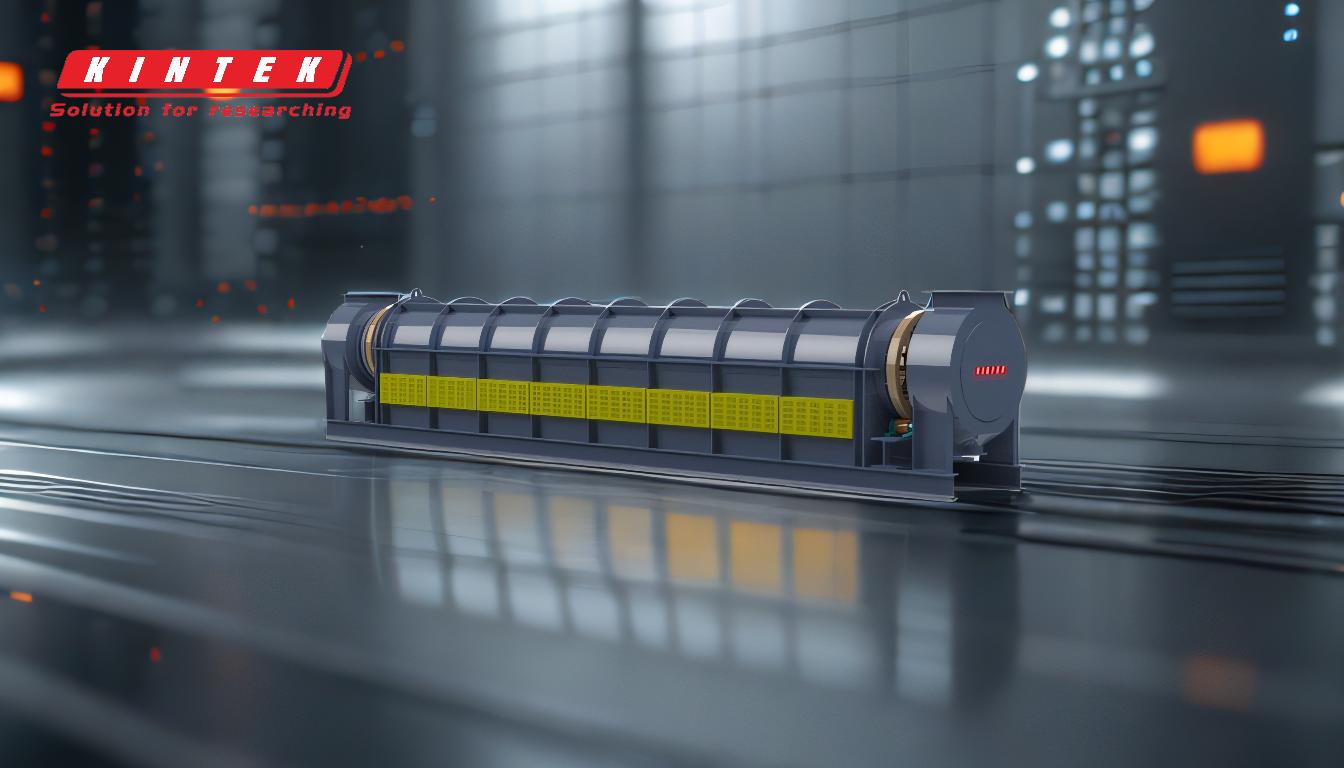
-
High Energy Requirements:
- Methane pyrolysis requires extremely high temperatures (typically above 750°C) to break down methane into hydrogen and solid carbon. This process is energy-intensive, leading to significant parasitic energy losses. Reducing these losses is critical to improving the overall efficiency and economic feasibility of the technology.
-
Catalyst Deactivation:
- Metal catalysts used in methane pyrolysis are prone to rapid deactivation due to the deposition of carbon on their surfaces. This not only reduces the efficiency of the process but also necessitates frequent catalyst replacement or regeneration, increasing operational costs and complexity.
-
Reactor Design Challenges:
- Designing reactors that can withstand high temperatures and manage the continuous production of hydrogen and carbon is a major challenge. Advanced reactor designs, such as those using molten metals or salts, are being explored to improve heat transfer and process stability. However, these designs are still in the research phase and require further development.
-
Safety Concerns:
- Methane pyrolysis involves high temperatures that exceed the autoignition temperature of the produced gases, creating a risk of explosion if oxygen is present. The process also generates toxic gases, such as carbon monoxide, which pose health and safety risks. Inert gas purging and robust safety systems are essential to mitigate these risks, but failures in these systems have led to accidents in the past.
-
Environmental Impact:
- While methane pyrolysis produces hydrogen with lower greenhouse gas emissions, it also generates solid carbon and potentially harmful by-products. Managing these by-products and ensuring that the process does not release pollutants into the environment is a significant challenge.
-
Feedstock Variability:
- The quality and composition of the methane feedstock can vary, affecting the efficiency and yield of the pyrolysis process. This variability complicates process optimization and requires sophisticated monitoring and control systems to maintain consistent product quality.
-
Scaling and Commercialization:
- Scaling up methane pyrolysis from laboratory or pilot-scale operations to commercial-scale production presents numerous technical and logistical challenges. These include ensuring process reliability, managing feedstock logistics, and reducing capital and operating costs to make the technology economically viable.
-
Research and Innovation Needs:
- Despite its potential, methane pyrolysis is still in the early stages of development. Significant research is needed to address the technical challenges, improve process efficiency, and develop cost-effective solutions for large-scale implementation.
In summary, while methane pyrolysis offers a promising pathway for sustainable hydrogen production, overcoming its technical, safety, and economic challenges is essential for its successful adoption and commercialization. Continued research and innovation will be key to unlocking its full potential.
Summary Table:
Challenge | Description |
---|---|
High Energy Requirements | Requires temperatures above 750°C, leading to significant energy losses. |
Catalyst Deactivation | Carbon deposition reduces efficiency, increasing operational costs. |
Reactor Design Challenges | Advanced designs needed to manage high temperatures and continuous operation. |
Safety Concerns | Risk of explosions and toxic gas emissions requires robust safety systems. |
Environmental Impact | Generates solid carbon and by-products, posing environmental challenges. |
Feedstock Variability | Variability in methane quality complicates process optimization. |
Scaling and Commercialization | Technical and logistical hurdles in scaling up to commercial production. |
Research and Innovation Needs | Significant R&D required to improve efficiency and reduce costs. |
Interested in learning more about methane pyrolysis? Contact our experts today for tailored solutions!