Plastic pyrolysis is a thermal decomposition process that breaks down plastic waste into valuable byproducts in the absence of oxygen. The primary outputs of this process are pyrolysis oil, carbon black, and syngas, with potential additional byproducts such as wastewater depending on the moisture content of the input material. These byproducts have diverse applications, including fuel production, soil amendment, energy generation, and industrial use. The process not only helps in waste management but also adds significant value to plastic waste by converting it into usable resources.
Key Points Explained:
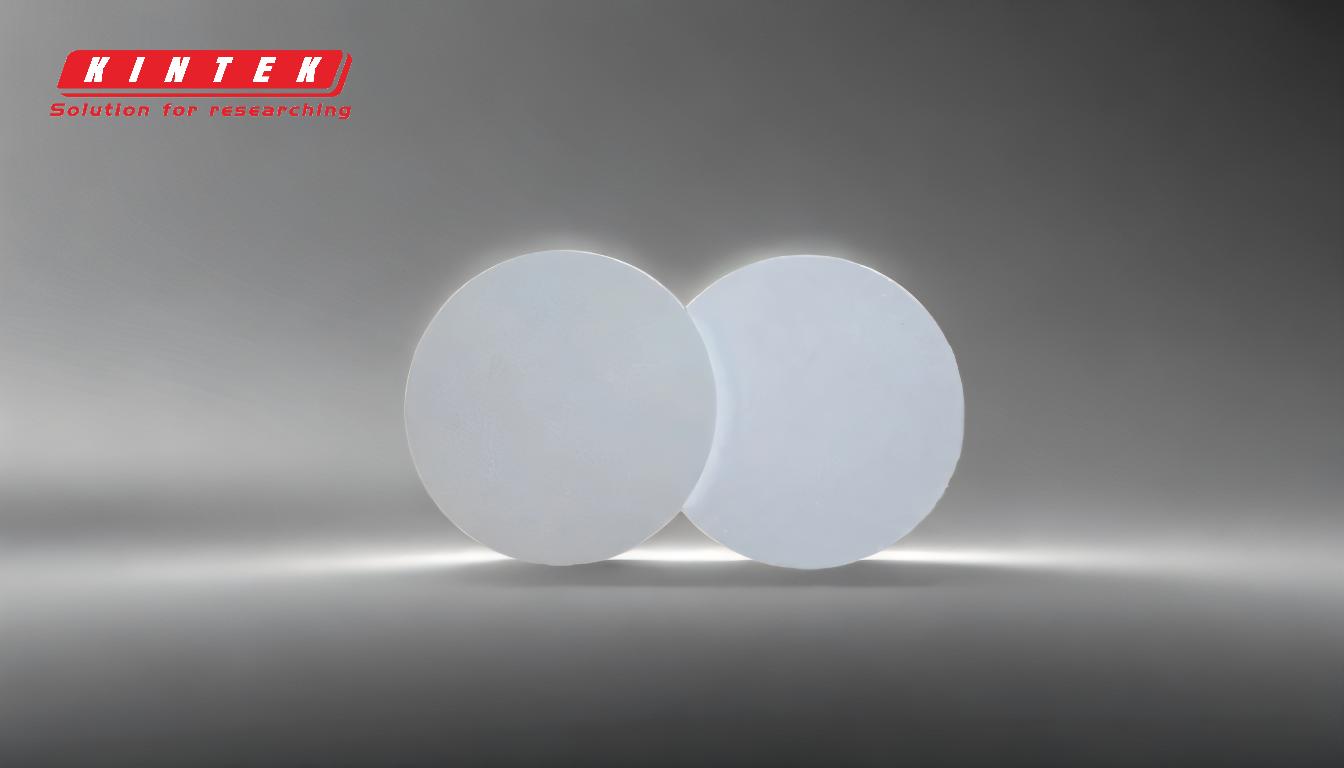
-
Primary Products of Plastic Pyrolysis:
-
Pyrolysis Oil:
- Typically constitutes 30-80% of the output, depending on the type of plastic and pyrolysis conditions.
