Pyrolysis is a thermal decomposition process that breaks down organic materials in the absence of oxygen. It typically occurs in three stages: drying, pyrolysis, and cooling. Each stage plays a critical role in transforming the feedstock into valuable products such as biochar, bio-oil, and syngas. The process is influenced by factors like temperature, residence time, and the type of feedstock. Understanding these stages is essential for optimizing the design and operation of a pyrolysis reactor to achieve desired outputs efficiently.
Key Points Explained:
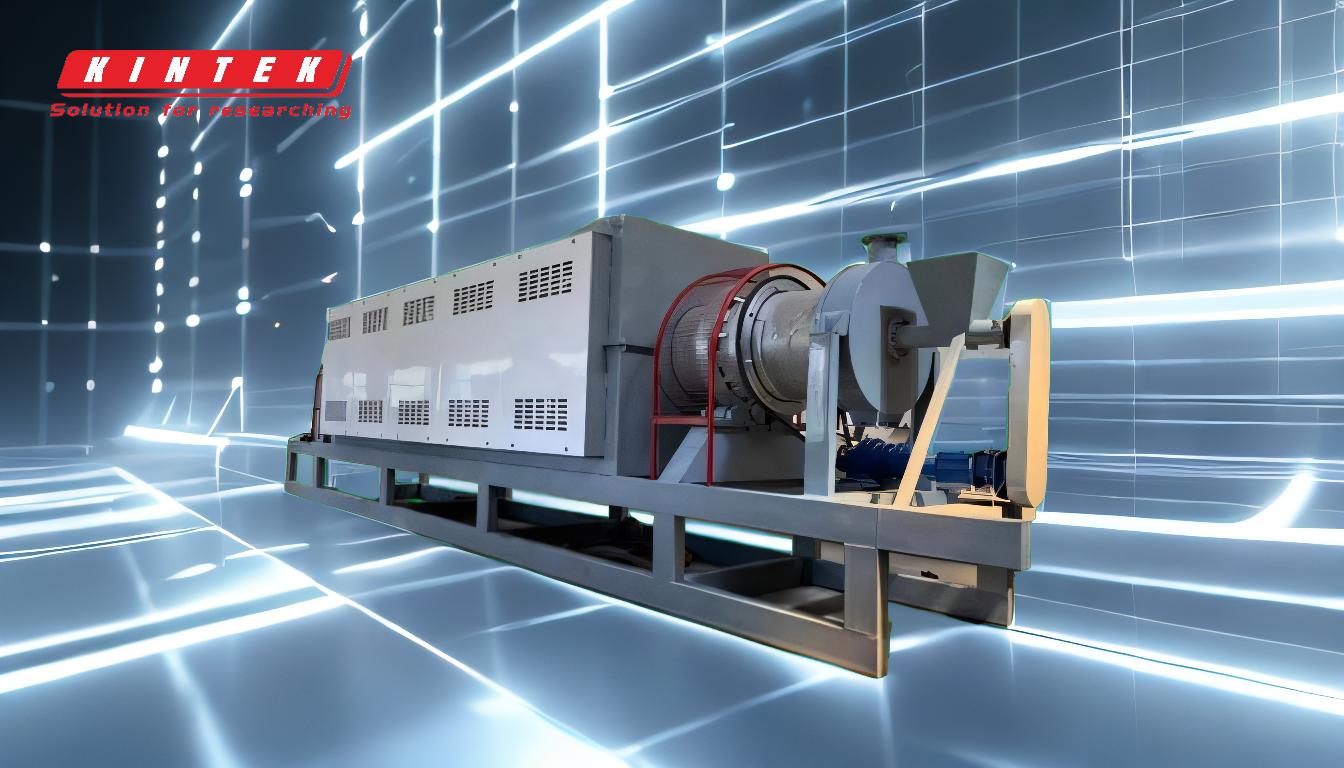
-
Drying Stage
- The first stage of pyrolysis involves removing moisture from the feedstock.
- This step is crucial because water content can interfere with the thermal decomposition process and reduce the efficiency of the reactor.
- Temperatures during this stage are relatively low, typically between 100°C and 150°C, to evaporate moisture without initiating chemical breakdown.
- Proper drying ensures that the subsequent pyrolysis reactions occur uniformly and efficiently.
-
Pyrolysis Stage
- The second stage is the core of the pyrolysis process, where the dried feedstock undergoes thermal decomposition.
- This stage occurs in the absence of oxygen, preventing combustion and allowing the material to break down into smaller molecules.
- Depending on the desired products, the temperature can range from 300°C to 800°C.
- Slow Pyrolysis: Operates at lower temperatures (300°C–500°C) with longer residence times, favoring the production of biochar.
- Fast Pyrolysis: Operates at higher temperatures (500°C–800°C) with short residence times, maximizing bio-oil yield.
- The feedstock is converted into three primary products:
- Biochar: A solid residue rich in carbon.
- Bio-oil: A liquid mixture of organic compounds.
- Syngas: A gaseous mixture of hydrogen, carbon monoxide, and methane.
-
Cooling Stage
- The final stage involves cooling the products to stabilize them and prevent further reactions.
- Biochar is typically cooled and collected for use as a soil amendment or fuel.
- Bio-oil is condensed from the vapor phase and stored for further refining or use as a fuel.
- Syngas is often cleaned and used as a renewable energy source or as a feedstock for chemical synthesis.
- Efficient cooling is essential to ensure the quality and usability of the products.
By understanding these three stages—drying, pyrolysis, and cooling—operators can optimize the performance of a pyrolysis reactor to achieve specific product yields and improve overall process efficiency. The choice of operating conditions (temperature, residence time, and feedstock type) will significantly influence the outcome of each stage and the final product distribution.
Summary Table:
Stage | Key Details | Temperature Range | Outputs |
---|---|---|---|
Drying | Removes moisture from feedstock to ensure efficient thermal decomposition. | 100°C–150°C | Dry feedstock |
Pyrolysis | Thermal decomposition in the absence of oxygen; produces biochar, bio-oil, syngas. | 300°C–800°C | Biochar, bio-oil, syngas |
Cooling | Stabilizes products to prevent further reactions and ensure usability. | Varies | Stable biochar, bio-oil, syngas |
Ready to optimize your pyrolysis process? Contact our experts today for tailored solutions!