Thin film coatings are essential in various industries, including electronics, optics, and energy, due to their ability to provide precise control over material properties. These coatings can be categorized based on their deposition methods, properties, and applications. Common deposition techniques include physical vapor deposition (PVD), chemical vapor deposition (CVD), spin coating, and atomic layer deposition (ALD). Thin films are broadly classified into optical, electrical, magnetic, chemical, mechanical, and thermal types, each serving specific functions such as reflective coatings, semiconductor devices, memory disks, corrosion resistance, and thermal insulation. Additionally, thin film coating systems vary in scale, from large factory systems for high-volume production to small laboratory systems for experimental purposes.
Key Points Explained:
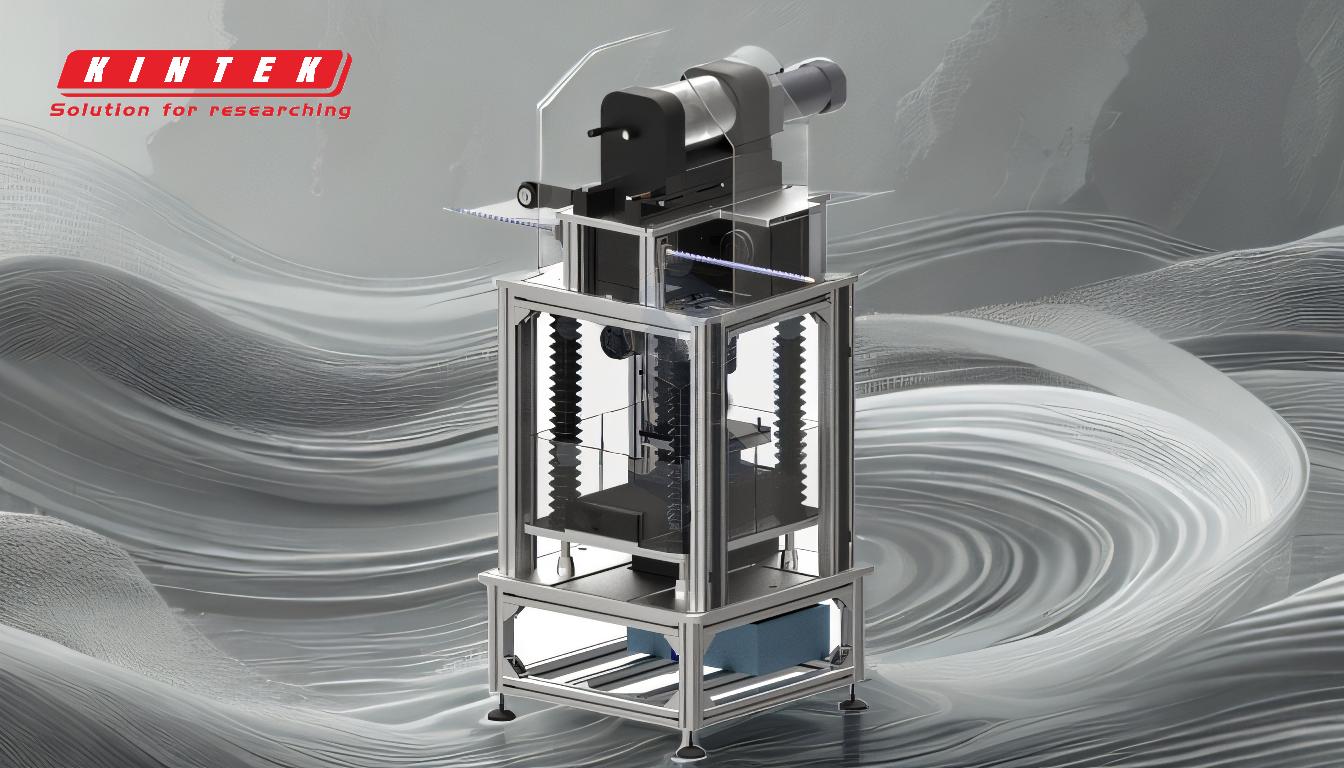
-
Deposition Methods:
-
Physical Vapor Deposition (PVD): Involves vaporizing a solid material in a vacuum and depositing it onto a substrate. Techniques include:
- Evaporation: Uses thermal energy (e.g., electron beam) to vaporize the material.
