Physical Vapor Deposition (PVD) and sputtering are advanced coating techniques used to deposit thin films onto various substrates. These processes are widely employed in industries such as semiconductors, optics, solar energy, and decorative coatings. The choice of substrate is critical, as it must be compatible with the deposition process and the intended application. Substrates can range from metals and alloys to plastics, ceramics, and glass, depending on the desired properties of the final product.
Key Points Explained:
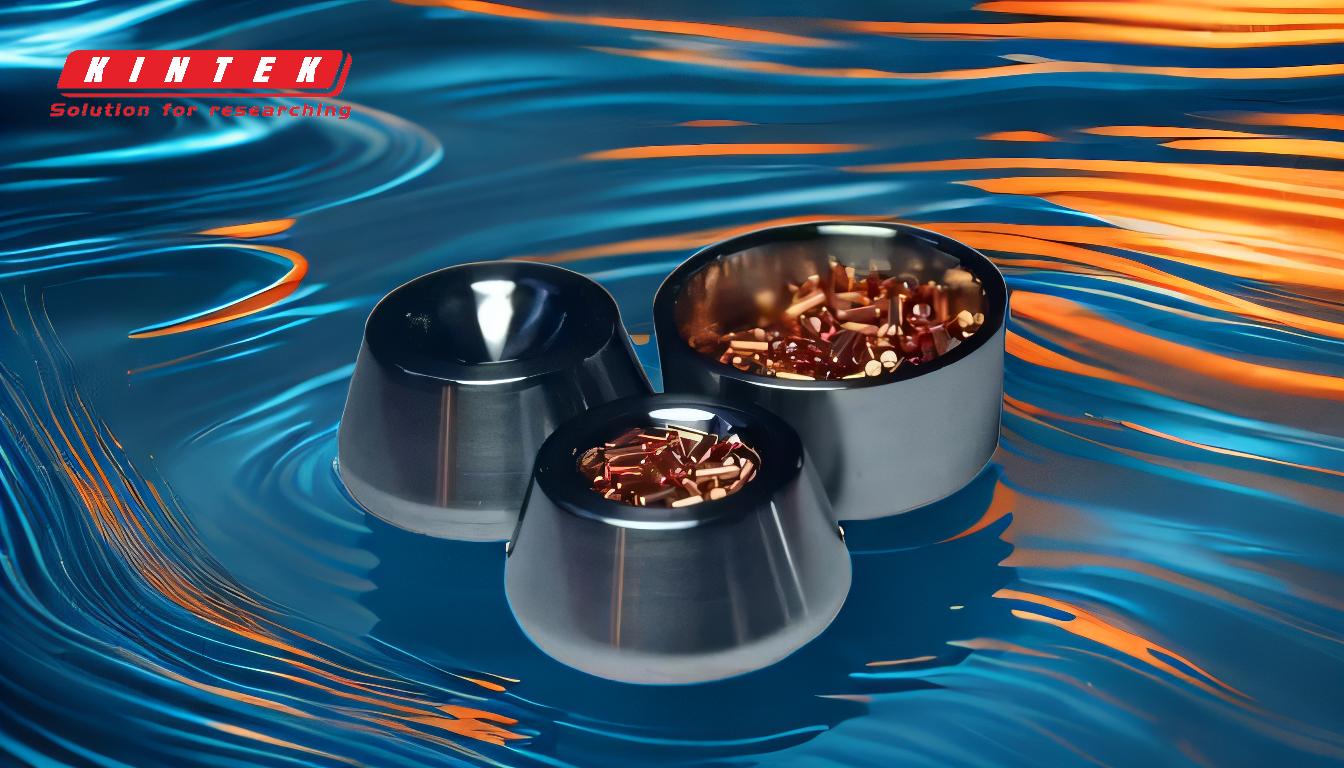
-
Semiconductor Wafers
- Semiconductor wafers, typically made of silicon, are a common substrate in PVD and sputtering processes.
- These substrates are used in the production of microelectronic devices, where thin films of metals, oxides, or nitrides are deposited to create circuits, transistors, and other components.
- The high precision and uniformity of PVD and sputtering make them ideal for semiconductor manufacturing.
-
Solar Cells
- Solar cells often use substrates like silicon, glass, or flexible polymers.
