Calcination is a thermal treatment process used in various industries to achieve specific chemical and physical transformations in materials. It involves heating a substance to high temperatures, typically below its melting point, in the presence of limited air or oxygen. The primary purposes of calcination include removing volatile impurities, decomposing compounds, and oxidizing materials. This process is widely applied in industries such as cement production, metallurgy, and chemical synthesis, where it plays a crucial role in transforming raw materials into usable products. Below, the key uses of calcination are explained in detail.
Key Points Explained:
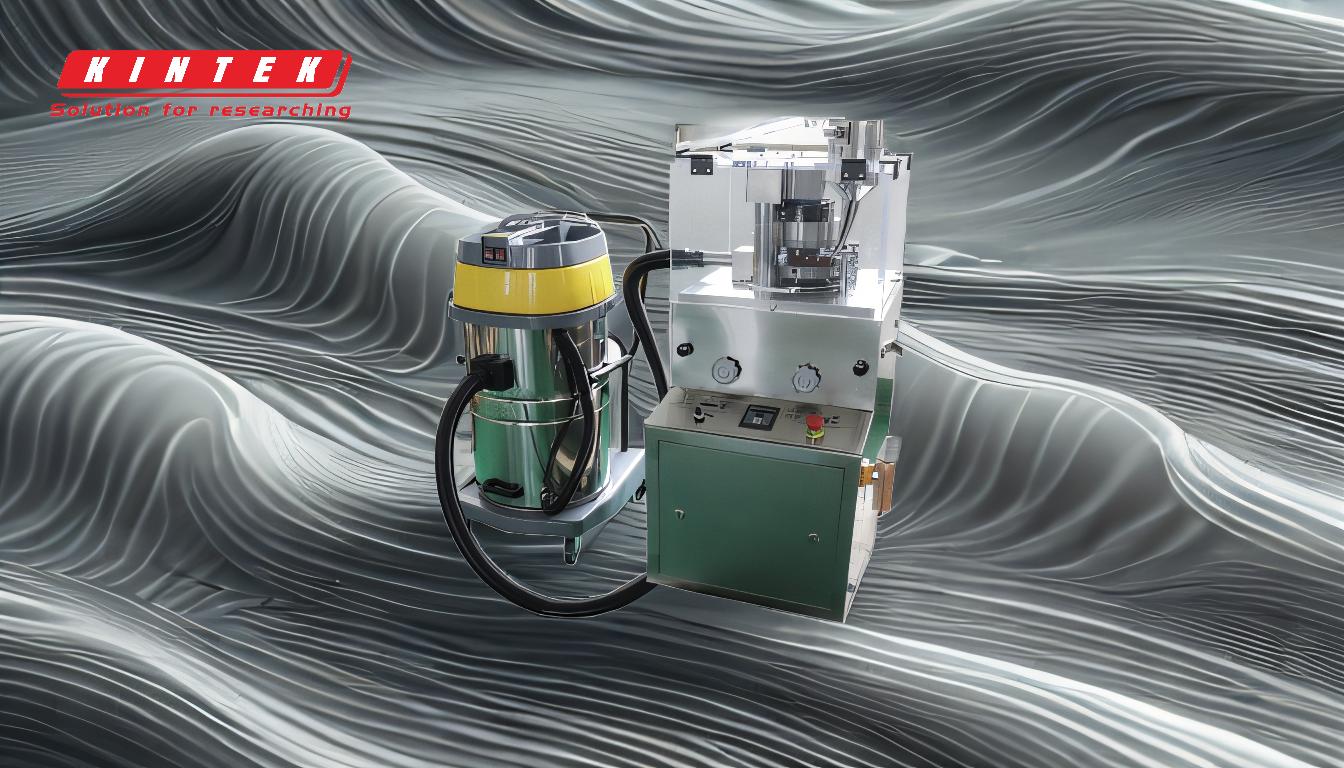
-
Production of Cement:
- Calcination is a critical step in cement manufacturing. It involves heating calcium carbonate (limestone) to high temperatures, causing it to decompose into calcium oxide (quicklime) and carbon dioxide.
