A rotary kiln is a versatile industrial equipment used for high-temperature processing of materials. It is widely applied across industries such as cement, steel, mining, and waste management due to its ability to achieve extremely high temperatures (up to 2273 K) and ensure uniform temperature distribution. Rotary kilns are used for processes like roasting ores, sintering materials, calcining limestone and gypsum, reducing ores for sponge iron production, incinerating waste, and activating catalysts. Modern applications also include recycling scrap tires, processing ceramics, and upgrading phosphate ores. The electric rotary kiln is particularly suited for high-temperature oxidation and reduction reactions, making it essential in chemical and material processing industries.
Key Points Explained:
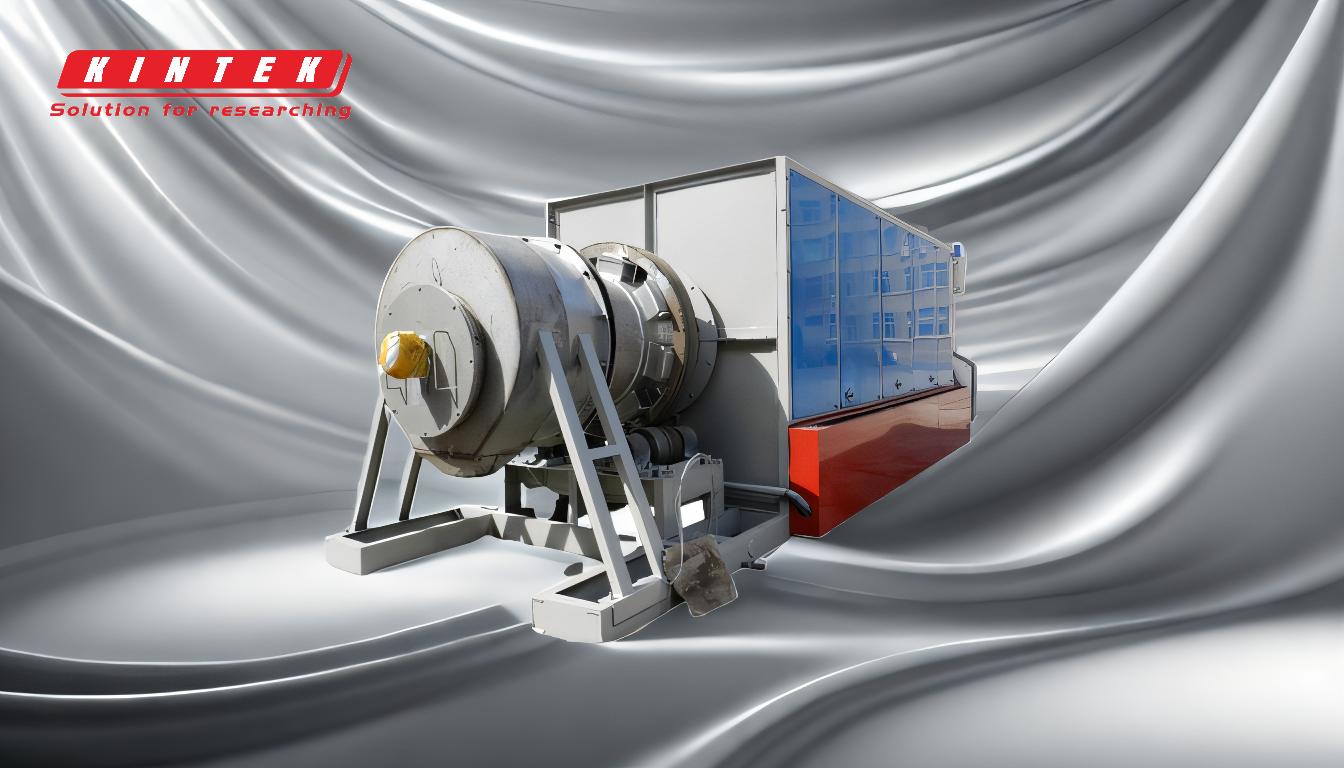
-
High-Temperature Processing:
- Rotary kilns are designed to achieve extremely high temperatures, up to 2273 K, making them ideal for processes requiring intense heat.
- This capability is crucial for applications like cement production, steel manufacturing, and ore reduction.
-
Uniform Temperature Distribution:
- The rotary motion of the kiln ensures that materials are well-mixed, promoting uniform heat distribution.
- This is essential for consistent product quality in processes like sintering, calcination, and roasting.
-
Versatility Across Industries:
- Cement Industry: Used for calcining limestone to produce clinker.
- Steel Industry: Employed in reducing iron ores to produce sponge iron.
- Mining: Applied for roasting ores and upgrading phosphate ores.
- Waste Management: Utilized for incinerating waste materials and recycling scrap tires.
-
Specific Applications:
- Roasting: Used for a variety of ores to extract metals.
- Sintering: Processes materials like dolomite and magnesite.
- Calcination: Converts limestone into lime and gypsum into plaster.
- Reduction: Produces sponge iron from iron ores.
- Incineration: Disposes of waste materials and sewage sludge.
-
Modern and Electric Rotary Kilns:
- Electric Rotary Kilns: Specifically used for high-temperature oxidation and reduction reactions involving materials like cobalt oxide, manganese oxide, and tungsten oxide.
- Modern Applications: Include catalyst activation, activated carbon production, and processing ceramics and plastics.
-
Environmental and Recycling Applications:
- Waste Recovery: Recovers waste lime and regenerates activated carbon.
- Soil Remediation: Desorbs soil contaminants.
- Recycling: Processes scrap tires and waste wood.
-
Chemical Processing:
- Oxidation and Reduction: Essential for chemical reactions requiring high temperatures.
- Molecular Sieve Roasting: Used in the production of chemical sieves.
- Calcining Granular Materials: Processes powders and granules for various industrial uses.
-
Specialized Industrial Processes:
- TiO2 Pigment Production: Used in the production of titanium dioxide.
- Mercury Production: Involves the volatilization of mercury from ores.
- Zinc and Lead Recovery: Extracts these metals from electric furnace dust.
In summary, rotary kilns are indispensable in industries requiring high-temperature processing, offering versatility, efficiency, and uniformity in heat distribution. Their applications range from traditional uses in cement and steel production to modern roles in waste management, recycling, and advanced chemical processing.
Summary Table:
Key Feature | Applications |
---|---|
High-Temperature Processing | Cement production, steel manufacturing, ore reduction |
Uniform Heat Distribution | Sintering, calcination, roasting |
Versatility Across Industries | Cement, steel, mining, waste management |
Modern Applications | Recycling scrap tires, processing ceramics, catalyst activation |
Environmental Uses | Waste recovery, soil remediation, recycling |
Chemical Processing | Oxidation, reduction, molecular sieve roasting |
Unlock the potential of rotary kilns for your industry—contact our experts today!