- Sputtering: Bombards a target material with ions to eject atoms, which then deposit onto the substrate.
- Chemical Vapor Deposition (CVD): Relies on chemical reactions to produce high-purity thin films. Precursor gases react on the substrate surface to form the film.
- Atomic Layer Deposition (ALD): A precise method that deposits films one atomic layer at a time, ensuring excellent thickness control and uniformity.
- Spin Coating: A liquid precursor is applied to a substrate, which is then spun at high speeds to create a uniform thin film.
- Drop Casting and Oil Bathing: Simple methods where a solution is dropped or immersed onto a substrate, often used for experimental purposes.
-
Physical Vapor Deposition (PVD): Involves vaporizing a solid material in a vacuum and depositing it onto a substrate. Techniques include:
-
Types of Thin Films:
-
Optical Thin Films: Used in applications requiring light manipulation, such as:
- Reflective and anti-reflective coatings.
- Solar cells and optical detector arrays.
- Waveguides and monitors.
-
Electrical/Electronic Thin Films: Essential for electronic devices, including:
- Insulators, conductors, and semiconductor devices.
- Integrated circuits and piezoelectric drives.
- Magnetic Thin Films: Used in data storage, such as memory disks.
- Chemical Thin Films: Provide resistance to corrosion, oxidation, and diffusion, and are used in gas and liquid sensors.
-
Mechanical Thin Films: Enhance surface properties, such as:
- Tribological coatings for abrasion resistance.
- Increased hardness and adhesion.
- Micro-mechanical applications.
-
Thermal Thin Films: Used for thermal management, including:
- Insulation layers.
- Heat sinks for dissipating heat.
-
Optical Thin Films: Used in applications requiring light manipulation, such as:
-
Applications of Thin Films:
- Optical Applications: Improve the performance of lenses, mirrors, and displays.
- Electronic Applications: Enable the miniaturization and functionality of devices like transistors and sensors.
- Energy Applications: Used in solar panels and energy storage systems.
- Industrial Applications: Provide protective coatings for tools and machinery.
- Biomedical Applications: Used in sensors and implants due to their biocompatibility and precision.
-
Thin Film Coating Systems:
- Batch Systems: Designed for high-throughput production, capable of processing multiple wafers simultaneously in a single chamber.
- Cluster Tools: Use multiple chambers for different processes, allowing for sequential processing of single wafers.
- Factory Systems: Large-scale systems for high-volume manufacturing, often integrated into production lines.
- Laboratory Systems: Compact and versatile, ideal for research and development or low-volume experimental work.
-
Advantages of Thin Film Coatings:
- Precision: Ability to control thickness and composition at the atomic level.
- Versatility: Suitable for a wide range of materials and applications.
- Customization: Tailored to meet specific functional requirements, such as optical, electrical, or mechanical properties.
- Efficiency: Enhances the performance and lifespan of components, reducing maintenance and replacement costs.
By understanding the types of thin film coatings, their deposition methods, and their applications, purchasers can make informed decisions to meet their specific needs, whether for industrial, electronic, or experimental purposes.
Summary Table:
Category | Key Information |
---|---|
Deposition Methods | PVD (Evaporation, Sputtering), CVD, ALD, Spin Coating, Drop Casting, Oil Bathing |
Types of Thin Films | Optical, Electrical, Magnetic, Chemical, Mechanical, Thermal |
Applications | Optics, Electronics, Energy, Industrial, Biomedical |
Coating Systems | Batch Systems, Cluster Tools, Factory Systems, Laboratory Systems |
Advantages | Precision, Versatility, Customization, Efficiency |
Discover how thin film coatings can transform your applications—contact our experts today!