A rotary kiln is a large, cylindrical, slightly inclined industrial equipment used to process materials at high temperatures. It rotates slowly around its longitudinal axis, allowing materials to move from the higher end (feed end) to the lower end (discharge end) while being heated. The kiln is designed to facilitate chemical reactions or physical changes in materials, such as calcination, sintering, or thermal decomposition. It operates by exposing the material to hot gases, which can flow in the same direction (co-current) or opposite direction (counter-current) to the material. Rotary kilns are widely used in industries like cement production, metallurgy, and waste treatment due to their ability to handle high temperatures and continuous processing.
Key Points Explained:
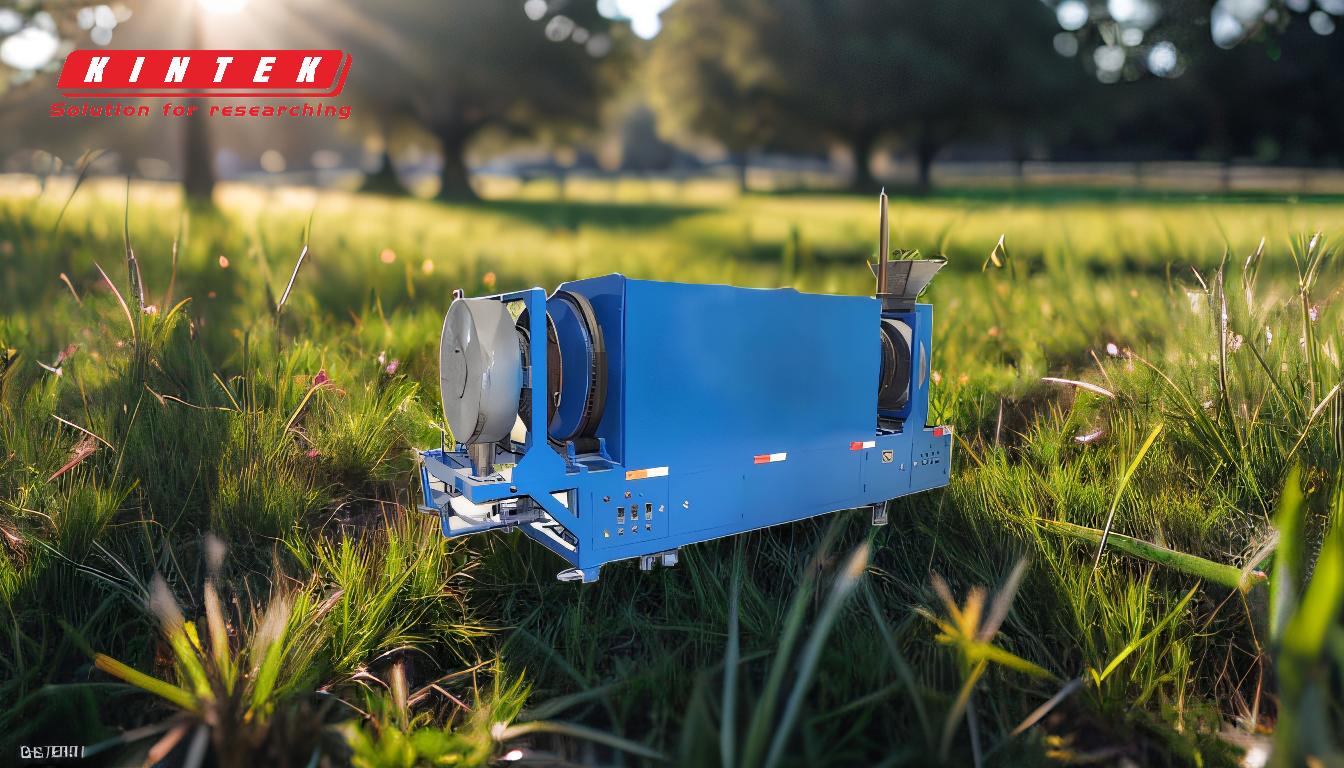
-
Basic Structure and Function:
- A rotary kiln is a cylindrical vessel, slightly inclined from the horizontal, that rotates slowly about its axis.
- The material is fed into the upper end and moves downward due to gravity and rotation, undergoing mixing and heating.
- Hot gases flow through the kiln, either co-currently or counter-currently, to heat the material.
-
Components of a Rotary Kiln:
- Shell: The outer cylindrical structure, often conically tapered at the ends, designed to withstand torsion and flexural stress.
- Refractory Lining: A heat-resistant lining inside the shell to protect it from high temperatures and chemical reactions.
- Support Tyres (Riding Rings) and Rollers: These support the kiln and allow it to rotate smoothly.
- Drive Gear: The mechanism that rotates the kiln, which can be a chain and sprocket, gear drive, friction drive, or direct drive assembly.
- Internal Heat Exchangers: Components that facilitate heat transfer within the kiln.
-
Working Principle:
- The kiln operates by heating solids to a specific temperature where chemical or physical changes occur.
- The material is held at the desired temperature for a precise amount of time, determined by temperature profiles based on chemical and thermal analyses.
- The rotation of the kiln ensures uniform heating and mixing of the material.
-
Gas Flow and Combustion:
- Hot gases are generated either in an external furnace or by a flame inside the kiln, projected from a burner-pipe.
- The fuel for combustion can be gas, oil, pulverized petroleum coke, or pulverized coal.
- The kiln ensures complete combustion of the fuel and effective heat transfer to the material.
-
Material Movement and Processing:
- The material moves through the kiln due to gravity and the rotation of the drum.
- The rotating drum is sealed at both ends to control the internal atmosphere and temperature, ensuring effective processing.
- The material undergoes a series of physical and chemical changes, such as drying, calcination, or sintering, to form the final product.
-
Types of Heating:
- Direct Heating: The material is heated directly by the flame or hot gases inside the kiln.
- Indirect Heating: The material is heated externally, with the heat source separated from the material by a wall or heat exchanger.
-
Applications:
- Rotary kilns are used in various industries, including:
- Cement Production: For clinker formation.
- Metallurgy: For ore reduction and metal processing.
- Waste Treatment: For incineration and recycling of hazardous materials.
- Chemical Processing: For calcination and thermal decomposition of chemicals.
- Rotary kilns are used in various industries, including:
-
Customization and Components:
- Rotary kilns are customized based on the material to be processed and the specific requirements of the application.
- Standard components include the drive assembly, riding rings, thrust rollers, trunnion wheels, discharge breeching, and product discharge area.
- The design and configuration of these components ensure efficient operation and durability.
In summary, a rotary kiln is a versatile and essential piece of equipment in many industrial processes. Its ability to handle high temperatures, continuous processing, and a wide range of materials makes it indispensable in industries such as cement production, metallurgy, and waste treatment. The combination of its structural components, working principles, and customization options ensures efficient and effective material processing.
Summary Table:
Aspect | Details |
---|---|
Structure | Cylindrical vessel, slightly inclined, rotates around its axis. |
Key Components | Shell, refractory lining, support tyres, drive gear, internal heat exchangers. |
Working Principle | Heats materials to induce chemical/physical changes, ensures uniform heating. |
Gas Flow | Co-current or counter-current flow of hot gases for heating. |
Applications | Cement production, metallurgy, waste treatment, chemical processing. |
Heating Types | Direct (flame/gases) or indirect (external heat source). |
Discover how a rotary kiln can optimize your industrial processes—contact our experts today!