A direct current sintering (DCS) system is an advanced sintering technology that utilizes a continuous direct current to heat a conductive graphite die assembly while simultaneously applying pressure. This system leverages joule heating, where electrical resistance within the die generates heat, enabling rapid heating rates (up to 600°C per minute) and achieving high temperatures (over 1500°C) in minutes. Unlike traditional sintering methods, DCS combines heat and pressure in a single step, making it highly efficient for densifying powdered materials such as ceramics, metals, and sintered plastics. The process avoids liquefaction by operating below the material's melting point, ensuring particle bonding through solid-state diffusion. DCS is particularly valued for its speed, precision, and ability to produce high-density, structurally robust components.
Key Points Explained:
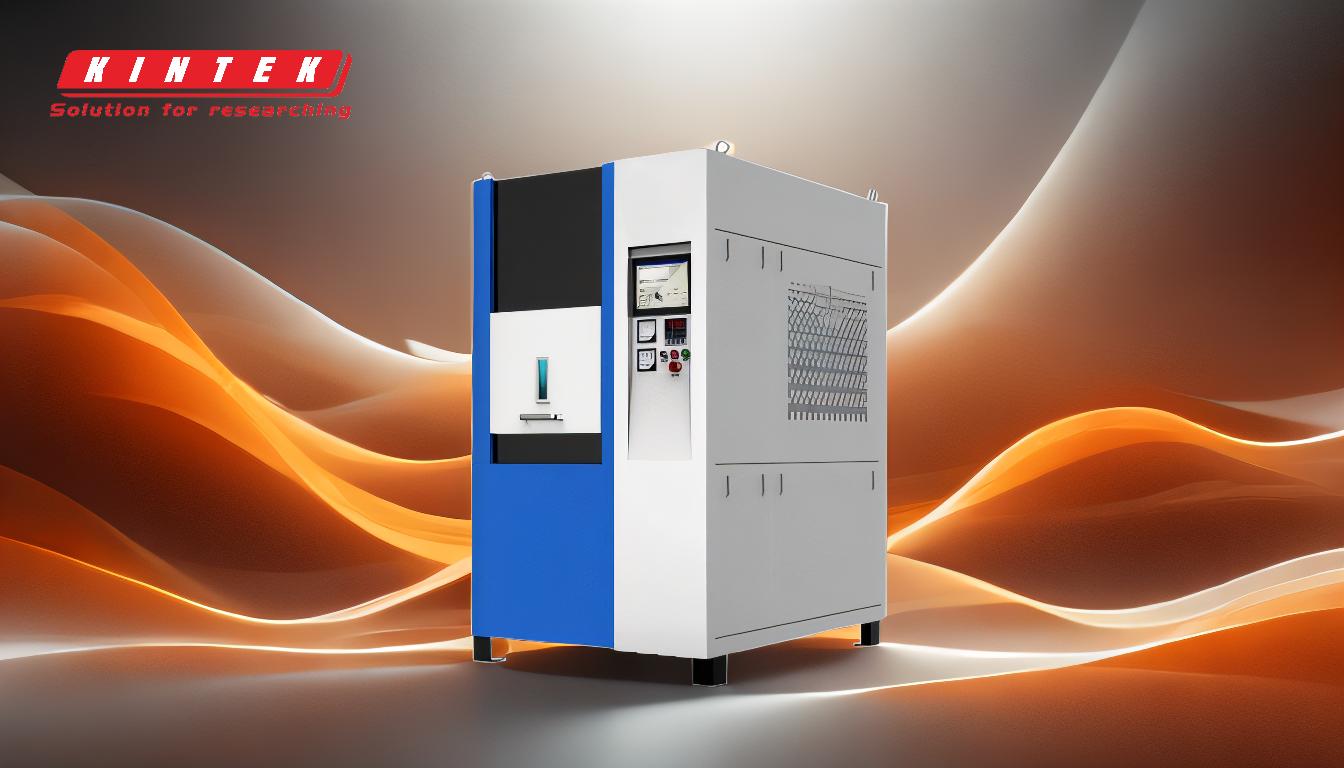
-
Definition of Direct Current Sintering (DCS):
- DCS is a sintering method that uses a continuous direct current to heat a conductive graphite die assembly while applying pressure. This unique combination of heat and pressure enables rapid densification of powdered materials.
-
Mechanism of Heating:
- The system relies on joule heating, where electrical resistance within the graphite die generates heat. This method allows for extremely fast heating rates (up to 600°C per minute) and can achieve temperatures exceeding 1500°C in just a few minutes.
-
Simultaneous Application of Heat and Pressure:
- Unlike traditional sintering processes, which may separate heating and pressing into distinct steps, DCS integrates both actions simultaneously. This integration enhances the efficiency and effectiveness of the sintering process.
-
Materials Suitable for DCS:
- DCS is versatile and can be used for a wide range of materials, including ceramics, metals, and sintered plastics. The process is particularly effective for materials that require high-density, structurally robust components.
-
Avoidance of Liquefaction:
- The process operates below the melting point of the material, ensuring that the particles bond through solid-state diffusion without liquefying. This characteristic preserves the material's properties and structural integrity.
-
Advantages of DCS:
- Speed: Rapid heating rates significantly reduce processing time.
- Precision: Controlled heating and pressure application ensure consistent results.
- Density: Produces high-density components with minimal porosity.
- Versatility: Suitable for a wide range of materials and applications.
-
Applications of DCS:
- DCS is widely used in industries requiring high-performance materials, such as aerospace, automotive, and electronics. It is particularly beneficial for manufacturing complex shapes and components with stringent mechanical and thermal properties.
-
Comparison with Traditional Sintering:
- Traditional sintering methods often involve separate heating and pressing stages, which can be time-consuming and less efficient. DCS streamlines the process by combining these stages, resulting in faster production times and higher-quality outputs.
By understanding these key points, equipment and consumable purchasers can better appreciate the advantages of direct current sintering systems and make informed decisions when selecting sintering technologies for their specific needs.
Summary Table:
Key Feature | Description |
---|---|
Heating Mechanism | Joule heating via electrical resistance in graphite die. |
Heating Rate | Up to 600°C per minute. |
Max Temperature | Exceeds 1500°C in minutes. |
Materials Supported | Ceramics, metals, sintered plastics. |
Key Advantages | Speed, precision, high-density outputs, versatility. |
Applications | Aerospace, automotive, electronics, and high-performance material manufacturing. |
Transform your material processing with a DCS system—contact us today to learn more!