- PVD and sputtering are used to deposit conductive or protective layers, such as transparent conductive oxides (e.g., indium tin oxide) or anti-reflective coatings.
- These coatings enhance the efficiency and durability of solar panels.
-
Optical Components
- Glass and optical-grade plastics are frequently used as substrates for optical components like lenses, mirrors, and filters.
- PVD and sputtering can deposit anti-reflective, reflective, or protective coatings to improve optical performance.
- Examples include coatings for eyeglasses, camera lenses, and laser optics.
-
Plastics
- Plastics such as ABS, polycarbonate, and PC-ABS are lightweight and cost-effective substrates for decorative or functional coatings.
- PVD and sputtering can deposit metallic or colored coatings for aesthetic purposes, as well as scratch-resistant or conductive layers for functional applications.
- These substrates are commonly used in consumer electronics, automotive parts, and packaging.
-
Metals and Alloys
- Common metals like steel, aluminum, and titanium, as well as their alloys, are widely used as substrates.
- PVD and sputtering can deposit wear-resistant, corrosion-resistant, or decorative coatings on these materials.
- Applications include cutting tools, medical devices, and architectural components.
-
Ceramics
- Ceramics are used as substrates in high-temperature or wear-resistant applications.
- PVD and sputtering can deposit coatings to enhance their thermal, electrical, or mechanical properties.
- Examples include coatings for cutting tools, engine components, and electronic insulators.
-
Glass
- Glass substrates are used in applications like mirrors, windows, and displays.
- PVD and sputtering can deposit reflective, anti-reflective, or conductive coatings.
- These coatings are essential for energy-efficient windows, touchscreens, and automotive glass.
-
Flexible Substrates
- Flexible substrates like polymers or thin metal foils are used in flexible electronics, wearable devices, and packaging.
- PVD and sputtering can deposit thin, uniform coatings that maintain flexibility while providing functionality.
- Examples include flexible displays, sensors, and RFID tags.
-
Compatibility Considerations
- The substrate must withstand the vacuum environment and temperatures involved in PVD and sputtering.
- Surface preparation, such as cleaning and pre-treatment, is crucial to ensure good adhesion of the coating.
- The thermal expansion coefficient and mechanical properties of the substrate must be compatible with the deposited material to avoid delamination or cracking.
-
Multilayered Coatings
- Some applications require multilayered coatings, where different materials are deposited in sequence.
- Substrates must be chosen to support the deposition of multiple layers without compromising performance.
- Examples include optical filters, semiconductor devices, and protective coatings.
In summary, the choice of substrate in PVD and sputtering depends on the application, desired properties, and compatibility with the deposition process. From semiconductors and solar cells to plastics and ceramics, a wide range of materials can be used as substrates to achieve functional or decorative coatings. Understanding the properties and requirements of both the substrate and the coating material is essential for successful deposition.
Summary Table:
Substrate Type | Key Applications | Coating Benefits |
---|---|---|
Semiconductor Wafers | Microelectronic devices, circuits, transistors | High precision, uniformity, and functionality |
Solar Cells | Solar panels, energy-efficient coatings | Enhanced efficiency and durability |
Optical Components | Lenses, mirrors, filters, eyeglasses, camera lenses | Anti-reflective, reflective, and protective coatings |
Plastics | Consumer electronics, automotive parts, packaging | Aesthetic, scratch-resistant, and conductive coatings |
Metals and Alloys | Cutting tools, medical devices, architectural components | Wear-resistant, corrosion-resistant, and decorative coatings |
Ceramics | Cutting tools, engine components, electronic insulators | Enhanced thermal, electrical, and mechanical properties |
Glass | Mirrors, windows, displays, automotive glass | Reflective, anti-reflective, and conductive coatings |
Flexible Substrates | Flexible electronics, wearable devices, RFID tags | Thin, uniform, and flexible coatings |
Compatibility Factors | Vacuum environment, temperature, surface preparation, thermal expansion coefficient | Ensures adhesion and prevents delamination or cracking |
Multilayered Coatings | Optical filters, semiconductor devices, protective coatings | Supports multiple layers for advanced functionality |
Ready to optimize your PVD and sputtering processes? Contact our experts today for tailored solutions!