Silicon dioxide (SiO₂) films deposited by Plasma-Enhanced Chemical Vapor Deposition (PECVD) at low temperature and pressure exhibit a unique combination of properties that make them suitable for various applications, particularly in integrated circuit fabrication. These films are characterized by excellent electrical properties, good substrate adhesion, and uniform thickness. However, they may also have higher hydrogen content, higher etch rates, and the presence of pinholes, especially in thinner films. Despite these drawbacks, PECVD offers higher deposition rates and excellent step coverage, making it a preferred method for certain applications. The films are also resistant to chemical and thermal changes, ensuring durability and reliability in demanding environments.
Key Points Explained:
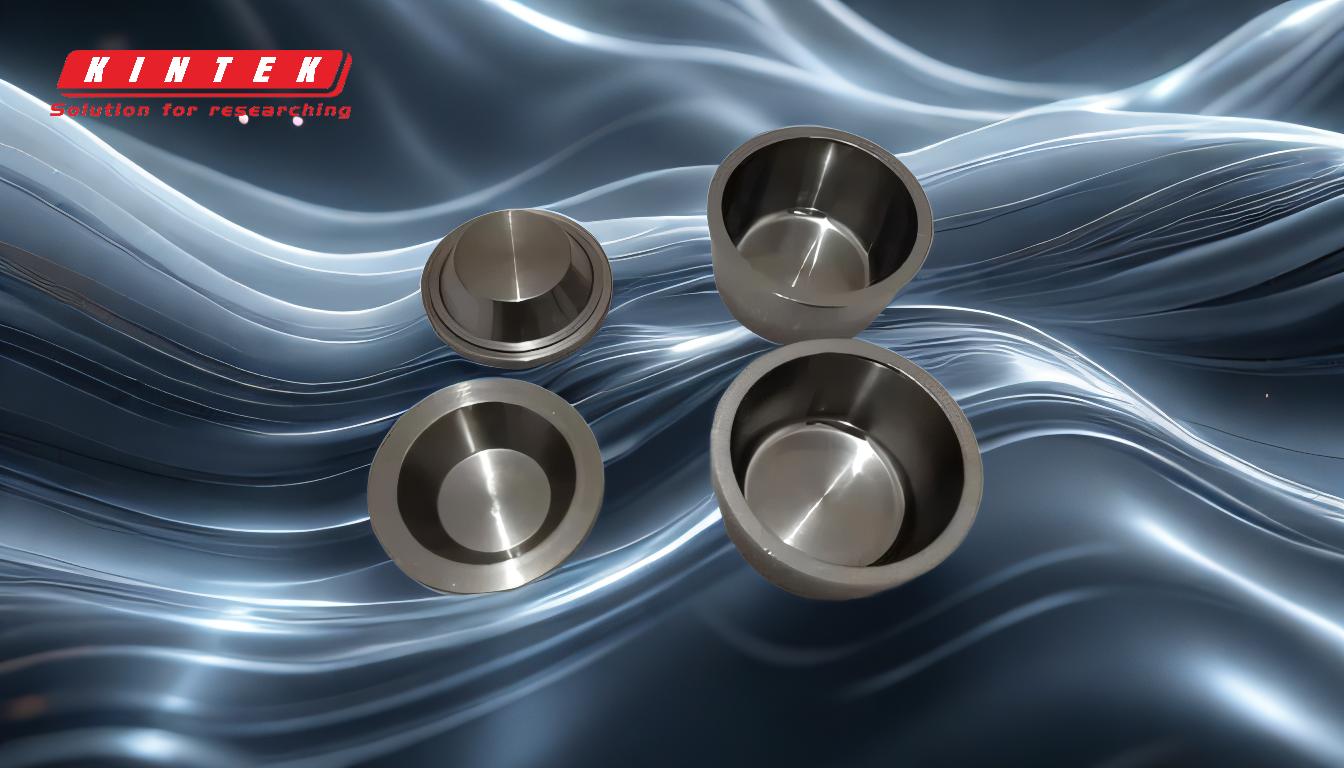
-
Electrical Properties:
- PECVD-deposited SiO₂ films exhibit excellent dielectric properties, which are crucial for applications in integrated circuits. These properties ensure minimal electrical interference and high performance in electronic devices.
- The films have low mechanical stress, which helps in maintaining the integrity of the layers in multi-layer structures, preventing cracking or delamination.
-
Substrate Adhesion:
- The films show good adhesion to various substrates, which is essential for the stability and longevity of the deposited layers. This property is particularly important in applications where the film must withstand mechanical or thermal stresses.
-
Uniformity and Thickness:
- PECVD films are known for their uniform thickness and high cross-linking, which contribute to the overall quality and reliability of the film. Uniformity is critical in applications such as integrated circuit fabrication, where even small variations can affect performance.
- The process allows for the deposition of films with consistent properties across large areas, which is beneficial for mass production.
-
Step Coverage:
- Excellent step coverage is one of the standout features of PECVD-deposited films. This property ensures that the film can uniformly cover complex geometries and high-aspect-ratio structures, which is essential for advanced semiconductor devices.
-
Hydrogen Content and Pinholes:
- PECVD films typically have higher hydrogen content compared to films deposited by other methods like LPCVD. This can affect the film's properties, such as its etch rate and mechanical strength.
- Thinner films (<~4000Å) are more prone to pinholes, which can compromise the film's integrity and performance. However, this issue can be mitigated by optimizing deposition parameters.
-
Deposition Rate:
- One of the advantages of PECVD is its higher deposition rate compared to other methods like LPCVD. This makes PECVD a more efficient process for applications where time is a critical factor.
-
Resistance to Chemical and Thermal Changes:
- PECVD-deposited SiO₂ films are resistant to chemical and thermal changes, making them suitable for use in harsh environments. This resistance ensures that the films maintain their properties over time, even when exposed to aggressive chemicals or high temperatures.
-
Applications:
- The properties of PECVD-deposited SiO₂ films make them ideal for use in integrated circuit fabrication, where maintaining the characteristics and performance of transistors is essential. The films' uniformity, step coverage, and electrical properties are particularly beneficial in this context.
In summary, PECVD-deposited silicon dioxide films at low temperature and pressure offer a balance of excellent electrical, physical, and mechanical properties, making them highly suitable for advanced semiconductor applications. While there are some drawbacks, such as higher hydrogen content and the presence of pinholes in thinner films, the overall benefits, including high deposition rates and excellent step coverage, make PECVD a valuable deposition method.
Summary Table:
Property | Description |
---|---|
Electrical Properties | Excellent dielectric properties, low mechanical stress, minimal interference |
Substrate Adhesion | Strong adhesion to various substrates, ensuring stability and longevity |
Uniformity & Thickness | High cross-linking, uniform thickness, suitable for mass production |
Step Coverage | Excellent coverage of complex geometries and high-aspect-ratio structures |
Hydrogen Content | Higher hydrogen content, affects etch rate and mechanical strength |
Pinholes | More common in thinner films (<~4000Å), can be mitigated with optimization |
Deposition Rate | Higher deposition rates compared to LPCVD, ideal for time-sensitive applications |
Chemical & Thermal Resistance | Resistant to harsh environments, maintains properties under stress |
Applications | Ideal for integrated circuit fabrication and advanced semiconductor devices |
Discover how PECVD-deposited SiO₂ films can enhance your semiconductor processes—contact our experts today!