Thermal evaporation sources are devices used in the thin film deposition process, specifically in the physical vapor deposition (PVD) method. They work by heating a target material to its evaporation point, causing it to vaporize and then condense onto a substrate to form a thin film. This technique is widely used in industries such as electronics, optics, and packaging due to its ability to create precise and uniform coatings. Thermal evaporation is particularly useful for depositing metals and other materials in applications like OLEDs, solar cells, and thin-film transistors.
Key Points Explained:
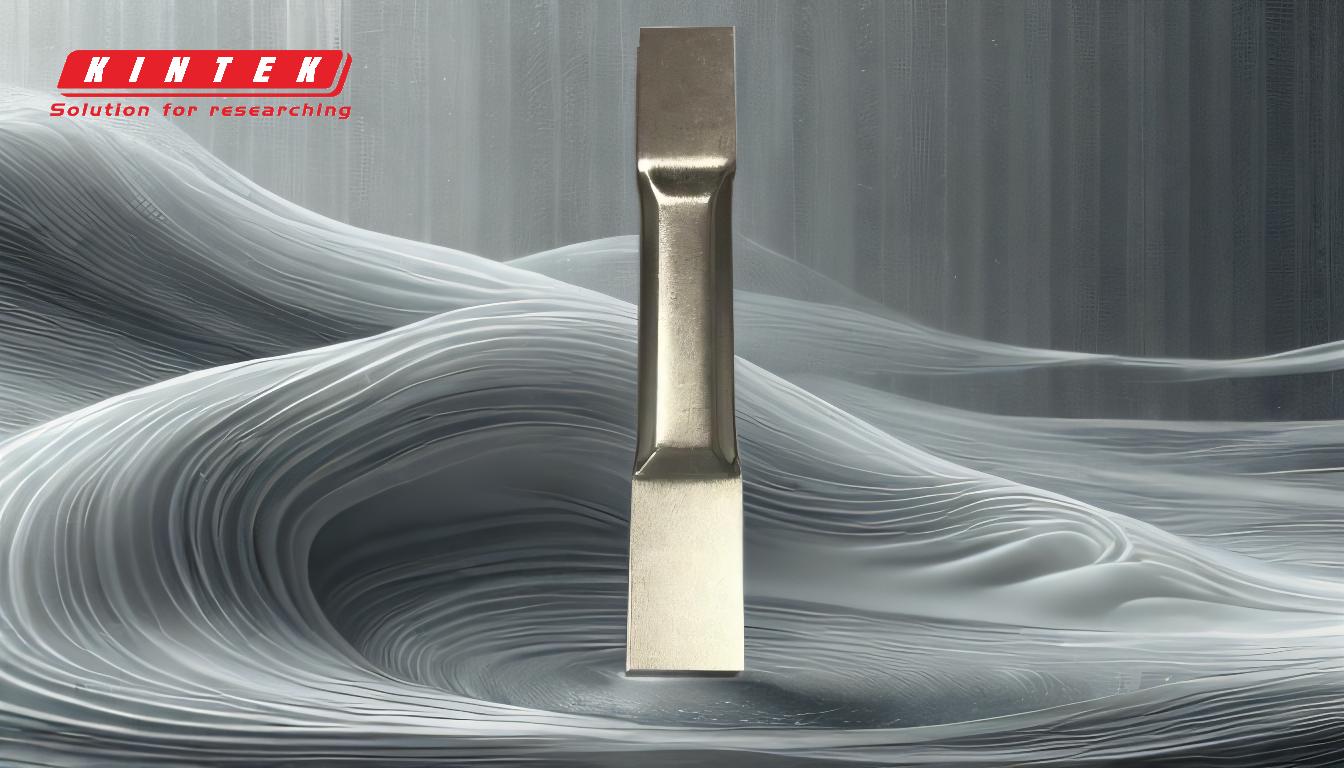
-
Definition and Process of Thermal Evaporation
- Thermal evaporation is a form of physical vapor deposition (PVD) where a target material is heated to extreme temperatures until it vaporizes.
- The vaporized material then travels through a vacuum or low-pressure environment and condenses onto a substrate, forming a thin film.
- This process is simple yet effective for creating uniform and high-quality coatings.
-
Key Components of Thermal Evaporation Systems
- Evaporation Source: Typically a crucible or boat made of materials like tungsten or graphite, which can withstand high temperatures.
- Heating Mechanism: Often involves resistive heating or electron beam heating to achieve the required evaporation temperature.
- Vacuum Chamber: Ensures a controlled environment to prevent contamination and allow efficient material transport.
- Substrate Holder: Positions the substrate to receive the vaporized material evenly.
-
Applications of Thermal Evaporation
- Electronics: Used to create metal bonding layers in OLEDs, thin-film transistors, and solar cells.
- Packaging: Deposits thin films of metals like aluminum on polymers for food packaging, heat insulation, and decorative purposes.
- Aerospace and Safety: Applied in NASA spacesuits, firefighter uniforms, and emergency blankets for reflective and insulating properties.
- Industrial Uses: Includes anti-static coatings and soundproof enclosures in aircraft.
-
Advantages of Thermal Evaporation
- High Purity: The vacuum environment minimizes contamination, resulting in high-purity films.
- Precision: Allows for precise control over film thickness and uniformity.
- Versatility: Suitable for a wide range of materials, including metals, alloys, and some organic compounds.
-
Comparison with Other Deposition Methods
- Sputtering: Unlike thermal evaporation, sputtering uses ionized gas to ablate the target material, making it a "line of sight" process.
- Chemical Vapor Deposition (CVD): Thermal evaporation is purely physical, while CVD involves chemical reactions to deposit the film.
- Electron Beam Evaporation: A variation of thermal evaporation that uses an electron beam for heating, offering higher energy and better control for certain materials.
-
Considerations for Equipment Purchasers
- Material Compatibility: Ensure the system can handle the specific materials and temperatures required for your application.
- Vacuum Quality: High-quality vacuum systems are essential for achieving optimal film properties.
- Scalability: Consider whether the system can be scaled for larger production volumes if needed.
- Maintenance and Durability: Evaluate the longevity and ease of maintenance of the components, especially the evaporation source and heating elements.
Thermal evaporation is a versatile and reliable method for thin film deposition, particularly suited for applications requiring high purity and precision. For more detailed insights, you can explore the topic further at thermal evaporation.
Summary Table:
Aspect | Details |
---|---|
Definition | A PVD method where material is heated to vaporize and condense on a substrate. |
Key Components | Evaporation source, heating mechanism, vacuum chamber, substrate holder. |
Applications | Electronics (OLEDs, solar cells), packaging, aerospace, industrial uses. |
Advantages | High purity, precision, versatility. |
Comparison with Others | Differs from sputtering (ionized gas) and CVD (chemical reactions). |
Buyer Considerations | Material compatibility, vacuum quality, scalability, maintenance. |
Discover how thermal evaporation can enhance your thin film processes—contact our experts today!