Thermal evaporation is a versatile deposition technique widely used across various industries for creating thin films and coatings. Its primary applications include electronics, optics, packaging, and decorative purposes. In electronics, it is extensively used for depositing metals like silver and aluminum in devices such as OLEDs, solar cells, and thin-film transistors. In optics, it is employed for anti-reflective coatings, UV protection, and lens enhancements. Additionally, thermal evaporation plays a role in consumer packaging, where it is used to deposit aluminum films on plastics, and in decorative applications, such as jewelry and sporting goods. It also finds use in specialized fields like aerospace, where it contributes to EMI/RFI shielding and light reflectors.
Key Points Explained:
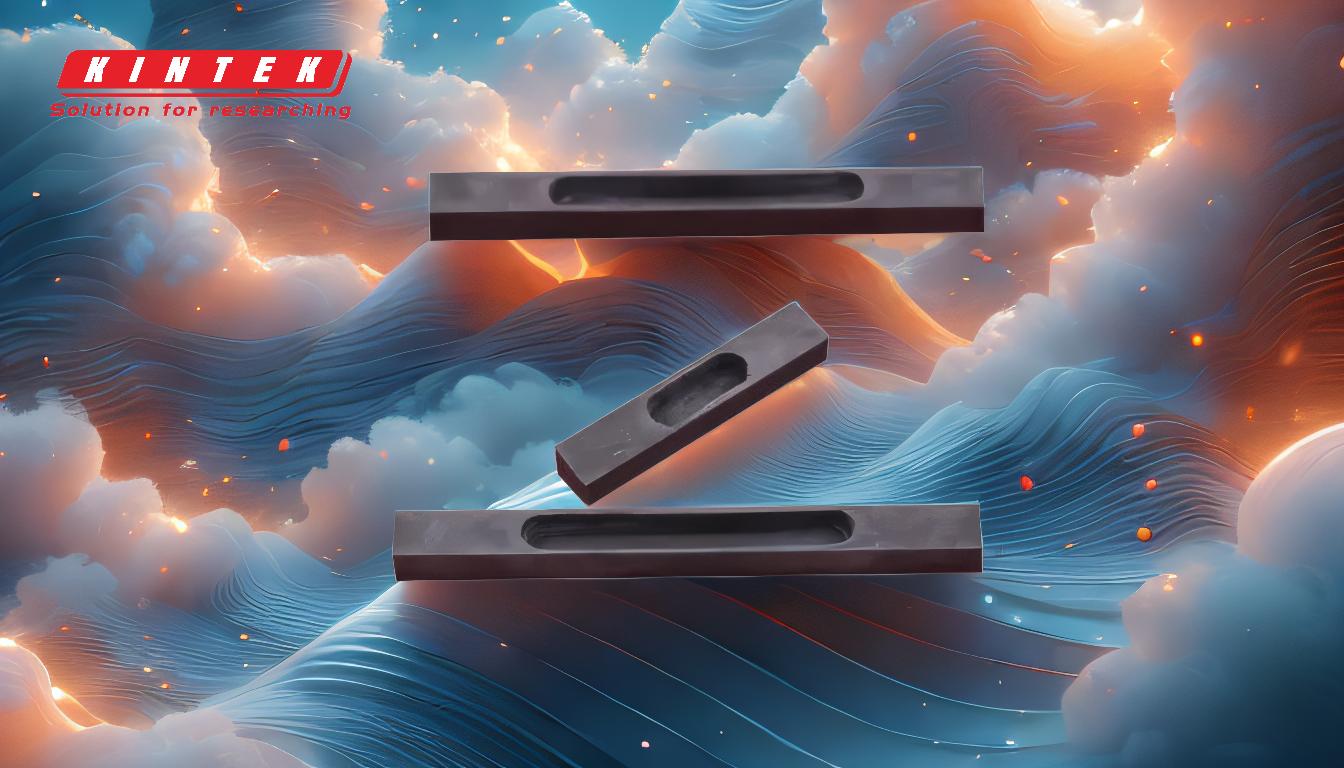
-
Electronics and Electrical Contacts
- Thermal evaporation is commonly used to deposit metals like silver and aluminum in electronic devices.
- Applications include creating electrical contacts in OLEDs, solar cells, and thin-film transistors.
- The process ensures precise deposition of ultra-thin metal layers, which are critical for device performance.
-
Optical Applications
- In the optics industry, thermal evaporation is used for coatings such as anti-reflective layers, UV protection, and lens enhancements.
- These coatings improve the performance and durability of optical components, making them suitable for cameras, telescopes, and eyeglasses.
-
Consumer Packaging
- Thermal evaporation deposits thin aluminum films on plastic packaging, enhancing barrier properties against moisture and oxygen.
- This application is crucial for food packaging, ensuring product freshness and extending shelf life.
-
Decorative and Aesthetic Uses
- The technique is employed in decorative applications, such as cosmetic closures, jewelry, and sporting goods.
- Thin-film coatings provide aesthetic finishes, making products visually appealing and durable.
-
Specialized Industrial Applications
- Thermal evaporation is used in aerospace, medical, and automotive industries for EMI/RFI shielding and light reflectors.
- It also contributes to the production of specialized materials like NASA spacesuits, firefighter uniforms, and emergency blankets.
-
Complex Co-Deposition
- By controlling the temperature of individual crucibles, thermal evaporation can co-deposit multiple materials.
- This capability is essential for creating complex multi-layer structures in advanced electronic and optical devices.
-
Sustainability and Insulation
- The technique is used to deposit thin films for heat and sound insulation in various applications.
- It also contributes to anti-static and soundproof enclosures in aircraft and other high-tech environments.
Thermal evaporation's versatility, precision, and ability to handle a wide range of materials make it indispensable in modern manufacturing and technology development.
Summary Table:
Industry | Applications |
---|---|
Electronics | Depositing metals (e.g., silver, aluminum) in OLEDs, solar cells, transistors. |
Optics | Anti-reflective coatings, UV protection, lens enhancements. |
Consumer Packaging | Aluminum films for moisture/oxygen barrier in food packaging. |
Decorative | Aesthetic finishes for jewelry, sporting goods, and cosmetic closures. |
Specialized Industries | EMI/RFI shielding, light reflectors, NASA spacesuits, firefighter uniforms. |
Complex Co-Deposition | Multi-layer structures for advanced electronic and optical devices. |
Sustainability | Heat/sound insulation, anti-static, and soundproof enclosures. |
Unlock the potential of thermal evaporation for your industry—contact us today to learn more!