Fast pyrolysis is a thermal decomposition process that converts biomass into bio-oil, biochar, and syngas in the absence of oxygen. The choice of reactor is critical as it directly impacts the efficiency, yield, and quality of the end products. Several types of reactors are commonly used for fast pyrolysis, each with unique design features and operational characteristics. These include fluidized bed reactors (bubbling and circulating), fixed bed reactors, rotary kilns, cyclonic reactors, and others. The design of these reactors focuses on heat transfer efficiency, durability, and the ability to handle high temperatures and pressures. Key features such as insulation, welding technology, and motor systems ensure optimal performance and safety. Understanding the differences between these reactors is essential for selecting the right system for specific pyrolysis applications.
Key Points Explained:
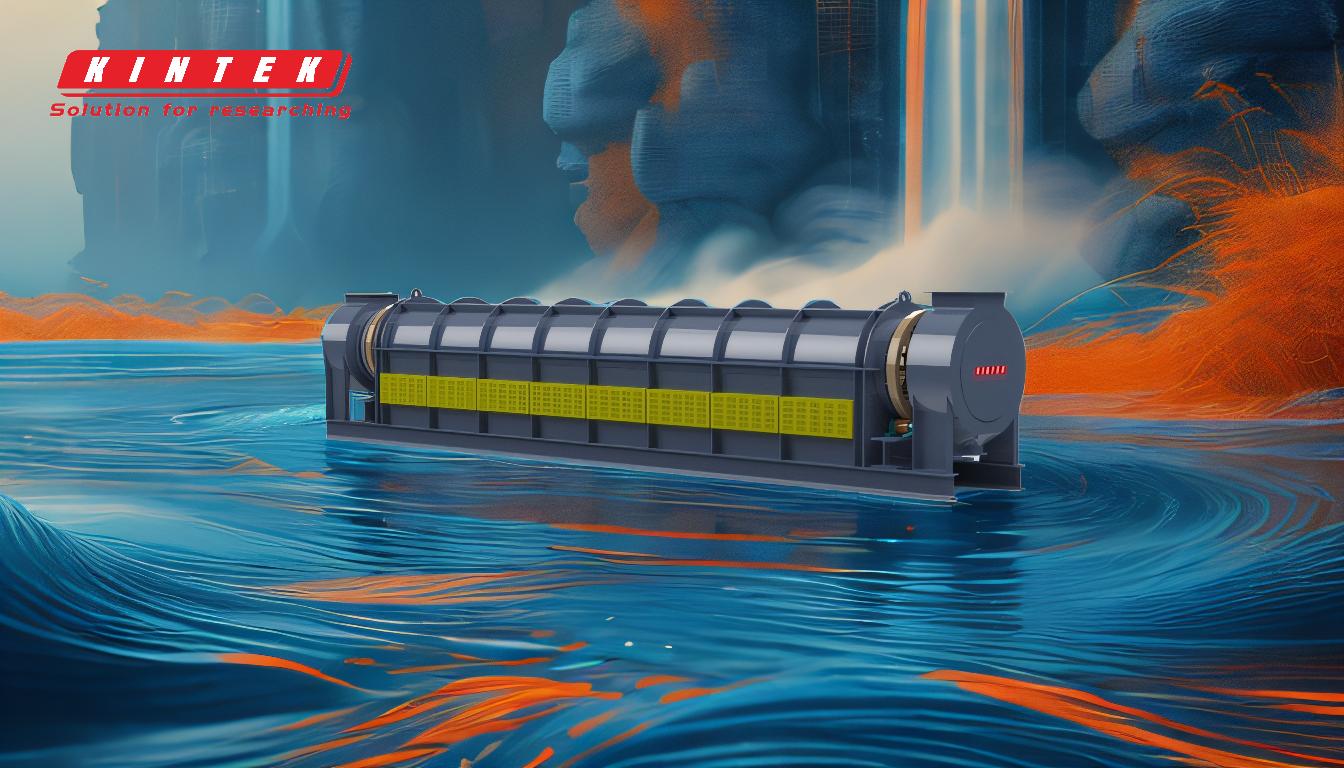
-
Types of Reactors for Fast Pyrolysis:
-
Fluidized Bed Reactors:
- Bubbling Fluidized Bed: Ensures excellent heat transfer and uniform temperature distribution, making it ideal for fast pyrolysis. It suspends biomass particles in a gas stream, allowing for rapid heating and decomposition.
