Corrosion prevention is a critical concern in various industries, and coatings play a significant role in protecting materials from degradation. The choice of coating depends on the environment, the material being protected, and the specific type of corrosion being addressed. Common coatings include paints, polymers, metallic coatings, and ceramic coatings, each offering unique advantages. For instance, zinc coatings are widely used for steel due to their sacrificial protection, while epoxy coatings are favored for their chemical resistance. Advanced coatings like nanocoatings and self-healing coatings are also gaining traction for their superior performance and durability. Understanding the specific requirements and environmental conditions is essential for selecting the most effective corrosion-preventing coating.
Key Points Explained:
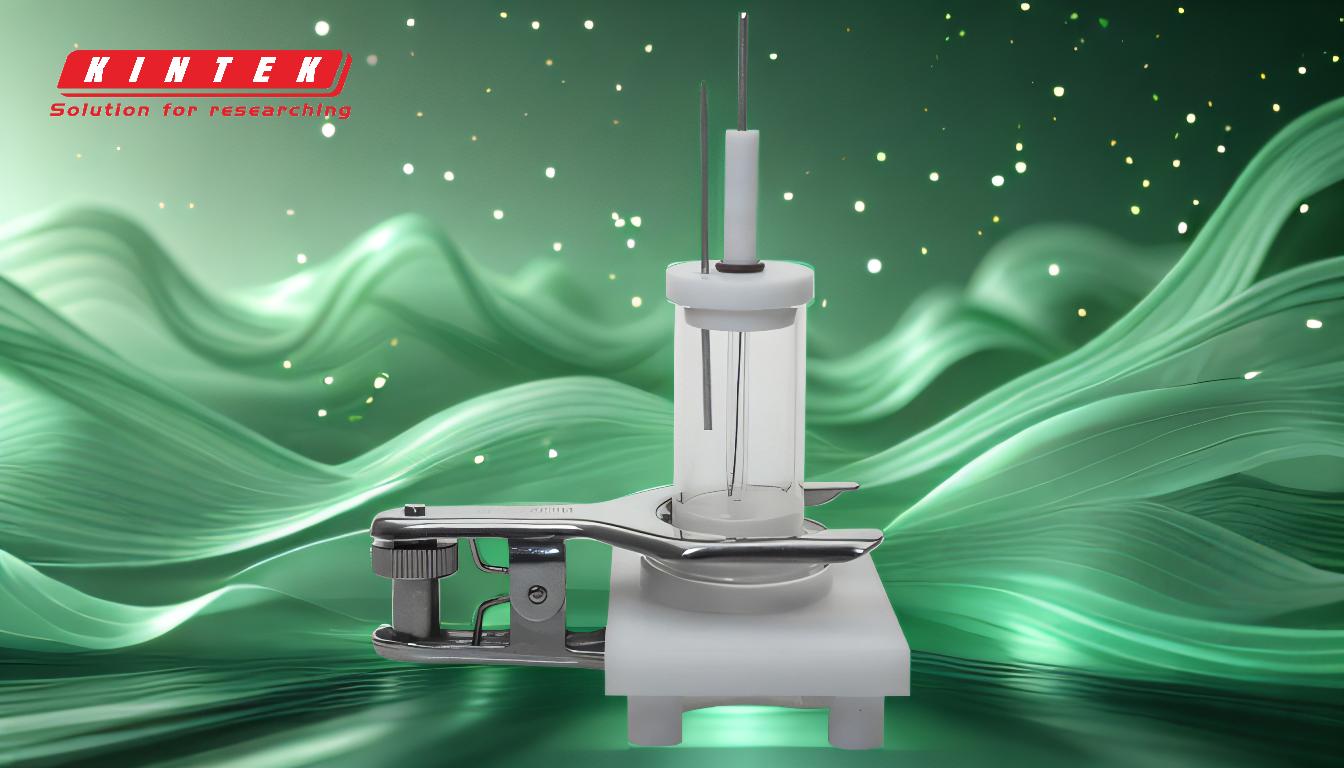
-
Types of Corrosion-Preventing Coatings:
- Paints and Polymers: These are the most common types of coatings used for corrosion prevention. They form a barrier between the material and the corrosive environment. Epoxy, polyurethane, and acrylic coatings are popular choices due to their excellent adhesion and resistance to chemicals and moisture.
