PVD (Physical Vapor Deposition) coatings offer a vast array of colors, ranging from metallic tones like gold, rose gold, and bronze to non-metallic shades such as black, blue, green, and red. The specific color achieved depends on the material being vaporized (target) and the conditions of the deposition process, including the mixture of reactive gases used. These coatings can be applied to various substrates, including metals and plastics, and are available in polished, satin, or matte finishes. The versatility of PVD coatings allows for precise color matching and customization to meet specific design or functional requirements.
Key Points Explained:
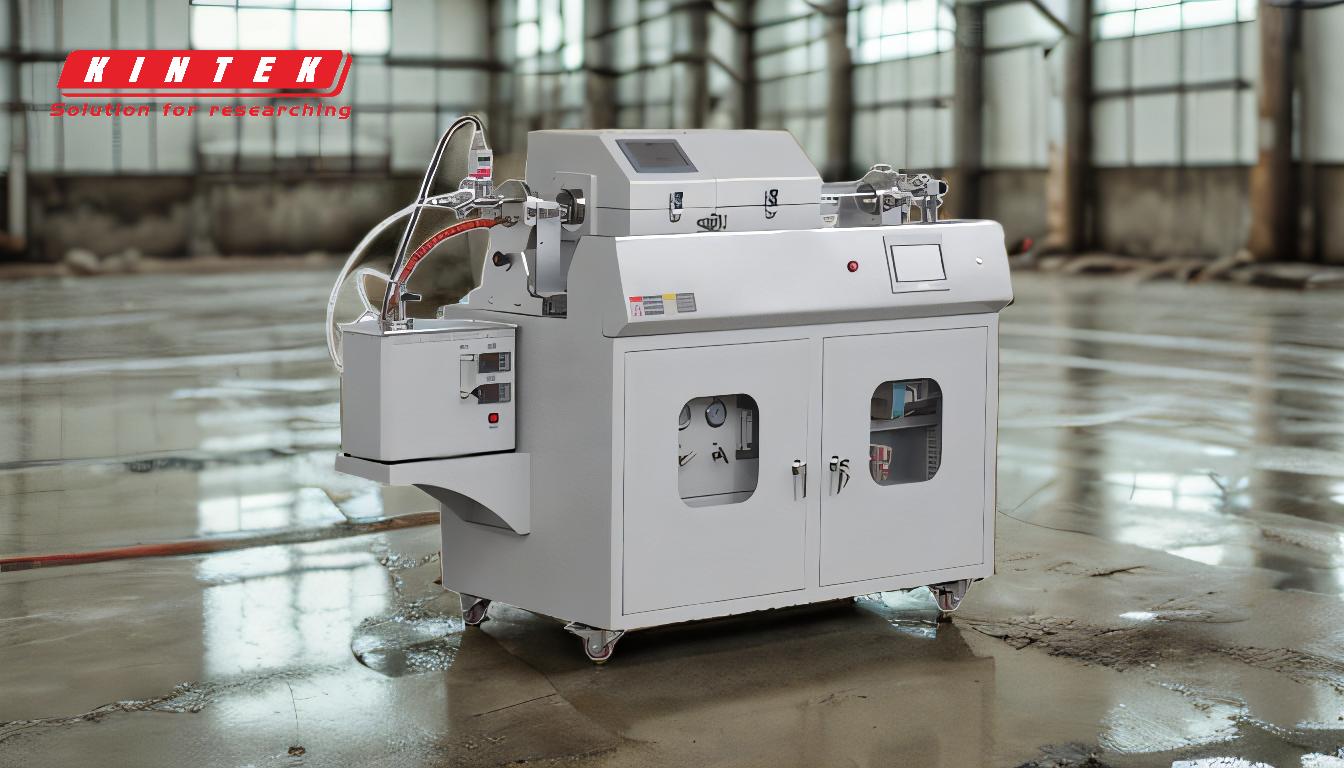
-
Wide Range of Colors:
- PVD coatings can produce a broad spectrum of colors, including:
- Metallic Colors: Gold, rose gold, silver, chrome, brass, nickel, copper, and bronze.
- Non-Metallic Colors: Black, blue, green, red, purple, turquoise, graphite, and smoky tones.
- These colors are achieved by varying the materials used in the PVD process and the conditions under which the deposition occurs.
- PVD coatings can produce a broad spectrum of colors, including:
-
Factors Influencing Color:
- Target Material: The type of metal or material being vaporized (e.g., titanium, zirconium, or chromium) significantly impacts the final color.
- Reactive Gases: The mixture of gases (e.g., nitrogen, oxygen, or acetylene) introduced during the deposition process can alter the color by forming different compounds with the vaporized material.
- Deposition Conditions: Parameters such as temperature, pressure, and deposition rate also play a role in determining the final color and finish.
-
Finish Options:
- PVD coatings are available in various finishes, including:
- Polished: High-gloss, reflective surfaces.
- Satin: Semi-matte, with a soft sheen.
- Matte: Non-reflective, with a flat appearance.
- The choice of finish can further enhance the aesthetic appeal and functional properties of the coating.
- PVD coatings are available in various finishes, including:
-
Applications and Substrates:
- PVD coatings can be applied to a wide range of substrates, including:
- Metals: Stainless steel, copper, zinc alloy, and titanium.
- Plastics: Certain plastics can also be coated, provided they can withstand the deposition process.
- This versatility allows for uniform color matching across different materials, ensuring a cohesive look for products with multiple components.
- PVD coatings can be applied to a wide range of substrates, including:
-
Customization and Matching:
- PVD coatings can be customized to match specific color requirements, even for critical applications. This may involve:
- Using a combination of PVD layers and colored protective coatings to achieve precise color matching.
- Adjusting the deposition process parameters to fine-tune the color and finish.
- This level of customization is particularly valuable in industries such as jewelry, automotive, and consumer electronics, where color consistency and aesthetics are crucial.
- PVD coatings can be customized to match specific color requirements, even for critical applications. This may involve:
-
Advantages of PVD Coatings:
- Durability: PVD coatings are highly resistant to wear, corrosion, and fading, making them suitable for long-lasting applications.
- Aesthetic Appeal: The wide range of colors and finishes available allows for creative and high-end designs.
- Cost-Effectiveness: Compared to using pure metals, PVD coatings offer a more affordable way to achieve similar aesthetic and functional properties.
In summary, PVD coatings provide an extensive palette of colors and finishes, making them a versatile and cost-effective solution for a wide range of applications. The ability to customize and match colors precisely, combined with the durability and aesthetic appeal of PVD coatings, makes them a popular choice in various industries.
Summary Table:
Aspect | Details |
---|---|
Color Range | Metallic: Gold, rose gold, silver, chrome, brass, nickel, copper, bronze. |
Non-Metallic: Black, blue, green, red, purple, turquoise, graphite, smoky. | |
Influencing Factors | Target material, reactive gases, deposition conditions (temp, pressure). |
Finish Options | Polished, satin, matte. |
Substrates | Metals (stainless steel, copper, titanium), plastics. |
Customization | Precise color matching for design or functional needs. |
Advantages | Durable, aesthetic, cost-effective. |
Unlock the potential of PVD coatings for your project—contact us today to get started!