The efficiency of the pyrolysis process depends on a variety of factors, including the composition of the feedstock, operational parameters such as temperature, pressure, and residence time, and the design and control of the pyrolysis reactor. These factors influence the extent to which organic materials are degraded and converted into valuable products like gas, oil, and char. Proper management of these variables is essential to optimize the process, ensure safety, and achieve the desired end products.
Key Points Explained:
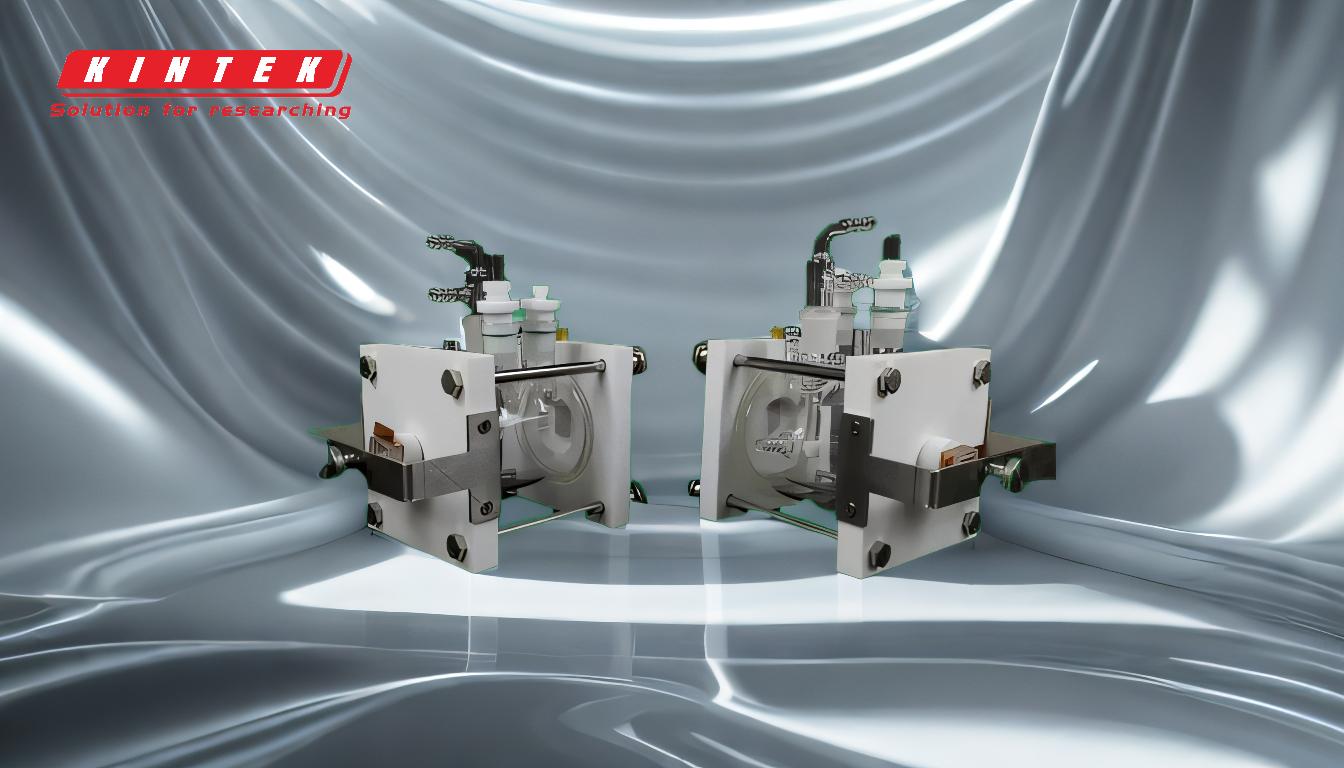
-
Feedstock Composition:
- The type and composition of the feedstock significantly impact pyrolysis efficiency. For example:
- Organic-rich materials degrade more effectively, yielding higher gas and oil outputs.