- Can be refined into diesel or used as a fuel in industrial applications.
-
Carbon Black:
- Makes up 20-30% of the output.
- Used as a reinforcing agent in rubber products, as a pigment, or in the production of tires.
-
Syngas:
- Comprises 10-20% of the output.
- A mixture of combustible gases (e.g., hydrogen, methane, carbon monoxide) that can be used for energy generation or as a chemical feedstock.
-
Pyrolysis Oil:
-
Secondary Byproducts:
-
Wastewater:
- Generated if the plastic waste contains moisture.
- Requires proper treatment before disposal or reuse.
-
Ash:
- A mineral-based residue that may require containment or further processing.
- Can be used in construction materials or as a filler in certain industrial applications.
-
Wastewater:
-
Applications of Pyrolysis Byproducts:
-
Pyrolysis Oil:
- Can be used directly as a fuel or further refined into higher-value products like diesel.
- Suitable for industrial boilers, furnaces, and power generation.
-
Carbon Black:
- Widely used in the rubber industry for tire manufacturing.
- Also used as a pigment in inks, paints, and plastics.
-
Syngas:
- Utilized for electricity generation or as a feedstock for chemical synthesis.
- Can replace natural gas in certain applications.
-
Biochar (if applicable):
- Used as a soil amendment to improve soil fertility and sequester carbon.
- Can serve as a catalyst support or activated carbon in industrial processes.
-
Pyrolysis Oil:
-
Environmental and Economic Benefits:
-
Waste Reduction:
- Converts non-recyclable plastic waste into valuable resources, reducing landfill dependency.
-
Energy Recovery:
- Provides an alternative energy source, reducing reliance on fossil fuels.
-
Carbon Sequestration:
- Biochar and carbon black can help sequester carbon, mitigating climate change.
-
Economic Value:
- Creates new revenue streams from waste materials, supporting circular economy initiatives.
-
Waste Reduction:
-
Challenges and Considerations:
-
Process Optimization:
- The yield and quality of byproducts depend on factors like temperature, heating rate, and feedstock composition.
-
Wastewater Treatment:
- Requires additional infrastructure and costs for proper management.
-
Regulatory Compliance:
- Pyrolysis plants must adhere to environmental regulations to minimize emissions and ensure safe handling of byproducts.
-
Market Demand:
- The economic viability of pyrolysis depends on the demand for its byproducts, which can fluctuate based on market conditions.
-
Process Optimization:
-
Comparison with Other Pyrolysis Processes:
-
Rubber Pyrolysis:
- Produces similar byproducts (oil, carbon black, and gas) but may yield more steel wire from waste tires.
-
Biomass Pyrolysis:
- Generates biochar, non-condensable gases, and wood acid, with different applications compared to plastic pyrolysis.
-
General Pyrolysis:
- All pyrolysis processes aim to convert waste into valuable resources, but the specific byproducts and their uses vary based on the feedstock.
-
Rubber Pyrolysis:
In summary, plastic pyrolysis transforms plastic waste into valuable resources like pyrolysis oil, carbon black, and syngas, offering environmental and economic benefits. However, the process requires careful optimization and management to maximize efficiency and comply with regulations. The byproducts have diverse applications, making pyrolysis a key technology in waste management and resource recovery.
Summary Table:
Byproduct | Output (%) | Applications |
---|---|---|
Pyrolysis Oil | 30-80 | Fuel for industrial boilers, refined into diesel, power generation |
Carbon Black | 20-30 | Rubber reinforcement, tire manufacturing, pigment in inks and paints |
Syngas | 10-20 | Energy generation, chemical feedstock, replacement for natural gas |
Wastewater | Variable | Requires treatment; potential reuse after processing |
Ash | Minimal | Construction materials, industrial filler |
Transform plastic waste into valuable resources—contact us today to learn more about plastic pyrolysis solutions!