- The chemical reaction is:
[ \text{CaCO}_3 \xrightarrow{\text{heat}} \text{CaO} + \text{CO}_2 ] - Calcium oxide is a key ingredient in cement, and the process of calcination ensures the removal of carbon dioxide, which is essential for the formation of the final product.
-
Removal of Volatile Impurities from Metal Ores:
- In metallurgy, calcination is used to purify metal ores by removing volatile impurities such as water, carbon dioxide, and sulfur dioxide.
- For example, sulfide ores are often calcined to remove sulfur as sulfur dioxide gas, leaving behind a purer metal oxide.
- This process is particularly important in the extraction of metals like zinc, lead, and copper.
-
Dehydration of Materials:
- Calcination is used to remove chemically bound water (water of hydration) from materials such as gypsum (calcium sulfate dihydrate) to produce plaster of Paris (calcium sulfate hemihydrate).
- The reaction is:
[ \text{CaSO}_4 \cdot 2\text{H}_2\text{O} \xrightarrow{\text{heat}} \text{CaSO}_4 \cdot 0.5\text{H}_2\text{O} + 1.5\text{H}_2\text{O} ] - This dehydration process is essential in industries like construction and ceramics.
-
Oxidation of Materials:
- Calcination can be used to oxidize part or all of a substance. For example, iron ores are calcined to convert ferrous oxide (FeO) into ferric oxide (Fe₂O₃), which is more stable and easier to process in subsequent metallurgical steps.
- Oxidation during calcination is also used in the production of pigments and catalysts.
-
Synthesis of Zeolites:
- Calcination is a key step in the synthesis of zeolites, which are widely used as catalysts and adsorbents. During this process, ammonium ions are removed from the zeolite framework, leaving behind a porous structure with active sites for catalytic reactions.
- This application is crucial in the petrochemical industry for processes like cracking and isomerization.
-
Devitrification of Glass:
- Calcination is used in the glass industry to induce phase transformations in glass, a process known as devitrification. This can improve the mechanical and thermal properties of glass, making it suitable for specialized applications.
- For example, devitrified glass is used in high-temperature applications where regular glass would fail.
-
Processing of Minerals:
- Calcination is employed in the processing of minerals like limestone, dolomite, and magnesite. Rotary kilns are commonly used for this purpose, as they provide uniform heating and are suitable for particle sizes of 60 mm or less.
- The process helps in the dissociation of these minerals into their respective oxides, which are then used in various industrial applications.
-
Removal of Carbon Dioxide and Sulfur Dioxide:
- In addition to cement production, calcination is used to remove carbon dioxide and sulfur dioxide from other materials. For instance, in the production of soda ash (sodium carbonate), calcination helps decompose sodium bicarbonate into sodium carbonate and carbon dioxide.
-
Preparation of Catalysts:
- Calcination is a critical step in the preparation of catalysts. It helps stabilize the active phase of the catalyst and remove any volatile components that might interfere with its performance.
- This is particularly important in the chemical and petrochemical industries, where catalysts are used to accelerate reactions.
-
Environmental Applications:
- Calcination is used in environmental applications, such as the treatment of hazardous waste. By heating waste materials to high temperatures, harmful organic compounds can be decomposed, and metals can be recovered for recycling.
In summary, calcination is a versatile and essential process used across multiple industries to achieve specific chemical and physical transformations. Its applications range from cement production and metal purification to catalyst preparation and environmental waste treatment. Understanding the uses of calcination helps in selecting the right equipment and optimizing processes for various industrial needs.
Summary Table:
Application | Description |
---|---|
Cement Production | Decomposes calcium carbonate into calcium oxide (quicklime) and carbon dioxide. |
Metal Ore Purification | Removes volatile impurities like sulfur dioxide from metal ores. |
Dehydration of Materials | Removes chemically bound water from materials like gypsum. |
Oxidation of Materials | Converts ferrous oxide to ferric oxide for stability. |
Zeolite Synthesis | Prepares porous structures for catalytic reactions. |
Devitrification of Glass | Enhances mechanical and thermal properties of glass. |
Mineral Processing | Dissociates minerals like limestone into oxides. |
Catalyst Preparation | Stabilizes catalysts by removing volatile components. |
Environmental Waste Treatment | Decomposes hazardous waste and recovers metals. |
Discover how calcination can optimize your industrial processes—contact our experts today!