- Metallic Coatings: These coatings, such as zinc, aluminum, and chromium, provide sacrificial protection. Zinc coatings, for example, corrode preferentially to the underlying steel, thereby protecting it. Galvanization is a common method of applying zinc coatings.
- Ceramic Coatings: These coatings are used in high-temperature environments where other coatings might fail. They offer excellent resistance to oxidation and thermal degradation.
- Nanocoatings: These advanced coatings utilize nanotechnology to provide superior protection. They can be engineered to have self-cleaning, anti-fouling, and even self-healing properties, making them highly effective in preventing corrosion.
-
Mechanisms of Corrosion Prevention:
- Barrier Protection: Coatings act as a physical barrier, preventing corrosive agents like oxygen and moisture from reaching the underlying material. This is the most straightforward mechanism and is common in paints and polymer coatings.
- Sacrificial Protection: In this mechanism, the coating material corrodes in place of the substrate. Zinc coatings on steel are a classic example, where the zinc sacrifices itself to protect the steel.
- Inhibitive Protection: Some coatings contain corrosion inhibitors that react with the metal surface to form a protective layer. This layer prevents further corrosion by blocking the electrochemical reactions that cause it.
- Cathodic Protection: This method involves making the metal surface the cathode of an electrochemical cell, thereby preventing corrosion. It is often used in conjunction with coatings, especially in marine environments.
-
Selection Criteria for Coatings:
- Environmental Conditions: The choice of coating depends heavily on the environment in which the material will be used. For example, marine environments require coatings with high resistance to saltwater, while industrial environments might need coatings that can withstand chemical exposure.
- Material Compatibility: The coating must be compatible with the substrate material. For instance, certain coatings might adhere well to steel but not to aluminum.
- Application Method: The method of applying the coating (e.g., spraying, dipping, electroplating) can affect its effectiveness. Some coatings are better suited to specific application methods.
- Cost and Durability: The cost of the coating and its expected lifespan are also important factors. While some coatings might be more expensive upfront, their durability and low maintenance requirements can make them more cost-effective in the long run.
-
Advanced and Emerging Coating Technologies:
- Self-Healing Coatings: These coatings can automatically repair damage, such as scratches or cracks, thereby maintaining their protective properties. This is achieved through the incorporation of microcapsules or other mechanisms that release healing agents when damage occurs.
- Nanocoatings: These coatings are engineered at the nanoscale to provide enhanced properties, such as improved adhesion, hardness, and resistance to corrosion. They can also be designed to have multifunctional properties, such as UV resistance and antimicrobial effects.
- Hybrid Coatings: Combining different types of coatings can result in hybrid coatings that offer the benefits of multiple protection mechanisms. For example, a hybrid coating might combine the barrier protection of a polymer with the sacrificial protection of a metallic coating.
-
Maintenance and Inspection:
- Regular Inspection: Even the best coatings can degrade over time, so regular inspection is crucial to ensure ongoing protection. This includes checking for signs of wear, damage, or corrosion breakthrough.
- Maintenance Practices: Proper maintenance, such as cleaning and reapplying coatings as needed, can extend the lifespan of the protective layer. This is especially important in harsh environments where coatings are subjected to extreme conditions.
- Monitoring Technologies: Advanced monitoring technologies, such as sensors and drones, can be used to inspect coatings in hard-to-reach areas or in large-scale applications like pipelines and offshore structures.
In conclusion, preventing corrosion through coatings involves a combination of selecting the right type of coating, understanding the mechanisms of protection, and implementing proper maintenance practices. With advancements in coating technologies, there are now more options than ever to protect materials from corrosion, ensuring their longevity and performance in various environments.
Summary Table:
Coating Type | Key Features | Best Use Cases |
---|---|---|
Paints and Polymers | Barrier protection, chemical resistance, excellent adhesion | General-purpose, chemical environments |
Metallic Coatings | Sacrificial protection (e.g., zinc for steel), durable | Marine, industrial environments |
Ceramic Coatings | High-temperature resistance, oxidation protection | High-heat applications |
Nanocoatings | Self-healing, anti-fouling, superior adhesion and hardness | Advanced, multifunctional applications |
Need the right corrosion-preventing coating for your project? Contact our experts today for tailored solutions!