- Inorganic components or contaminants can hinder the process, reducing efficiency.
- Moisture content in the feedstock also plays a critical role. High moisture levels require additional energy for evaporation, reducing overall efficiency.
- The type and composition of the feedstock significantly impact pyrolysis efficiency. For example:
-
Temperature:
- Temperature is a critical operational parameter in pyrolysis. It directly influences the rate and extent of thermal degradation:
- Higher temperatures generally increase the conversion of feedstock into gas and oil but may also lead to excessive cracking, reducing the quality of the end products.
- Lower temperatures may result in incomplete pyrolysis, leaving behind more solid residues (char).
- Optimal temperature ranges must be determined based on the specific feedstock and desired outputs.
- Temperature is a critical operational parameter in pyrolysis. It directly influences the rate and extent of thermal degradation:
-
Residence Time:
- The duration that the feedstock remains in the pyrolysis reactor (residence time) affects the completeness of the reaction:
- Longer residence times allow for more thorough degradation of organic materials, enhancing gas and oil yields.
- However, excessively long residence times can lead to over-cracking, reducing the quality of the end products.
- Shorter residence times may result in incomplete pyrolysis, leaving behind unconverted feedstock.
- The duration that the feedstock remains in the pyrolysis reactor (residence time) affects the completeness of the reaction:
-
Pressure:
- The pressure inside the pyrolysis reactor influences the reaction kinetics and product distribution:
- Higher pressures can favor the formation of liquid products (bio-oil) over gaseous products.
- Lower pressures may enhance gas production but could also lead to incomplete pyrolysis.
- Pressure control is essential to achieve the desired balance between gas, oil, and char yields.
- The pressure inside the pyrolysis reactor influences the reaction kinetics and product distribution:
-
Reactor Design and Control:
- The design of the pyrolysis reactor and the control systems used to manage operational parameters are crucial for efficiency:
- Reactors must be designed to ensure uniform heating and proper mixing of the feedstock.
- Advanced control systems can optimize temperature, pressure, and residence time in real-time, improving overall efficiency.
- Proper maintenance and operation of the reactor are essential to prevent downtime and ensure consistent performance.
- The design of the pyrolysis reactor and the control systems used to manage operational parameters are crucial for efficiency:
-
Feedstock Preparation:
- Pre-treatment of the feedstock, such as drying or size reduction, can enhance pyrolysis efficiency:
- Reducing moisture content minimizes energy losses due to evaporation.
- Smaller particle sizes improve heat transfer and reaction rates, leading to more efficient pyrolysis.
- Pre-treatment of the feedstock, such as drying or size reduction, can enhance pyrolysis efficiency:
-
End Product Quality:
- The efficiency of pyrolysis is also judged by the quality and usability of the end products:
- High-quality bio-oil and syngas are more valuable and easier to utilize in downstream applications.
- The presence of impurities or incomplete conversion can reduce the market value of the end products.
- The efficiency of pyrolysis is also judged by the quality and usability of the end products:
By carefully managing these factors, operators can optimize the pyrolysis process to maximize efficiency, safety, and the quality of the end products. This requires a thorough understanding of the feedstock properties, precise control of operational parameters, and regular maintenance of the pyrolysis equipment.
Summary Table:
Factor | Impact on Pyrolysis Efficiency |
---|---|
Feedstock Composition | Organic-rich materials yield more gas/oil; inorganic components and moisture reduce efficiency. |
Temperature | Higher temps increase gas/oil production; lower temps leave more char. |
Residence Time | Longer times enhance degradation; excessively long times reduce product quality. |
Pressure | Higher pressures favor bio-oil; lower pressures enhance gas production. |
Reactor Design & Control | Uniform heating, advanced controls, and maintenance ensure consistent performance. |
Feedstock Preparation | Drying and size reduction improve heat transfer and reaction rates. |
End Product Quality | High-quality bio-oil and syngas are more valuable; impurities reduce market value. |
Ready to optimize your pyrolysis process? Contact our experts today for tailored solutions!