- Circulating Fluidized Bed: Offers higher throughput and better control over residence time, which is crucial for optimizing bio-oil yield.
- Fixed Bed Reactors: Simple in design and suitable for small-scale operations. They operate by passing hot gases through a stationary bed of biomass, but heat transfer efficiency is lower compared to fluidized beds.
- Rotary Kiln Reactors: Use indirect heating to break down biomass, reducing contamination risks. They are versatile and can handle a wide range of feedstocks.
- Cyclonic Reactors: Utilize centrifugal force to separate particles and gases, enabling rapid pyrolysis with minimal residence time.
- Rotary Cone Reactors: Designed for continuous operation, they provide efficient mixing and heat transfer, making them suitable for large-scale applications.
-
Fluidized Bed Reactors:
-
Key Design Features:
- Material and Insulation: Reactors are often constructed from special boiler steel (e.g., Q345R) for heat transfer efficiency and longevity. Insulation materials like aluminum silicate refractory fiber cotton (80mm thick) ensure minimal heat loss.
- Welding and Safety: Advanced welding techniques and ultrasonic flaw detection tests ensure the structural integrity and safety of the reactor.
- Motor and Speed Control: Inverter motors paired with frequency converters allow for adjustable speed, improving efficiency and adaptability to different feedstocks.
- Durability: High-temperature resistant rollers and dynamic balance tests enhance the longevity and stability of the reactor.
-
Operational Characteristics:
- Heat Transfer Efficiency: Fluidized bed reactors excel in this aspect due to their ability to suspend biomass particles in a gas stream, ensuring rapid and uniform heating.
- Residence Time Control: Circulating fluidized beds and rotary kilns offer better control over residence time, which is critical for optimizing product yields.
- Feedstock Handling: Different reactors are suited to different types of feedstocks. For example, rotary kilns can handle larger and more varied biomass particles compared to fixed bed reactors.
-
Applications and Scalability:
- Small-Scale Operations: Fixed bed reactors are often used for small-scale or experimental setups due to their simplicity and lower cost.
- Large-Scale Production: Fluidized bed reactors and rotary kilns are preferred for industrial-scale applications due to their higher throughput and efficiency.
-
Emerging Reactor Designs:
- Dragged-Flow Reactors: Designed for rapid pyrolysis, they minimize residence time and maximize bio-oil yield.
- Vacuum Furnace Reactors: Operate under reduced pressure, which can enhance the quality of bio-oil by reducing secondary reactions.
- Vortex Reactors: Utilize swirling gas flows to achieve rapid heating and separation of pyrolysis products.
By understanding the different types of reactors and their design features, one can make informed decisions when selecting a reactor for fast pyrolysis applications. Each reactor type offers unique advantages, and the choice depends on factors such as feedstock type, desired product yield, and scale of operation.
Summary Table:
Reactor Type | Key Features | Applications |
---|---|---|
Fluidized Bed | - Excellent heat transfer, uniform temperature distribution | Fast pyrolysis, high bio-oil yield |
Fixed Bed | - Simple design, lower heat transfer efficiency | Small-scale operations |
Rotary Kiln | - Indirect heating, versatile feedstock handling | Large-scale, varied feedstocks |
Cyclonic Reactor | - Centrifugal force for rapid pyrolysis, minimal residence time | Rapid heating and separation |
Rotary Cone Reactor | - Continuous operation, efficient mixing and heat transfer | Large-scale applications |
Need help selecting the right reactor for your fast pyrolysis needs? Contact our experts today!