Ball milling is a mechanical process used to grind, mix, or blend materials into fine powders or nanoparticles. It involves placing the material to be processed into a grinding jar along with grinding balls. The jar is then rotated or shaken, causing the balls to collide with the material and each other, leading to particle size reduction, deformation, and other structural changes. The process involves several key steps, including flattening, welding, layering, deformation, and nanoparticle formation, all of which contribute to the final product's properties.
Key Points Explained:
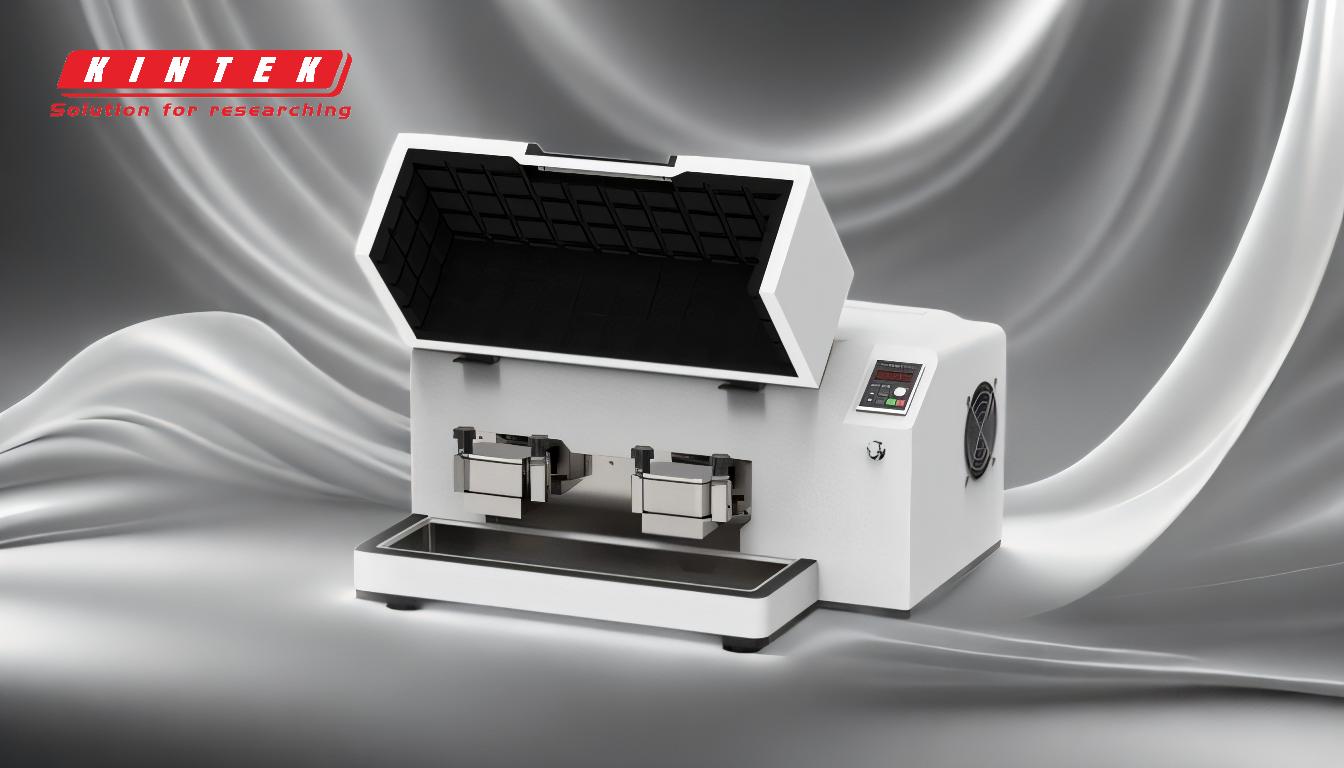
-
Preparation of Materials and Equipment
- The first step in ball milling is preparing the materials and equipment. This involves selecting the appropriate grinding jar and grinding balls, which are typically made of the same material to avoid contamination.
- The material to be processed (powder or other forms) is weighed and added to the jar along with the grinding balls. The ratio of balls to material is critical for achieving the desired grinding efficiency.
- The jar is then sealed to prevent contamination and ensure safety during the milling process.
-
Flattening of Powder Particles
- As the grinding jar rotates or shakes, the grinding balls collide with the powder particles, applying compressive and shear forces.
- These forces cause the powder particles to flatten, reducing their thickness and increasing their surface area.
- Flattening is an essential step in achieving uniformity and preparing the particles for further structural changes.
-
Welding of Powder Particles
- The repeated collisions and mechanical energy input can cause particles to weld together. This occurs due to the high-energy impacts, which generate localized heat and pressure.
- Welding leads to the formation of larger agglomerates or composite particles, which can be beneficial for certain applications, such as creating layered structures or enhancing mechanical properties.
-
Formation of Layered Structures
- During the milling process, the flattened and welded particles can form layered structures. This is particularly common when working with materials that have different properties or compositions.
- The layers are created as particles are repeatedly flattened and welded, resulting in a stratified arrangement that can enhance specific material properties, such as strength or conductivity.
-
Deformation of the Layered Structure
- As milling continues, the layered structures undergo further deformation. The mechanical forces cause the layers to bend, fold, or fracture, leading to changes in the material's microstructure.
- This step is crucial for refining the material's properties, as it can introduce defects or dislocations that improve mechanical performance or reactivity.
-
Formation of Nanoparticles
- Prolonged milling can break down the particles into smaller and smaller sizes, eventually leading to the formation of nanoparticles.
- This step is highly dependent on the milling time, speed, and the nature of the material being processed. Nanoparticles have unique properties due to their high surface area-to-volume ratio, making them valuable for applications in catalysis, electronics, and medicine.
-
Post-Milling Processing
- After the milling process is complete, the material is removed from the jar and may undergo additional processing steps, such as sieving, annealing, or coating, to achieve the desired final properties.
- The grinding balls and jar are cleaned to prevent cross-contamination in future milling operations.
By following these steps, ball milling can effectively transform raw materials into finely ground powders or nanoparticles with tailored properties for various industrial and scientific applications.
Summary Table:
Step | Description |
---|---|
Preparation | Select grinding jar and balls, add material, and seal the jar to avoid contamination. |
Flattening | Powder particles are flattened by grinding balls, increasing surface area. |
Welding | Particles weld together due to high-energy impacts, forming agglomerates. |
Layered Structures | Flattened and welded particles form stratified layers for enhanced properties. |
Deformation | Layers bend, fold, or fracture, refining material properties. |
Nanoparticle Formation | Prolonged milling breaks particles into nanoparticles with unique properties. |
Post-Milling Processing | Material undergoes sieving, annealing, or coating for final properties. |
Discover how ball milling can optimize your material processing—contact our experts today!