Pyrolysis, a process that decomposes organic materials at high temperatures in the absence of oxygen, carries several inherent risks. These include fire and explosion hazards due to the high temperatures exceeding the autoignition point of produced gases, toxic gas emissions like carbon monoxide, and challenges in waste handling and storage. Operational risks are heightened during startup, shutdown, intermittent operation, or operational upsets. Proper safety measures, such as inert gas purging and careful monitoring of temperature and pressure, are critical to mitigate these risks. Failure to implement these precautions can lead to accidents, posing significant threats to both personnel and equipment.
Key Points Explained:
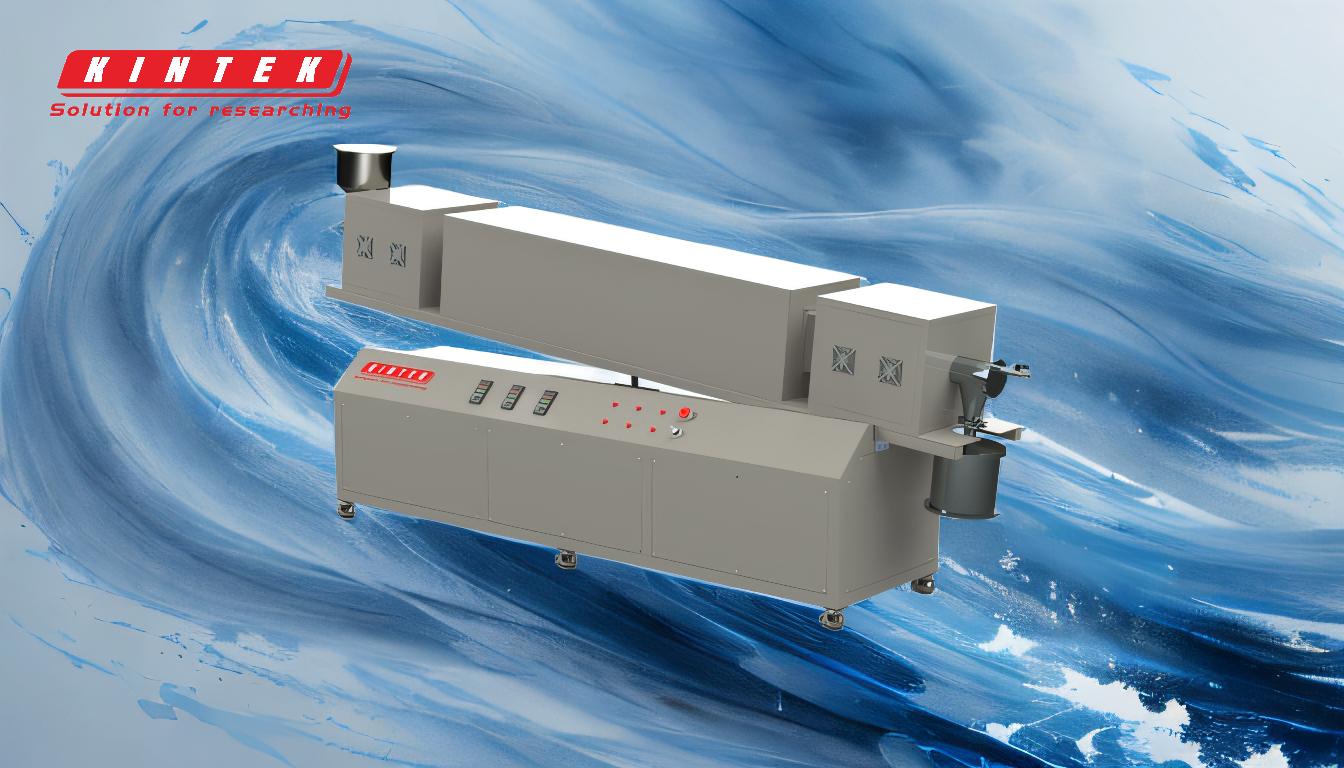
-
Fire and Explosion Hazards
- Pyrolysis occurs at temperatures that exceed the autoignition point of the gases produced.
- If oxygen is present, these gases can ignite, leading to explosions.
- The risk is particularly high during system startup, shutdown, or operational upsets when conditions are less stable.
- Inert gas purging is essential to displace oxygen and prevent ignition.
-
Toxic Gas Emissions
- The process generates toxic gases, primarily carbon monoxide, which poses serious health risks to workers.
- Exposure to these gases can lead to poisoning, respiratory issues, or even fatalities if not properly managed.
- Effective emission control systems are necessary to capture and neutralize these gases before release.
-
Operational Safety Concerns
- High temperatures and pressures in pyrolysis furnaces create hazardous working conditions.
- Careful monitoring and control of these parameters are critical to prevent equipment failure or accidents.
- Regular maintenance and safety checks are required to ensure the system operates within safe limits.
-
Waste Handling and Storage Challenges
- Pyrolysis produces solid residues and byproducts that require proper handling and storage.
- Improper disposal or storage can lead to environmental contamination or secondary hazards.
- Waste management protocols must be established to handle these materials safely.
-
Risk During Startup, Shutdown, and Intermittent Operation
- These phases are particularly vulnerable to accidents due to fluctuating conditions.
- Inconsistent operation can lead to incomplete reactions, gas buildup, or unintended releases.
- Strict operational procedures and safety protocols must be followed during these critical periods.
-
Importance of Inert Gas Purging
- Inert gases like nitrogen are used to purge oxygen from the system, reducing explosion risks.
- Failure to maintain an oxygen-free environment has been a leading cause of accidents in pyrolysis plants.
- Proper training and adherence to purging protocols are essential for safe operation.
-
Mitigation Strategies
- Implement robust safety systems, including gas detectors, pressure relief valves, and automated shutdown mechanisms.
- Conduct regular risk assessments and safety audits to identify and address potential hazards.
- Provide comprehensive training to operators on emergency response and safe handling procedures.
By understanding and addressing these risks, pyrolysis plants can operate more safely and efficiently, minimizing the potential for accidents and ensuring the well-being of workers and the environment.
Summary Table:
Risk Category | Key Concerns | Mitigation Strategies |
---|---|---|
Fire and Explosion Hazards | High temperatures exceed autoignition point; oxygen presence can cause explosions. | Use inert gas purging, monitor temperature/pressure, and implement automated shutdowns. |
Toxic Gas Emissions | Carbon monoxide and other toxic gases pose health risks. | Install emission control systems and ensure proper ventilation. |
Operational Safety | High temperatures and pressures create hazardous conditions. | Regular maintenance, safety checks, and operator training are essential. |
Waste Handling | Solid residues and byproducts require safe disposal to prevent contamination. | Establish waste management protocols and ensure proper storage. |
Startup/Shutdown Risks | Fluctuating conditions increase accident risks during critical phases. | Follow strict operational procedures and safety protocols. |
Inert Gas Purging | Oxygen-free environments are crucial to prevent explosions. | Train operators on purging protocols and maintain consistent purging practices. |
Mitigation Strategies | Accidents can be minimized with robust safety systems and regular risk assessments. | Conduct safety audits, install gas detectors, and provide emergency response training. |
Ensure the safety of your pyrolysis operations—contact our experts today for tailored solutions!