The sputtering process is a widely used physical vapor deposition (PVD) technique for depositing thin films of materials onto substrates. It involves creating a vacuum, introducing an inert gas, ionizing the gas to form a plasma, and using the plasma to eject atoms from a target material, which then deposit onto a substrate. The process is highly controlled, ensuring the deposition of high-purity, uniform coatings. Below, the steps involved in the sputtering process are explained in detail.
Key Points Explained:
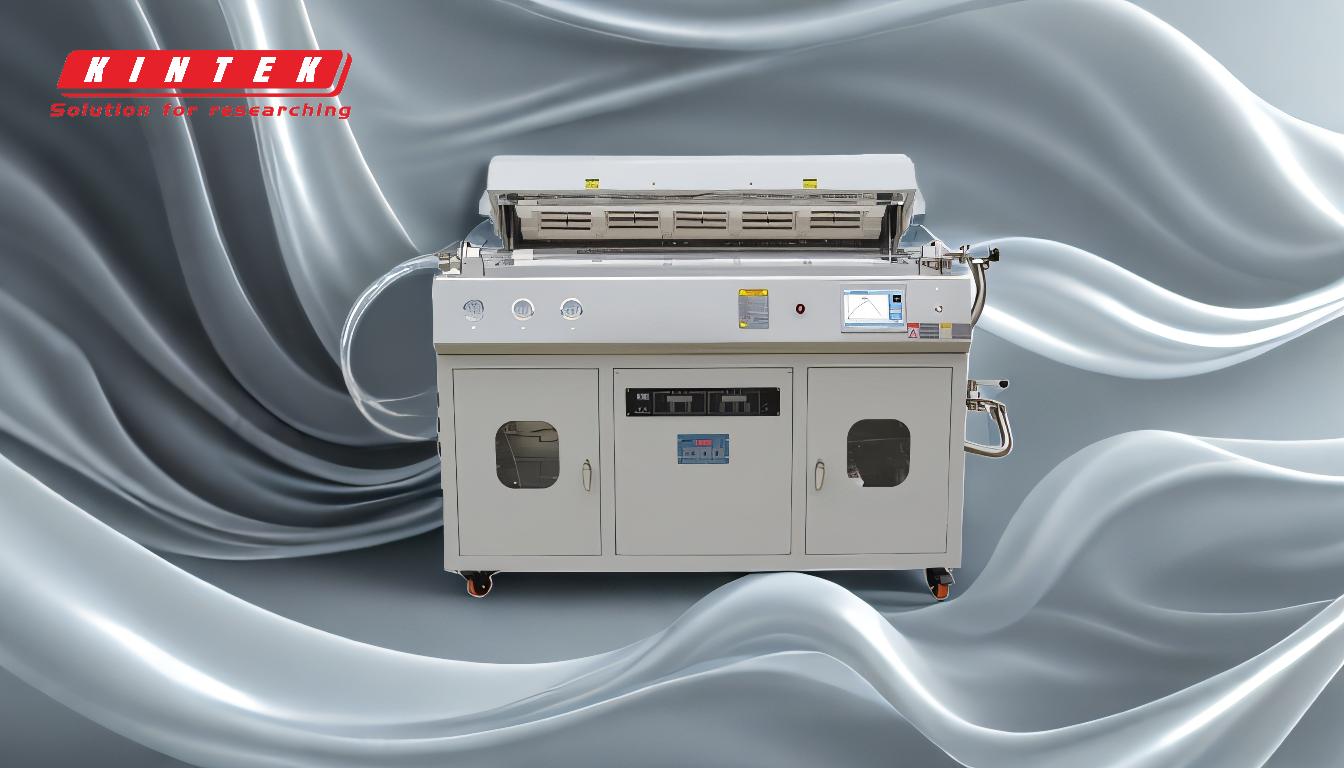
-
Creating a Vacuum in the Reaction Chamber
- The first step involves evacuating the reaction chamber to remove moisture, impurities, and residual gases.
- The pressure is typically reduced to around 1 Pa (0.0000145 psi) to create a clean environment for the process.
- A vacuum ensures that contaminants do not interfere with the deposition, which is critical for achieving high-quality coatings.
-
Introducing an Inert Gas
- Once a vacuum is established, an inert gas (usually Argon) is introduced into the chamber.
- The gas is chosen because it is chemically inert, minimizing unwanted reactions during the process.
- The pressure of the gas is adjusted to create a low-pressure atmosphere, typically in the range of 10⁻¹ to 10⁻³ mbar, which is ideal for plasma formation.
-
Heating the Chamber
- The chamber is heated to temperatures ranging from 150°C to 750°C (302°F to 1382°F), depending on the material being deposited.
- Heating ensures proper adhesion of the coating to the substrate and can also influence the microstructure and properties of the deposited film.
-
Generating a Plasma
- A high voltage (3-5 kV) is applied to ionize the Argon gas, creating a plasma.
- The plasma consists of positively charged Argon ions (Ar⁺) and free electrons.
- A magnetic field is often used to confine and control the plasma, enhancing the efficiency of the ionization process.
-
Accelerating Ions Toward the Target
- The positively charged Ar⁺ ions are accelerated toward the target material (the source of the coating material).
- The target is negatively charged, creating an electric field that attracts the ions.
- When the ions collide with the target, they transfer their energy, causing atoms to be ejected from the target's surface.
-
Transporting Sputtered Atoms to the Substrate
- The ejected atoms are transported through the low-pressure environment toward the substrate.
- The reduced pressure minimizes collisions between atoms, ensuring a directed flow of material.
- This step is critical for achieving uniform deposition across the substrate.
-
Depositing the Thin Film
- The sputtered atoms condense on the substrate's surface, forming a thin film.
- The energy of the deposited atoms can enhance surface mobility, leading to better adhesion and film quality.
- The process continues until the desired thickness of the coating is achieved.
-
Controlling Process Parameters
- Throughout the process, parameters such as pressure, temperature, voltage, and magnetic field strength are carefully controlled.
- These parameters influence the rate of deposition, the quality of the film, and the properties of the final coating.
- Adjustments can be made to optimize the process for specific materials and applications.
The sputtering process is a precise and versatile method for depositing thin films of materials onto substrates. By carefully controlling each step, from creating a vacuum to depositing the coating, manufacturers can achieve high-quality, uniform films with excellent adhesion and purity. This makes sputtering a preferred technique in industries such as electronics, optics, and aerospace, where precision and performance are critical.
Summary Table:
Step | Key Details |
---|---|
1. Creating a Vacuum | Evacuate the chamber to ~1 Pa to remove contaminants. |
2. Introducing Inert Gas | Add Argon gas at 10⁻¹ to 10⁻³ mbar for plasma formation. |
3. Heating the Chamber | Heat to 150°C–750°C to enhance adhesion and film properties. |
4. Generating Plasma | Apply 3-5 kV to ionize Argon, creating a plasma. |
5. Accelerating Ions | Positively charged Ar⁺ ions collide with the negatively charged target. |
6. Transporting Atoms | Sputtered atoms flow to the substrate in a low-pressure environment. |
7. Depositing Thin Film | Atoms condense on the substrate, forming a uniform, high-quality coating. |
8. Controlling Parameters | Adjust pressure, temperature, voltage, and magnetic field for optimal results. |
Need high-quality thin film deposition solutions? Contact our experts today to learn more!